Sandwich panel roof is a universal solution both for the arrangement of prefabricated industrial facilities and for the construction of residential real estate. The relevance of the technology is explained by the tight deadlines, ease of implementation and affordable cost of building from a sandwich, or as they are also called sip-panels.
In this article I will talk about what this wonderful material is and how roofing systems are assembled with it.
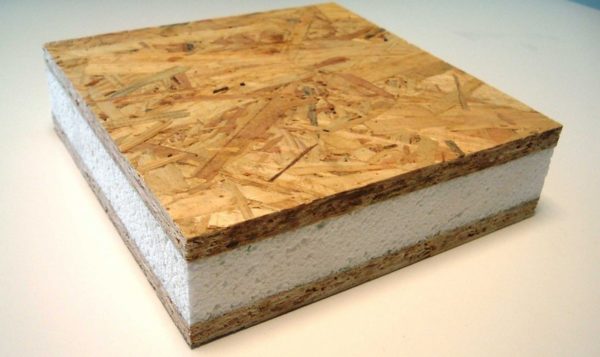
Basic information about building material
It is probably not a secret for anyone that a sandwich is a sandwich in which one or another filling is hidden between two pieces of bread. So, a sandwich panel is the same sandwich, but in a building way.
In accordance with GOST 32603-2012, a heat and noise insulating filler is located between two layers of rigid material.
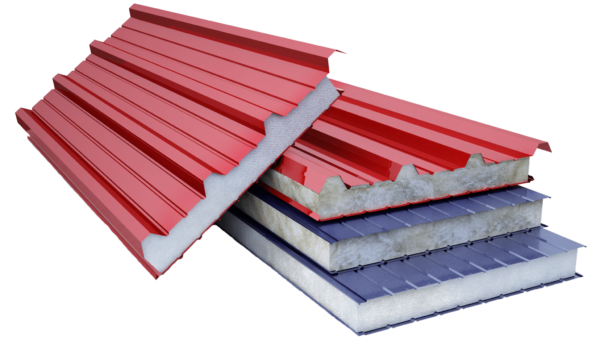
For example, for the assembly of roofing systems at industrial facilities, three-layer panels with an external sheathing of corrugated steel sheet are used. To protect against atmospheric precipitation, the metal sheathing is galvanized, painted, less often has a polymer coating.
The intermediate layer of such structures is made of mineral wool slabs or polymeric materials with a low degree of thermal conductivity.
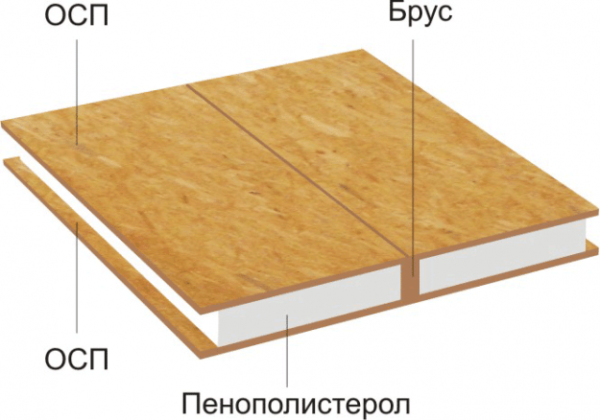
For the assembly of roofing systems on prefabricated frame houses, lighter panels are used with outer layers made of moisture-resistant oriented strand boards (OSB).
Despite the marking “moisture resistant”, such slabs do not withstand long-term contact with atmospheric precipitation, therefore, traditional roofing material, most often soft tiles, is laid on top of the structure assembled from panels.
Now a few words about the advantages and disadvantages of technology. Perhaps I'll start with the cons.
The only significant drawback of any sip panels is that they do not "breathe", that is, they do not let air through.This threatens with condensation, as the humid air from the room will not be able to go outside. However, the problem can be solved by a competent device of the vapor barrier and ventilation system of the under-roof space.
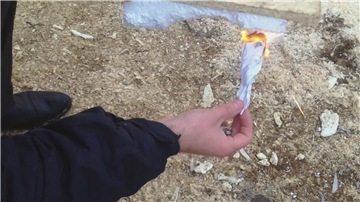
Among the advantages of the technology, I note the following:
- Simplicity and short terms of assembly of the roofing system due to the low weight and exact dimensions of the panels;
- Light weight of the finished structure and, as a result, a small load on the load-bearing walls and on the foundation;
- Possibility to carry out construction works all-season, as there are no wet processes as when using traditional building materials;
- Affordable price of a finished roof structure in comparison with similar structures assembled from other materials.
