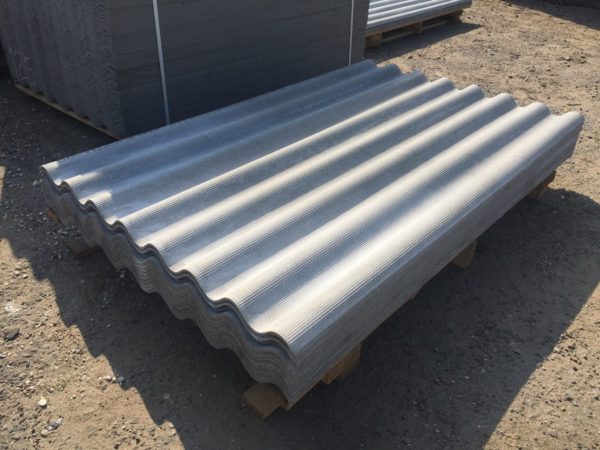
Wave slate can be considered perhaps the most popular roofing material in the economy segment. In this article, I will give a brief overview of the main varieties of slate, analyze their strengths and weaknesses, and also describe in detail the technology for installing a slate roof.
Material overview
Varieties in composition
Slate is a sheet roofing material, or rather, a group of materials. Depending on the composition, several varieties of slate are distinguished:
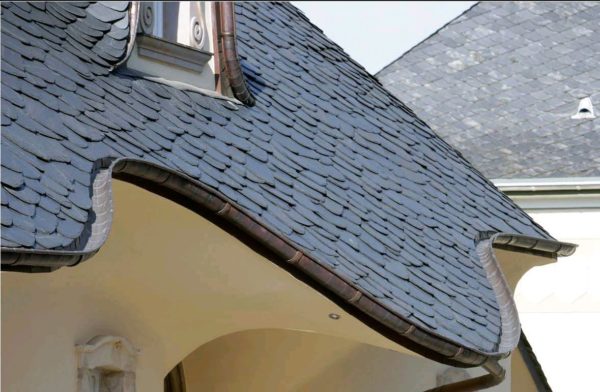
- Natural (natural, slate) slate - plates obtained by splitting a slate monolith. After trimming and processing, they can be used for roofing.
- Asbestos-cement slate - the most common variety (this is what they usually mean when they talk about slate). Produced on the basis of chrysotile or amphibole asbestos with cement as a binder.
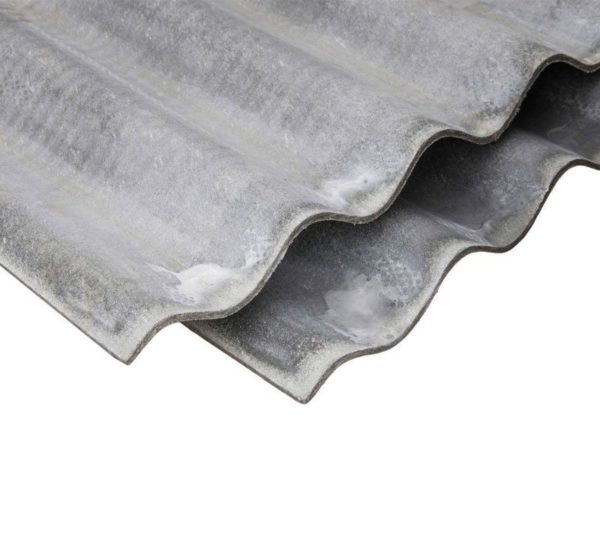
Slate based on amphibole materials was previously produced in the EU countries, but today the use of such raw materials has been abandoned due to its potential danger as a carcinogen. Chrysotile asbestos is still used, but the market share of such materials is gradually decreasing.
- Fiber cement (non-asbestos) slate. Instead of asbestos fiber, cellulose, jute, acrylic threads, etc. are introduced into the composition of slate. Mineral fillers are also added to the binder to increase mechanical strength. The advantages of asbestos-free materials are environmental friendliness and lighter weight.
- Polymer sand slate - sheet material, the basis of which is a polymer binder. Screened sand is used as a filler, to which various additives and pigments are added.
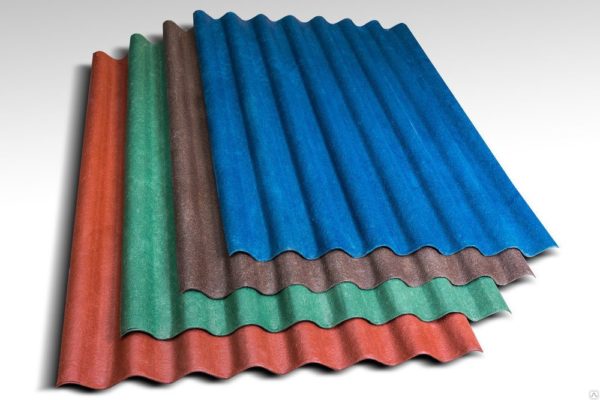
- Euroslate – flexible material based on bitumen/polymer binder with fabric or cellulose base. Produced under the brands "Ondulin", "Aqualine", "Nulin", etc.
