Metal rafters are more reliable and stronger than wooden ones, because they are able to withstand more significant loads. This article will discuss their main pros and cons, as well as the choice of material for metal rafters and their installation.
A metal rafter system is most often chosen to increase the rigidity of the roof, and is also used to create rafter systems that require the installation of a beam whose length exceeds 10 meters.
In this case, it is necessary to replace not only the rafters, girders and supports of the skates made of wood, but also the Mauerlat beam. Instead, a powerful channel is laid, the fastening of metal rafter legs to which is carried out using welded corners.
In practice, combined truss systems are also used - wooden with metal, which have a number of disadvantages.
The most important is the inadmissibility of contact between metal and wood, since with a sharp change in temperature, condensation forms on the surface of the metal, causing decay of the wood adjacent to it.
To avoid this, wooden elements should be treated with special antiseptic and moisture resistant agents. In addition, it is necessary to isolate wood from metal with the help of roofing material.
Separate consideration also deserves the insulation of the attic.
In the case of a metal rafter system, it is required to lay the material not between the rafters, as required by wooden truss systems, but under or above them.
In addition, between metal and roof insulation a gap should be left to prevent condensation from getting wet from the insulating material.
In the case of laying insulation under metal rafters, the remaining layers of the roof pie, such as the inner lining, vapor barrier material, roofing and ventilation gap, are located above the insulation layer.
This prevents heat loss from the attic space and the occurrence of cold bridges.
Another option is metal truss systems without the use of wood. In this case, the absence of wooden elements allows you not to be afraid of rotting.
This roof option is quite advantageous given the long service life and the possibility of using solid rafters rather large length (from 7 to 30 meters).
Metal rafters, which are also called trusses, can be either made independently or purchased ready-made.For their manufacture, periodic classical profiles, paired corners, etc. are used.
Farms consist of two sloping arms, which together form a triangle. The ability to block rooms of large area and height makes them most suitable for the construction of hangars and industrial buildings.
In the construction of residential buildings with a metal frame, metal roof trusses are also used, which in this case are made to order for a specific frame and delivered to the construction site.
Their installation is carried out together with the base.
In addition to the advantages of metal rafters listed above, their disadvantages should also be considered, which primarily include the delivery and installation of metal structures:
- Metal rafters have a rather large weight, therefore, to lift them to the desired height and installation, the use of special equipment is required;
- Steel trusses have poor resistance to high temperatures, therefore, in case of fire, after 15-30 minutes, they sag and the roof collapses;
- Finally, the construction of a metal rafter system is quite an expensive undertaking.
The choice of material for metal trusses
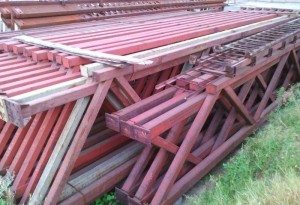
For the manufacture of truss elements, a paired profile is usually used, and kerchiefs are used to perform knot mates. The elements are connected by welding or riveting.
Before manufacturing a metal structure, it is necessary to calculate the cross section of the elements used, the number of welds, the required number of rivets, etc.
Farm production is performed as follows:
- For the manufacture of the upper belts of trusses, two unequal corners with a T-section are used, the docking of which is performed on the smaller sides.
- The lower belts are made using two isosceles corners.
- In the case of loads on the farm that occur within its panels, paired channels are used.
- For the manufacture of braces and racks, isosceles corners are used, the section of which is T-shaped or cruciform.
- For the manufacture of fully welded trusses, brands are used.
The truss truss, made of shaped pipes, received the greatest popularity in individual construction.
This truss has a significantly lower weight than structures made of channel, tee or angle, and its assembly can be carried out directly on the site by welding.
Useful: for the manufacture of trusses, bent or hot-rolled pipes are used. Hot-rolled pipes are produced using a steel strip of rectangular or square section, the thickness of which is 1.5-5 mm.
Steel Structure Roof
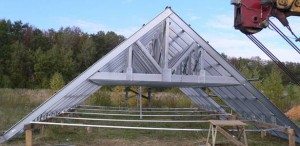
Steel roof structures are made from truss trusses designed for fairly long spans - from 6 to 30 meters.
Trusses are structures made of profiles with a periodic section, such as paired angles or bent-welded square or rectangular pipes.
roof trusses consist of two slopes, the slope of which is equal and is at least 20 degrees. To support them on the walls, special columns or reinforced concrete distribution pads with mortgages are used.
Runs from a wooden bar and corners, on which the crate will be stuffed, are attached to the trusses by welding. In order to increase the rigidity of this system, horizontal ties are made from a corner along the lower chords of the trusses.
In the construction of private houses, metal trusses are used quite rarely, more often they are used in civil and industrial construction for buildings such as:
- Factories;
- Factories;
- Warehouses;
- Hangars;
- Multi-storey public buildings, etc.
In the construction of residential private houses, trusses are usually used with a light modular steel frame.
The production of steel trusses is a fairly simple process that can be carried out in any industrial plant.
The main advantages of these designs are:
- High strength;
- Possibility of covering long spans;
- Good rigidity.
The disadvantages of steel trusses include:
- Large weight (20-30 kg/m2), requiring the use of special equipment during installation;
- Low fire resistance of the roof structure (15-30 minutes);
- Corrosion formation in the absence of special treatment.
An example of the installation of metal rafters
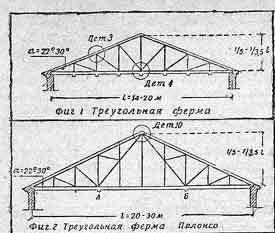
Consider, as an example, the installation of a metal truss structure for a roof, the angle of inclination of which is 22-30º, the roofing material is iron, slate or eternite:
- The most suitable option in this case would be a triangular truss truss, the height of which is 20% of the span length (Fig. 1 in the diagram). Its light weight allows you to build walls near its supports to a relatively small height within the attic;
- In the case when the span is 14-20 meters, it is recommended to choose a truss with downward braces due to the lightest weight of this structure;
- The length of the panel located in the upper belt of the truss should be selected in the range of 1.5-2.5 m;
- The number of panels in both parts of the truss must be even, according to the specified span size, the number of panels is 8.
In the case of the construction of an industrial structure, truss trusses are mounted on truss trusses that connect the supporting columns to each other and are the basis for the installation of trusses.
The length of the spans in such buildings reaches 20-35 meters, in connection with which Polonso trusses should be used (Fig. 2). This is a structure made up of two triangles connected to each other by tightening.
This makes it possible to eliminate long braces in the middle panels, the section of which must be increased to resist bending along, which will lead to an increase in the weight of the truss structure.
The upper belt is divided into 12 or 16 panels 2-2.75 meters long each. In the case of hemming the ceiling to the trusses, a puff is fastened to the nodes of the upper belt, the length of which is 4-6 panel lengths.
Even though the metal truss systems have greater rigidity and reliability than wooden ones, their use in the construction of country houses and cottages is most often not justified for a number of reasons.
The most appropriate is the use of metal rafters in the construction of industrial buildings, where the overlap of sufficiently long spans is required.
Did the article help you?