By the way, using sandwich panels, you can build warm roofs without an attic, which is difficult when using traditional technologies. This advantage will be appreciated by the owners of small houses, where the attic will come in handy.
Is it possible to assemble a roofing system from sip panels with your own hands? Of course you canwhen it comes to the construction of the roof of a residential frame house.
Features of construction work
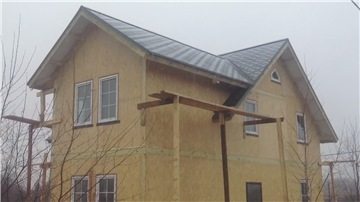
There is an opinion that the construction of roofs on small frame houses is carried out without a traditional truss system, that is, the strength of the structure is provided by panels and a lock connection between them.This is a gross mistake, since the lock connection will not provide adequate strength in relation to wind loads and the load of the snow layer.
Roof panels in a frame house are by no means independent structural elements, but just a heater fixed between beams and rafters.
In order to make it clear how a simple roof is assembled on a frame house, I bring to your attention a photo report and instructions for the work done.
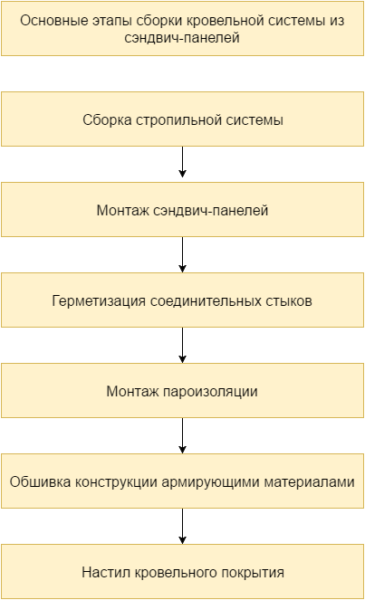
To perform installation work, we need the following materials:
- Glued laminated timber for a ridge device beams;
- Rafters as thick as a notch at the end of roofing slabs, their number is calculated by the number of vertical rows of sandwich panels on each slope;
- A bar with a thickness similar to the thickness of the sip-panel insulation;
- Trimmings of roofing slabs and a board for the device of side bevels;
- Polyethylene foam sealing tape;
- Self-tapping screws for wood;
- Mounting foam;
- Vapor barrier membrane;
- Board 100 × 25 mm for the construction of the crate;
- Oriented strand board OSB3 with a minimum thickness of 9 mm;
- Flexible tiles.
Roof system assembly
Roof assembly instructions are as follows:
- At the initial stage, a roofing system project is developed with the determination of the angle of inclination of the slopes and with the calculation of the total surface area;
- In accordance with the project, the number of building materials, fasteners and other consumables is calculated;
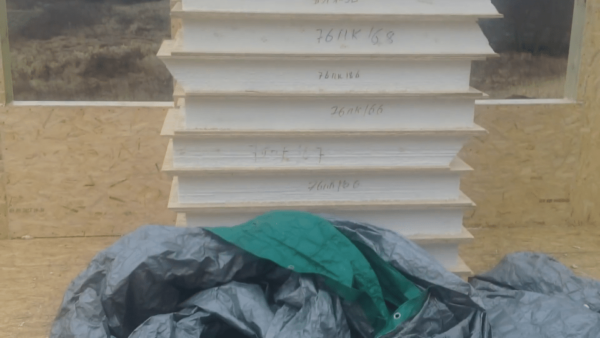
- Building materials are brought to the site and transferred as close as possible to the place of installation work;
- Gables rise from the panels;
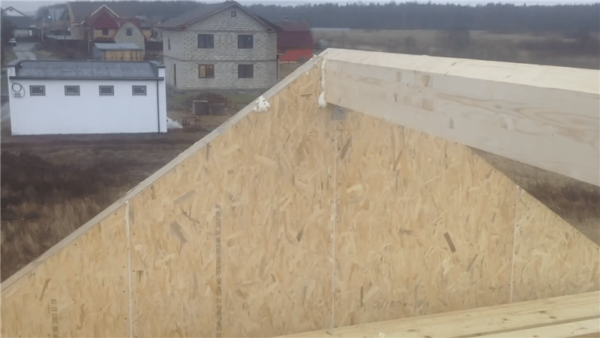
- A notch is made in the upper part of the gables, where a ridge beam made of glued laminated timber is installed with the help of a screw connection;
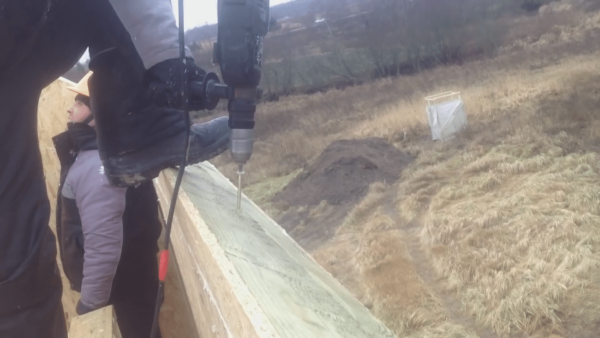
- Beveled structures made of panels and boards are arranged along the upper part of the side load-bearing walls, so that the slope made corresponds to the slope of the slope;
- All joints are foamed with mounting foam, and after the mounting foam dries, its excess is cut off;
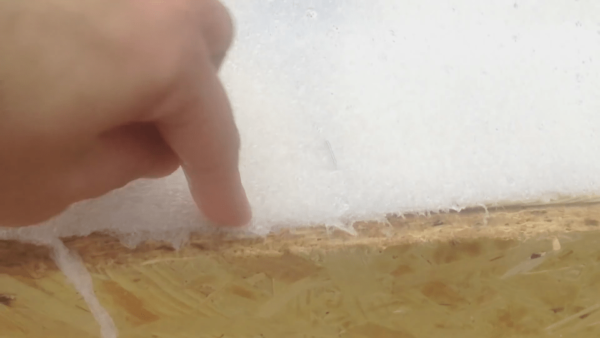
- Along the entire length of the ridge beam of the rafters and along the end of the gable, that is, in all areas that will be in contact with the roofing slabs, we lay a strip of polymer sealant;
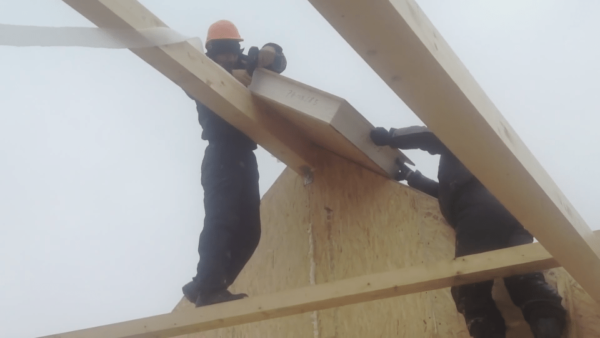
- We lay the first slab, starting from the ridge beam, fixing it with self-tapping screws to the beam itself and to the strapping board (end) of the pediment;
Roof slabs are produced taking into account the project of a frame house. But on the panel object, one way or another, you have to edit. Therefore, stock up on a jigsaw, a hacksaw and possibly a miter saw.
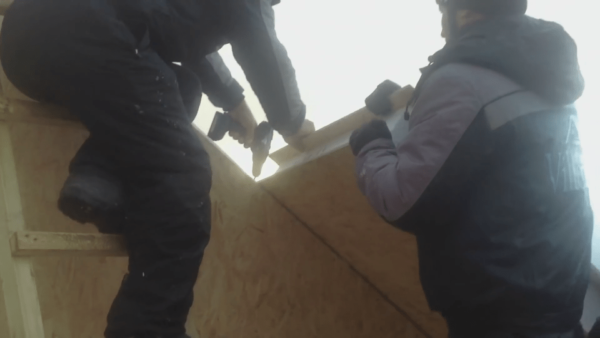
- Temporarily install the first panel, starting from the bottom beam and also fix it with one side to the bottom beam, and sideways to the end of the gable;
Do not forget to put polyethylene foam under the plates, as such a measure will eliminate the formation of cold bridges and extend the life of the roof.