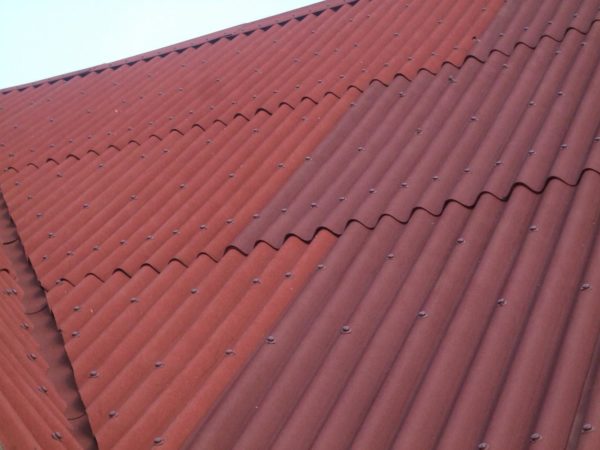
Also to this group can be attributed - albeit in many respects conditionally:
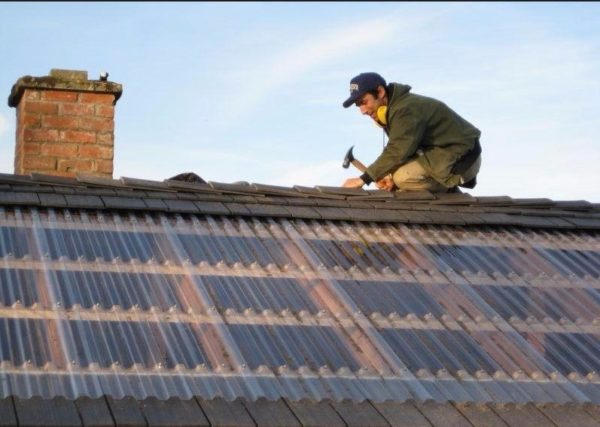
- polycarbonate slate - made of polycarbonate in the form of transparent or translucent sheets. It can be either colorless or tinted, it has good thermal insulation properties and significant decorative potential.
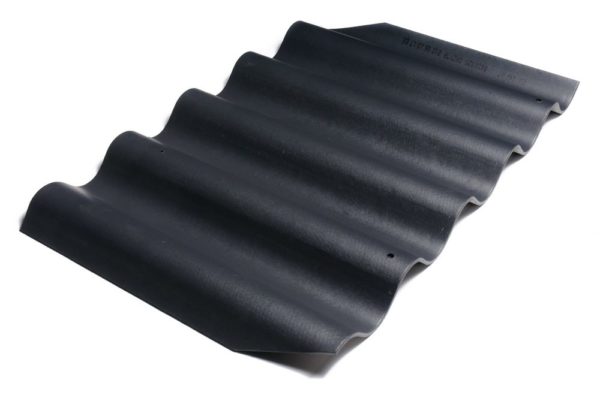
- rubber slate. The base is fiberglass, the binder is rubber processing waste. The coating will be elastic and moisture resistant.
- metal slate - another name for corrugated board (profiled metal sheet with anti-corrosion coating).
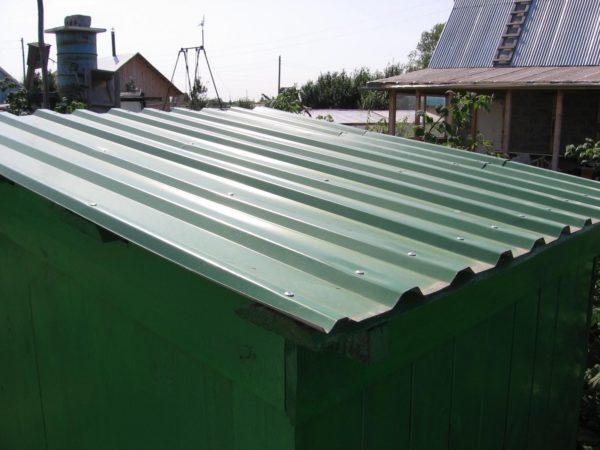
And yet, if in the text of an article or a regulatory document you come across the word "slate" without additional clarifications, then most likely it will be about the asbestos-cement variety of the material or its non-asbestos modification.
Sheet shape
In addition to the classification by material, it is also worth keeping in mind the division according to the shape of the sheets. As a rule, slate is produced in two forms:
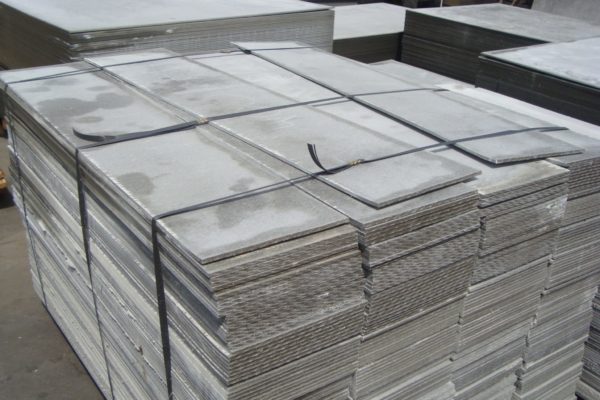
- slate flat – GOST 18124-95 “Asbestos-cement flat sheets. Specifications";
- slate wavy – GOST 30340-95 “Asbestos-cement corrugated sheets. Specifications".
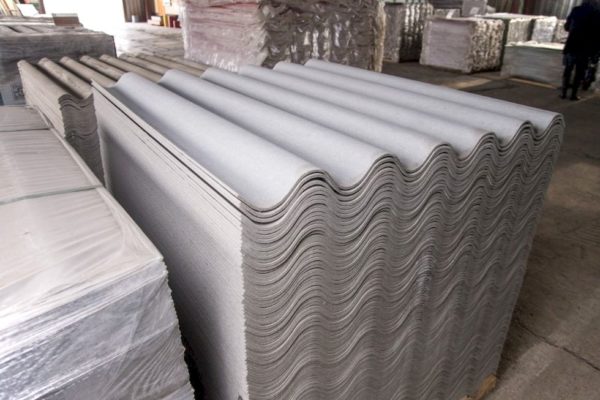
Corrugated products are more common as they are much better suited for roofing applications. Flat materials are also used, but due to their lower strength (there are no stiffeners), they are more often used for sheathing horizontal surfaces.
