In the modern construction of private houses and cottages, such an element as the use of reinforced concrete slabs for flooring is gaining more and more popularity, in particular, monolithic flooring over corrugated board. This article will tell you what it is, what is the difference between corrugated floors and ordinary floors, and how they are installed.
Monolithic ceilings on corrugated board are used in a wide variety of areas of construction, for example, in the construction of terraces and garages and a number of other buildings and structures.
Profile slab and regular slab
A monolithic ceiling on corrugated board differs from reinforced concrete, in which pouring is carried out using special formwork, in that the corrugated board allows you to get a finished ceiling as a result, which does not require additional work related to finishing or refinement.
The various profiles that are equipped with corrugated flooring are an important advantage of the floor, thanks to which its section can be made ribbed.
This allows you to significantly increase the strength of the floor, while simultaneously reducing the consumption of reinforcement and concrete for its construction.
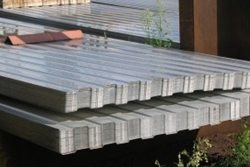
The floor plan of the corrugated board is that the corrugated board, which acts as a permanent formwork to which concrete will subsequently be applied, uses a metal frame as its support. And this frame consists of metal beams and columns.
The use of this design allows the use of lightweight materials with low strength for the construction of walls, because what is corrugated board - everyone knows.
This becomes possible due to the fact that interfloor ceilings from corrugated board transfer the load not to the walls, but directly to a sufficiently strong metal frame.
Useful: the material for the walls, if corrugated floors are used, can also serve as materials for thermal insulation, for example, foam block or aerated concrete.
Interfloor ceilings made of corrugated board have another equally important advantage. In the case of the construction of a large building, it is necessary to make a strip foundation, which requires quite significant costs of various building materials.
Transferring the load from the floor to the frame facilitates the walls, which also significantly reduces the load on the foundation. This makes it possible to perform, instead of a resource-intensive strip foundation, for example, a column foundation, the manufacture of which requires much less time and money.
In addition, each of the columns that make up the foundation will withstand the load from only one column of the metal frame.
A small grillage is poured into the heads of such a foundation (under the walls of lower weight along the entire perimeter of the building), to calculate the section of which the calculation of the thickness of the walls and the planned distance between the columns that make up the foundation are used.
At the same time, the corrugated flooring used in the plan makes it possible to actually reduce both labor and financial costs, as well as the time required for the construction of a building or structure.
Floor installation
Regardless of whether corrugated flooring or other material is used, its plan must necessarily include the calculation of this floor.
The following data is required to perform a correct calculation:
- The exact dimensions of the designed building;
- Calculation of loads created by the floor itself.
This data will help you choose the right dimensions for elements such as metal beams or columns.
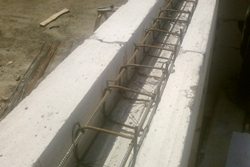
For the manufacture of columns, metal pipes are most often used, the cross section of which can be either round or square. As beams, metal I-beams or channels are most often used.
At the same time, the step of laying the beams, as well as the section chosen for them, directly depends on which corrugated board will be used in the construction of the floor.
Simply put - the greater the height of the sheet profile wall corrugated board, the smaller the step is chosen for laying the beams.
To perform the most accurate self-calculation of the distance between the beams, it is recommended to clarify the required information from the company in which the corrugated board was purchased.
The seller must provide all the necessary parameters of the material, list the main types of corrugated board, its characteristics, bearing capacity, etc.
Consider an example calculation:
- Let's say that the step of laying the beams is three meters. The brand of corrugated board used is TP-75, the thickness of the sheet is 0.9 mm.
- When determining the required length of corrugated board, it is recommended to calculate its support not on two beams, which is the most common option, but on three at once, which makes it possible to prevent sheet deflection in the future.
- The highest quality fastening of the sheet to the metal base of the beam is achieved by using special 32 mm (5.5) self-tapping screws equipped with a reinforced drill. Thanks to this drill, which allows you to drill a channel without pre-drilling them with a drill, self-tapping screws are also called armor-piercing. Fastening should be carried out at each junction of the profiled sheet and the overlapping beams. Accordingly, in the case of laying the sheet on three beams, fastening is carried out at three points, and when laying on two beams - in two places.
- In addition to attaching the sheets to the beams, they should also be fixed at the joints.In this case, the same armor-piercing self-tapping screws 5.5 can be used, but their length is chosen a little less - for example, self-tapping screws of 25 millimeters would be a good choice. Self-tapping screws are screwed in increments of about 40 centimeters.
- After the completion of the corrugated formwork for concrete, the concrete is directly laid. In terms of floors, the minimum thickness of this floor is always taken into account, which is most often seven to eight centimeters, excluding the thickness of the sheets themselves. For concreting, it is best to use concrete grade M-25, also referred to as M-350.
- Before proceeding with concreting, it is necessary to prepare the corrugated board, which consists in the fact that at the bottom, in the center of each span located between the beams, sticks are installed, starting from the floor and up to the corrugated board itself. The sticks are designed to prevent subsidence of corrugated board under the weight of the concrete lying on it. After the concrete has dried, temporary supports in the form of sticks are removed.
- It is recommended to perform concreting in one run, and if it is not possible to cover the entire covered area within one working day, then it is desirable to concret at least one span.
- If concreting was carried out in several stages, it is important to remember correctly how many days it will take to dry one or another span. This will allow timely removal of additional supports from under the dried concrete. Concrete reaches about 70-80 percent of the required strength only on the tenth or eleventh day from the moment of pouring in case of warm weather. In the winter season, the drying time of concrete increases to three to four weeks.
- In the event that work on the construction of ceilings from corrugated board is carried out in hot, dry weather, it is necessary to constantly wet the concrete. This prevents premature evaporation of moisture as a result of heating sheets of corrugated board under the influence of elevated ambient temperatures, leading to accelerated evaporation of moisture.
Like many other construction works, the construction of a monolithic floor for corrugated board is not particularly difficult.
Its most important stage is the theoretical part, which includes:
- The choice of material from which the metal structure of the frame will be made;
- The correct choice of the type and thickness of corrugated sheets;
- Competent selection of reinforcement sections used in the manufacture of the frame, etc.
It is recommended to entrust such calculations to a qualified specialist, and you can directly perform the construction work yourself.
The main thing at the same time is to strictly adhere to the plans and drawings developed in advance and comply with the requirements listed in the instructions.
In order to avoid various errors in the performance of these works, you can also resort to the help of a team of qualified workers with good reviews and a reputation.
Did the article help you?