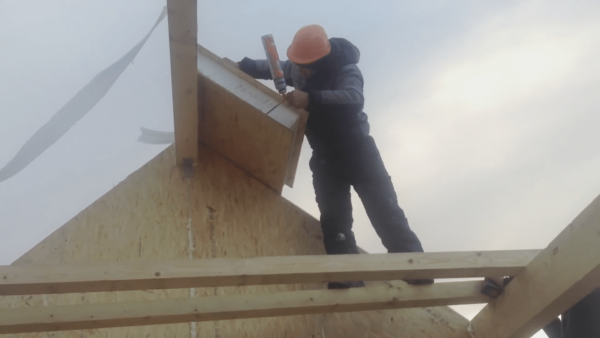
- We foam the end of the top panel where the rafter will be attached to it;
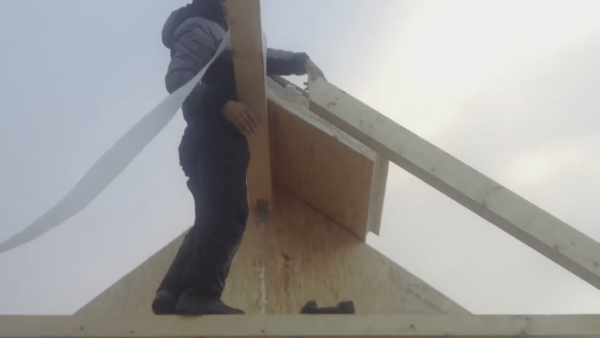
- We insert the rafter into the end of the first and last fixed plate and fix it there with self-tapping screws;
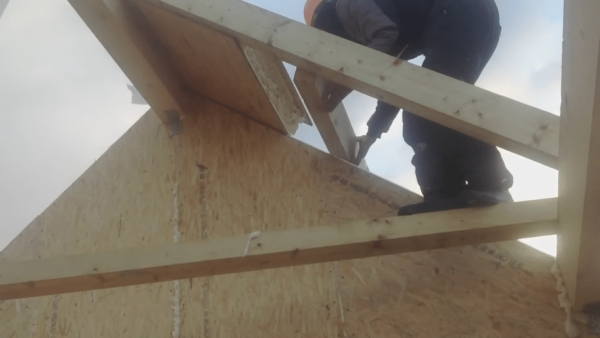
- Mounting foam is also applied to the free end of the plates, a beam is installed and fixed with self-tapping screws to the rafters and to the pediment strapping board;
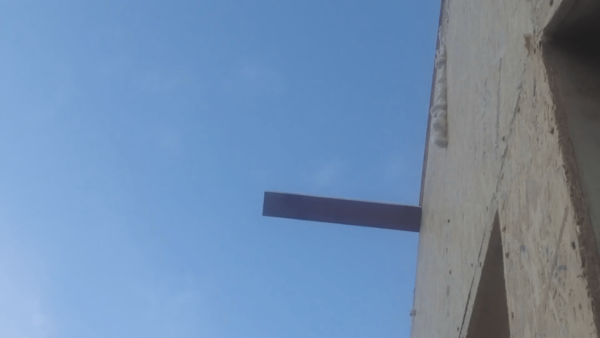
- We do not cut off the end of the beam that protrudes beyond the strapping board, but leave it for subsequent filing of the roof overhang;
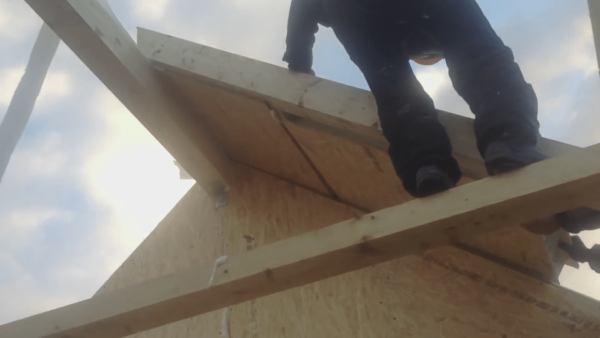
- In the same way, the roof slabs are installed in the gap between the first and last sandwich panel;
- In the upper part, the laid plates are passed along the end with self-tapping screws with a pitch of 100 mm;
- Pieces of timber similar to rafters are cut along the length of the installed panels;
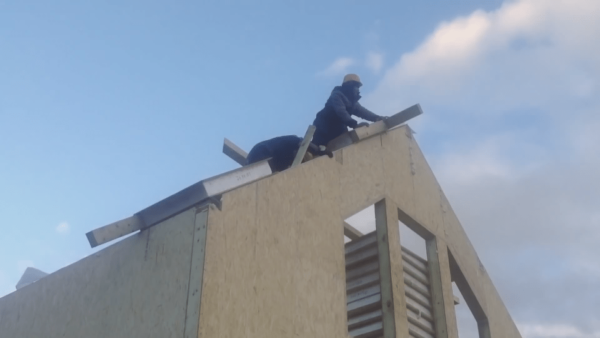
- Pieces of timber are inserted into the outer ends of the panels, into the gaps between the ends of the crossbars and fixed with self-tapping screws;
The external strapping of the beam along the gable is not flush with the wall, but with a protrusion of about 50 mm. This is necessary in order to subsequently cover the walls with siding or similar facing materials.