The main parameters are the number and dimensions of the waves:
- By the number of protrusions on one sheet, five-, six-seven- and eight-wave slate is distinguished.7 and 8 waves are optimal for private construction, 5 and 6 - for the roof of industrial buildings.
- Slate grades determine the height of the wave and its step. So, brand 40/150 has waves 4 cm high with a step of 15 cm, brand 54/200 - 5.4 cm by 20 cm, respectively.
In addition to the number of waves and their dimensions, the wave profile can also differ:
Profile type | Marking | Dimensions, mm | ||
length | width | thickness | ||
Ordinary | IN | 1120 | 680 | 5,2 – 7,5 |
unified | HC | 1750 | 1125 — 1130 | 5,2 – 7,5 |
reinforced | WU | up to 2800 | 1000 | 8 or more |
When selecting roofing materials for arranging the roof of a private house, it is advisable to purchase VO or UV slate. Its strength is sufficient, but it costs much less than products with a reinforced profile.
The price of VU slate is higher (about 300 rubles per sheet versus 175 - 200 rubles for a standard one), so it is purchased mainly for roofing industrial facilities.
Use as a roof
Advantages
Wave slate has the following advantages:
- Mechanical strength. The combination of a cement binder with asbestos or fiber filler gives roofing sheets significant mechanical strength. In any case, with a fairly modest thickness (up to 8 mm), you can walk on the laid slate.
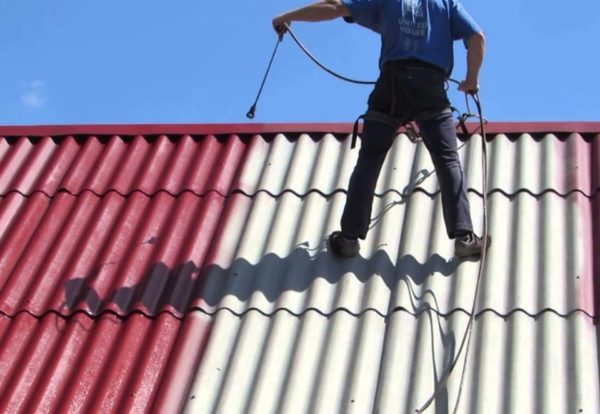
- Thermal conductivity. The structure of the material ensures its low thermal conductivity. Of course, it will not work as a full-fledged heat insulator, but in the heat the roof will heat up much less than metal.
- Moisture and corrosion resistance. This provides the composition of the slate.
- Lifetime. A properly equipped roof will last at least 20-25 years.Moreover, if one sheet of roofing material is damaged, it can be simply replaced without redoing the entire roof.
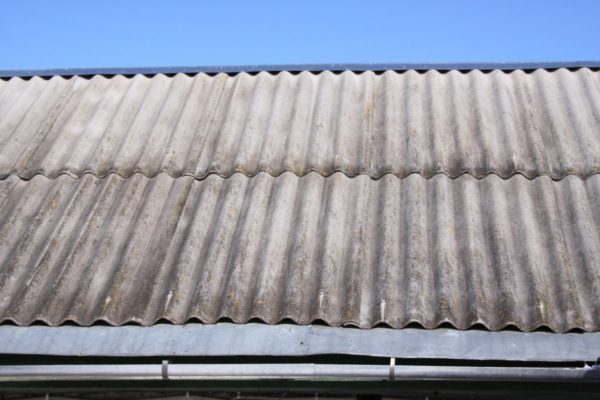
- The material is not flammable. In addition, when burned, slate does not emit toxic substances.
And yet, the main advantage is the acceptable cost of products: if you are looking for ways to minimize the cost of roofing, then the choice will be quite obvious.
Flaws
This building material also has a number of disadvantages:
- Fragility. This is the main operational disadvantage, which is due to insufficient elasticity. Sheets can crack both during transportation and processing, which increases the reject rate.
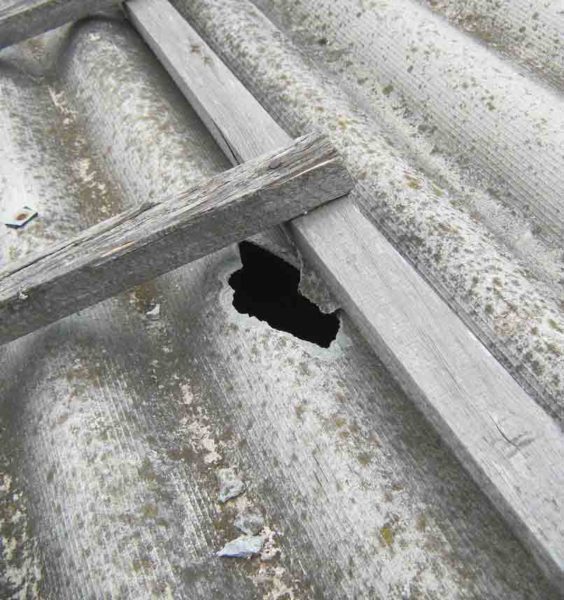
Hence the obvious conclusion: when buying slate, you need to make more stock than in the case of other roofing materials.
- Weight. Asbestos-cement sheets, especially reinforced ones, weigh a lot (from 23 to 35 kg). And if we take into account the significant dimensions of the product, then the problem with lifting to the roof becomes obvious.
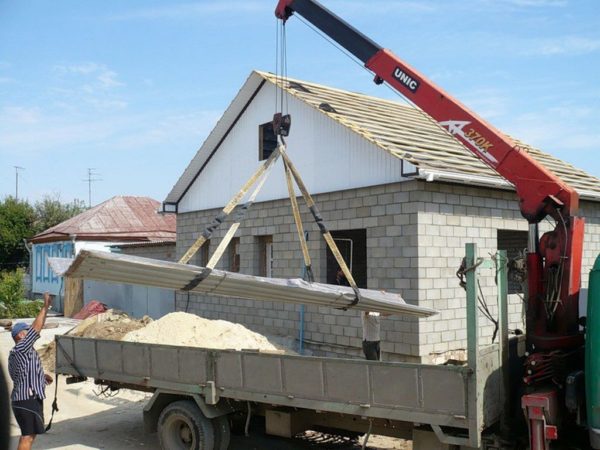
- Porosity. The porous surface of the material absorbs rain and melt water, which significantly reduces its service life. With temperature fluctuations, this can lead to cracking of the sheet, but usually everything is limited to a gradual overgrowth of moss. To avoid this, it is necessary to treat the slate with special compounds with an antiseptic.
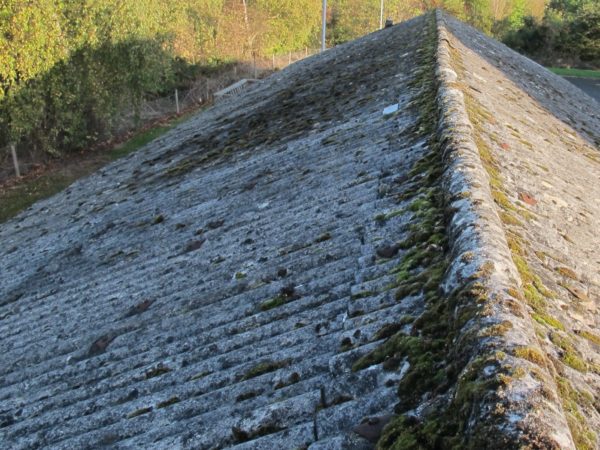
- Interaction with fire. Slate does not ignite, but cracks intensively in case of fire.Flying fragments can cause injury or fire in neighboring buildings.
And yet the main disadvantage of this material is its potential carcinogenicity, due to the presence of asbestos in the composition of the slate. This question is quite voluminous, therefore I will devote a separate section to it.
A few words about toxicity
The degree of danger of asbestos-cement slate depends on which mineral in the composition is used as a filler. There are two options here:
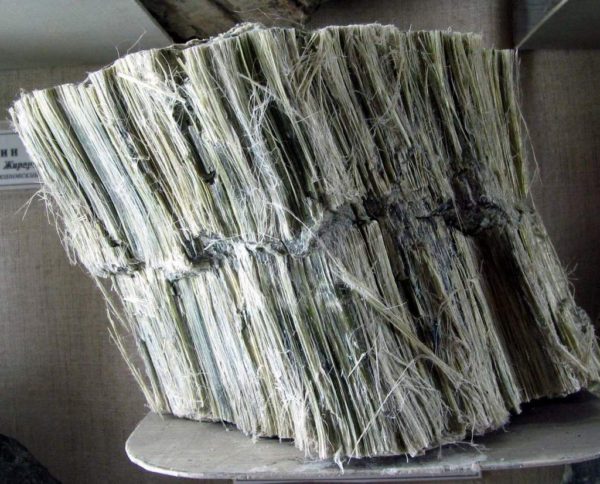
- Chrysotile asbestos - used in the production of roofing materials in the USA, China, Russia, Ukraine, Belarus and other countries. Alkali-resistant, but susceptible to acids.
- Amphibole-asbestos - previously used in production in Europe. Resistant to acid, but reacts with the alkaline environment of the cement slurry.
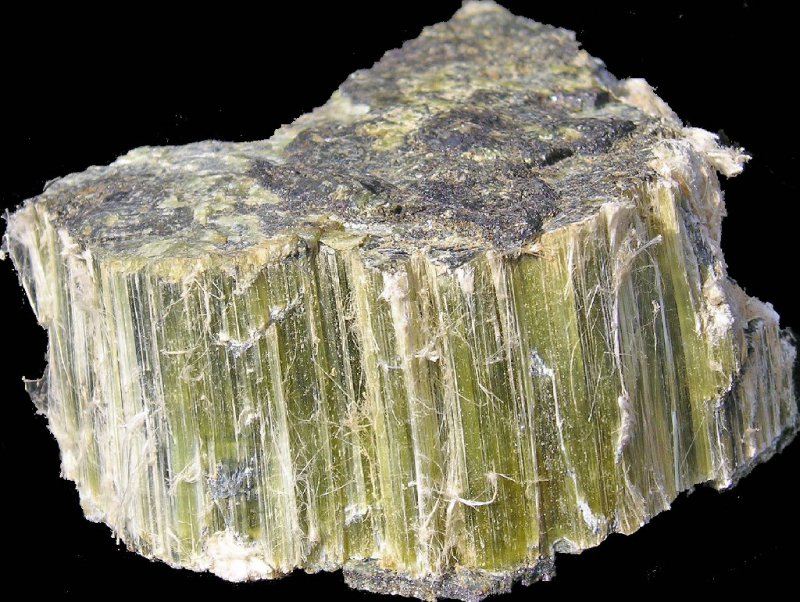
This is where the root of the problem lies:
- The point of view about the high carcinogenicity of slate containing asbestos was formed in Europe. And it is absolutely fair: amphibole materials really cause oncological diseases, and there is no way to compensate for the harm from them.