- We check all the gaps between the installed materials for the presence of mounting foam, and if there is none, we additionally blow it with foam;
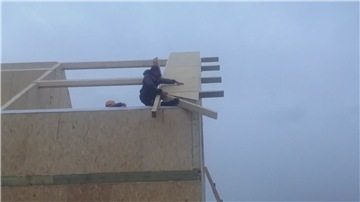
- The edge plate on the roof overhang is made of two triangular pieces, as shown in the photo;
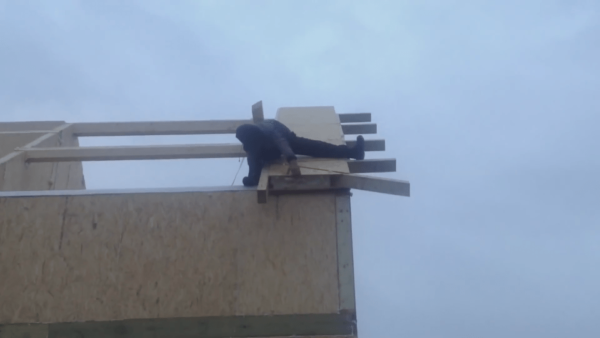
- Between the two triangular pieces of the sandwich panel, a piece of timber is installed, which is necessary for the subsequent sheathing of the roof;
- The remaining roofing slabs are installed in the same way;

- Along the overhang line between the rafter legs, we close the insulating layer of the sandwich with pieces of timber;
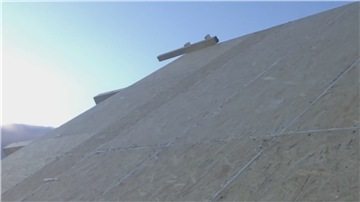
- After the entire roof slope is filled with slabs, we isolate the technological gaps from the outside with mounting foam;
After the foam has hardened, it is not necessary to immediately cut off its excess, because this can be done later when laying the roofing material.
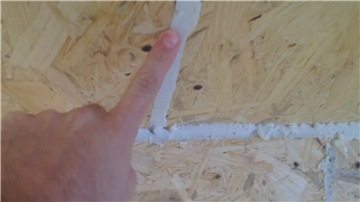
- On the inside, we foam all the technological gaps, and after the foam has completely dried, we cut off its excess;
- On the surface of the OSB, a vapor barrier membrane is lined with transverse strips with an overlap of 10 cm each other;
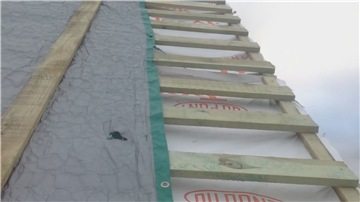
- A plank crate is stuffed over the membrane;
The construction shown in the photo was carried out in winter, so the crate was covered with an awning to protect it from atmospheric precipitation. If there were no awning, each working day would begin with a thorough cleaning of the snow in the space between the boards of the crate.
- On top of the crate, oriented strand boards are laid and fixed with self-tapping screws;
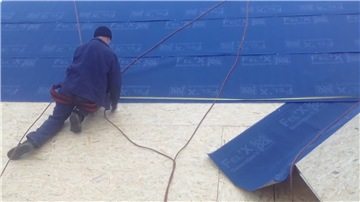
- On the surface of the laid plates, a lining carpet is laid under the flexible tiles and fixed with a stapler to avoid wrinkles;
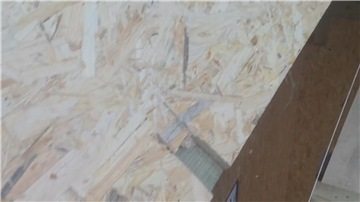
- At the same stage, notches are cut along the overhang line, as shown in the photo;
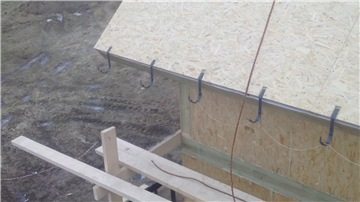
- Gutter holders are attached to these recesses;
The method of fastening the gutter was not chosen by chance. Firstly, the fastener sections can be closed with an end plate and flexible tiles, which means they will not be visible and everything will be neat. Secondly, the gutter will be located as close as possible to the overhang, which means that water will fall directly into it.
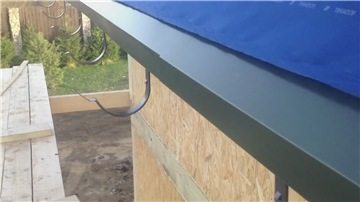
- An end plate is installed along the overhang line, which will cover the pieces of timber fixed at the ends of the sip panels.
On this, the construction of the roof from sandwich panels can be considered complete, which means it's time to start laying tiles.
Conclusion
Now you know what is the roof construction technology using heat-insulating sandwich panels. I hope the provided instructions will be useful to you. By the way, if you have any questions, ask them in the comments and besides that, do not forget to watch the video in this article.
Did the article help you?