- Chrychzotile asbestos, used in the production of domestic building and roofing materials, can also have a carcinogenic effect. But its activity is much lower, because negative consequences can occur only if used incorrectly.
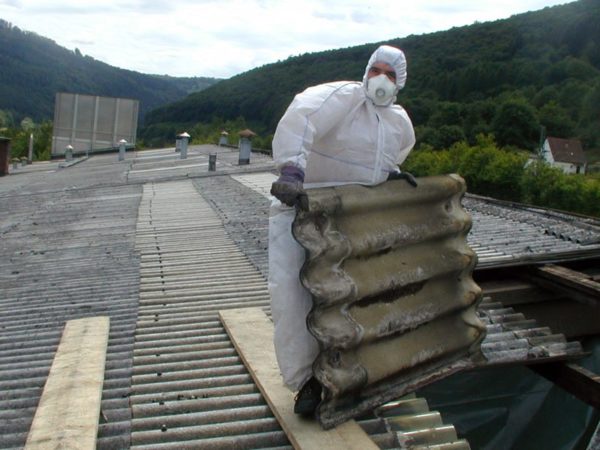
- Studies show that asbestos-containing slate can be used in roofing, provided that the premises are reliably isolated from chrysotile dust.But for interior cladding, flat sheets are undesirable.
Thus, if you buy slate in Moscow or another city in the Russian Federation, then most likely you should not worry. Of course, it is better to clarify the composition of the material and the origin of the raw materials, but still the danger of an asbestos-containing roof is, to put it mildly, exaggerated.
Slate roof installation technology
Stage 1. Tools and supplies for work
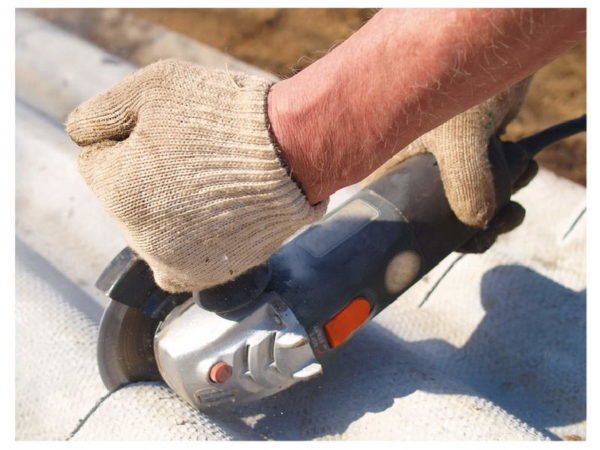
Despite the significant mass and a certain fragility, slate can be laid with your own hands. When installing a roof from this material, we will need:
- Saw on wood.
- Hammer.
- Screwdriver.
- Bulgarian.
- Drill.
- Hacksaw for metal.
- Stairs (one for lifting, the second for moving along the slopes of the roof).
- Ropes with hooks for lifting materials to the roof.
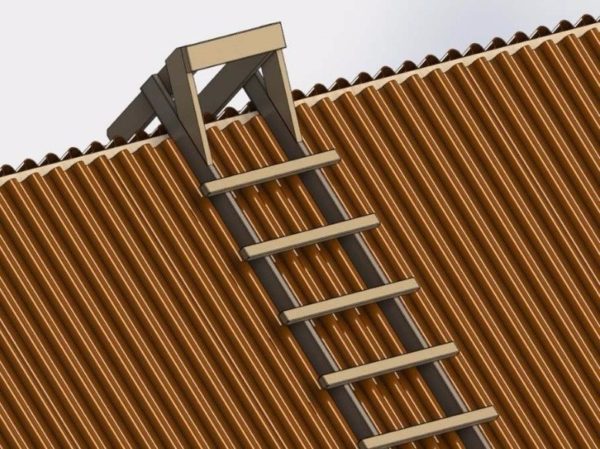
We will also need consumables:
- Bars or boards for crates.
- Waterproofing (roofing material or roofing membranes).
- Impregnation for wood (moisture protective + antiseptic).
- Paint for slate.
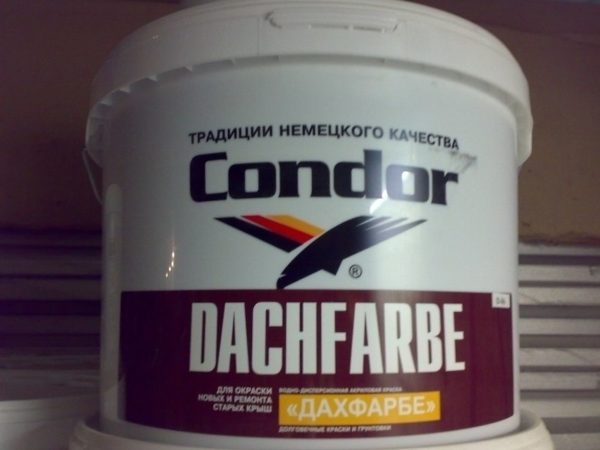
- Fasteners (nails or self-tapping screws for lathing, slate nails or special self-tapping screws with galvanized washers).
Naturally, we need to purchase the slate itself. The purchase volume is determined as follows:
- We measure the length of the slope along the eaves, divide the resulting number by the width of the sheet and add about 10%. So we get the number of sheets in one row.
- We measure the distance from the ridge to the eaves along the slope, divide by the length of the sheet and add about 13% for the overlap.
- We multiply the obtained numbers by each other and calculate the number of sheets for one slope.
- All roundings are done up, not to join the sheets, but to use the maximum number of integer elements.
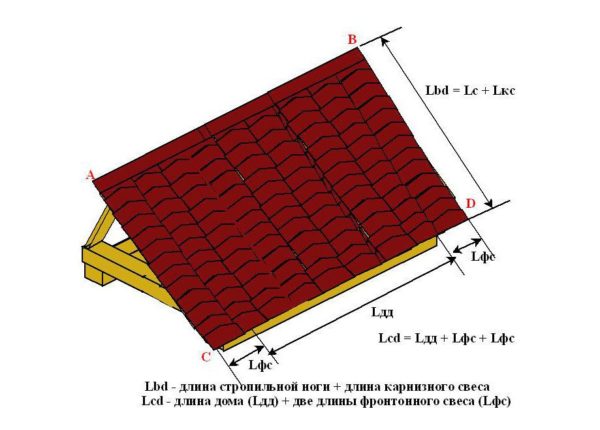
This calculation is suitable for rectangular slopes. When buying slate for a roof of a different shape, you need to make the appropriate amendments.
Stage 2. Preparation of the base and material
Instructions for creating a roof begin with a description of the lathing device. In order for slate to provide a sufficient level of reliability and waterproofing, it must be laid on an appropriate base. The parameters of the crate depend on the angle of the slope:
Slope angle, degrees | Lathing pitch, mm | Horizontal overlap | Vertical overlap, mm |
to 10 | solid | two waves | 300 |
10 — 15 | 450 | one wave | 200 |
over 15 | 600 | one wave | 170 |
We make the crate according to standard technology:
- For manufacturing, we take even and durable pine beams. section from 50x50 mm or boards with a thickness of at least 30 mm. We make the ridge beam more massive - at least 50x100 mm.

- We treat all parts with an antiseptic to prevent rotting and damage by carpenter beetles.
- We mount the crate, fixing the bars and boards on the rafters. For fixing, we use long nails or phosphated wood screws.
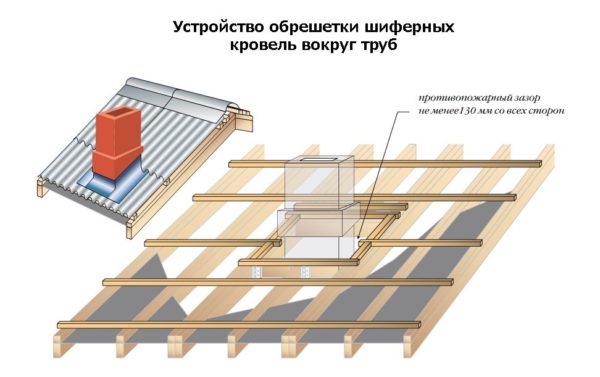
- In the valleys and at the points of junction with vertical surfaces (walls, chimneys, etc.) we fix additional batten boards. This is done in order to create a more reliable foundation and provide protection against leakage.
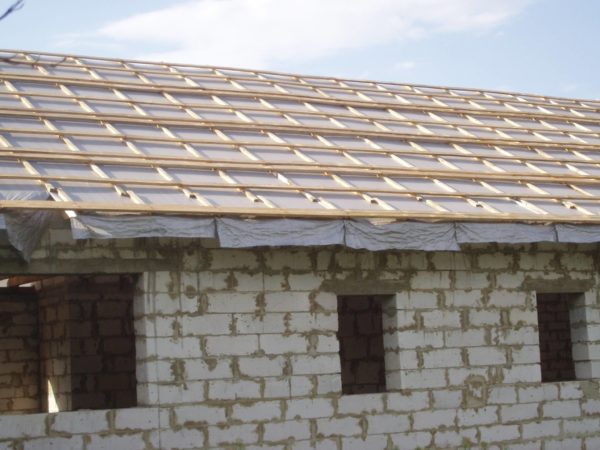
- We lay waterproofing material on top of the crate. As a waterproofing, a relatively cheap roofing material is usually used, but more reliable roofing membranes can also be taken.
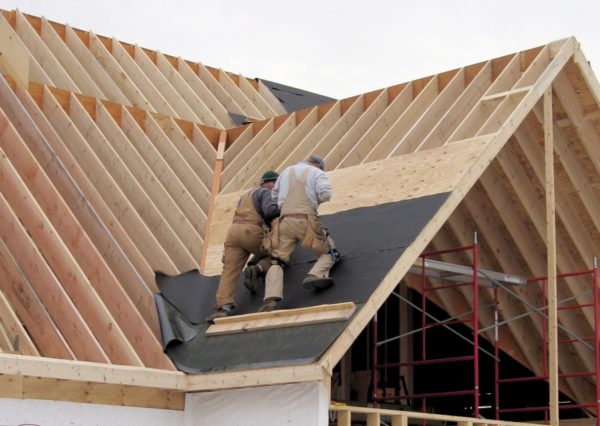
Sometimes waterproofing is laid under the crate, directly on the rafters.
It is also necessary to prepare the roofing material itself:
- Slate cut to sizebased on previous calculations. It is undesirable to use fragments less than 60 cm long - in this way the material loses a significant part of its characteristics. In this case, to compensate for the dimensions, it is better to increase the overlap.
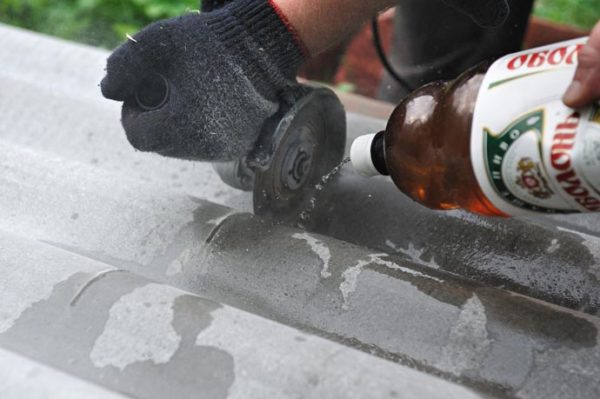
- We process the cut lines with water-dispersed paint - so the material will not crumble and exfoliate under the influence of moisture.
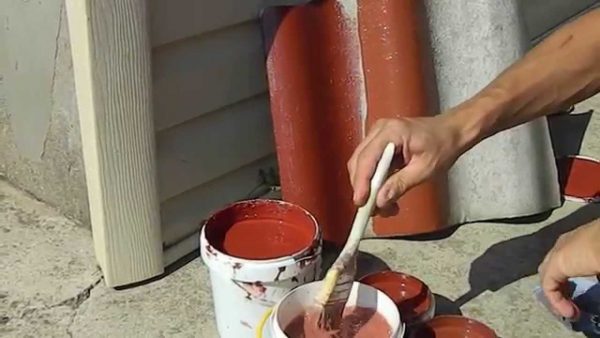
- Sometimes the entire plane of the sheet is painted: in addition to improving the aesthetic qualities, this treatment protects the material from moss fouling. In addition, rain and melt water flows better from a roof slope painted or treated with water-repellent impregnation. This helps to reduce the risk of leaks.
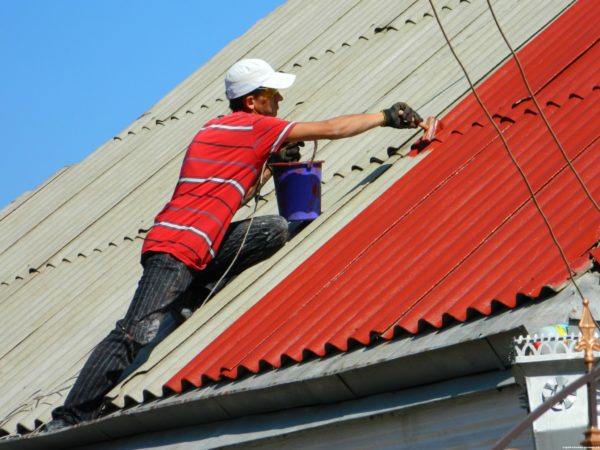
- We drill slate in places of fastening. The diameter of the hole should be slightly larger than the diameter of the fastener.
Both drilling and sawing slate is possible only with gloves, goggles and a respirator. It is also desirable to moisten the treatment site to reduce the amount of asbestos-cement dust.
After completing these operations, you can start laying the roof.
Stage 3. Slate laying technology
You need to lay the slate from the bottom up, starting from one gable ledge and gradually moving towards the other.The laying direction is chosen against the direction of the most frequently blowing wind: so the air will not be blown under the overlap, tearing the sheets from the crate:
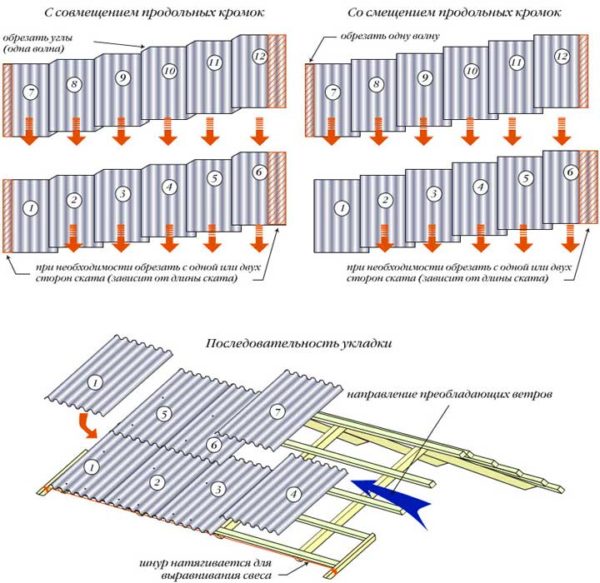
- We stretch the cord along the eaves, which we will focus on when aligning the sheets.
- We raise the slate to the roof either with a ladder or on ropes with hooks.
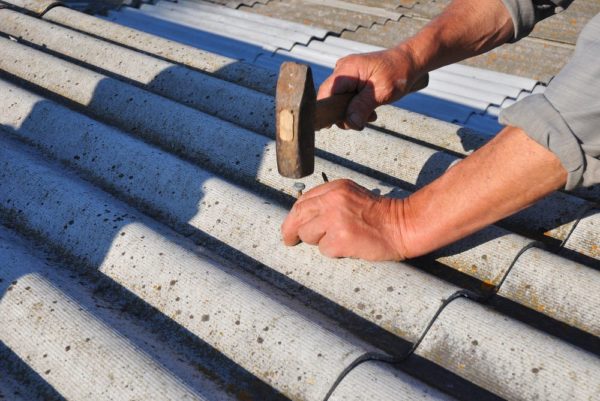
- Lay the sheet on the crate, align it and fix it with nails or screws.
- Usually, eight-wave slate fastening performed in the second and sixth waves, seven-wave - in the second and fifth, counting from the edge or overlap. For each wave, two attachment points are needed, the distance from which to the edge of the sheet should be maintained at least 150 mm.
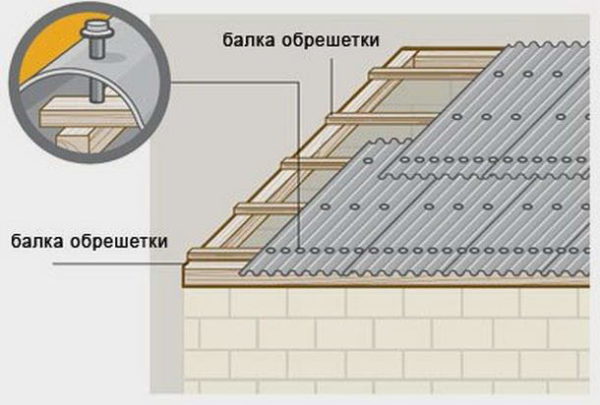
- We fasten not to the stop, making sure to leave a minimum gap between the head/washer and the sheet surface.
- We do not bend nails from the inside of the slope. Thanks to this, the roof will retain mobility, and the slate will not crack during temperature deformations.
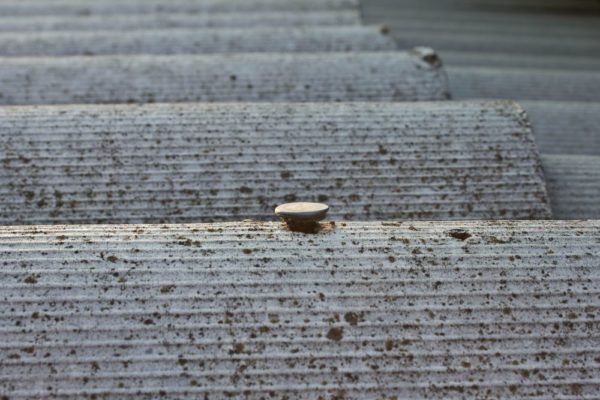
- When laying "out of the way" the slate is placed so that the vertical joints between the sheets in the rows do not match. To do this, we start each even row by mounting half of the sheet, which will provide an offset.
- When laying "with cutting corner" in the place where the edges overlap, one corner of the sheet must be cut off (see diagram). The standard cut size is 103 mm in width and 120 or 140 mm in length.
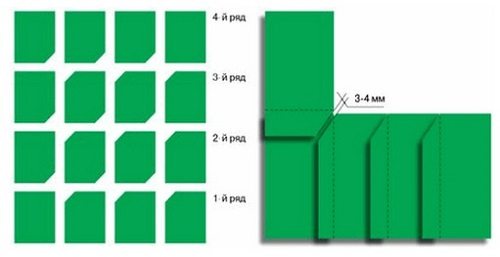
- According to this algorithm, we gradually mount the slate over the entire area roof slopes.
- After that, we make out the junctions to the vertical surfacesby installing protective aprons made of galvanized steel sheet.
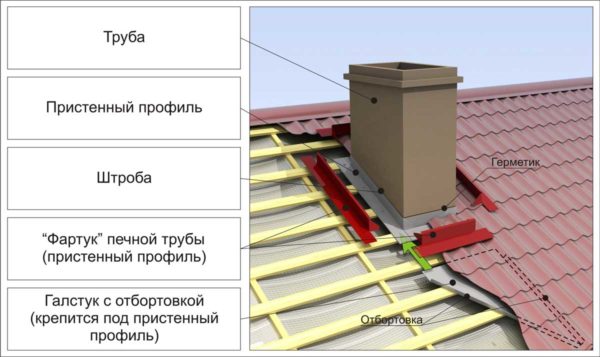
- In the upper part, we attach a skate to the ridge boardmade of metal profile. The ridge overlay should completely cover the edges of the slate sheets to avoid leaks.
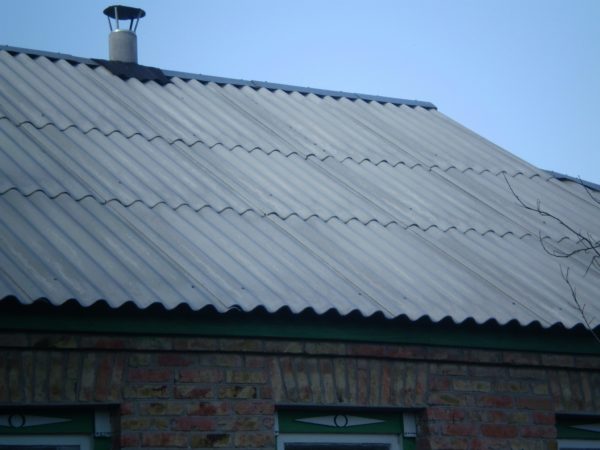
Both under the ridge and under the protective aprons, additional waterproofing can be laid.
Slate Roof Repair Tips
One of the advantages of slate roofing is its maintainability. And if, in the presence of large defects, the slate is simply replaced with a whole sheet, then small cracks can be eliminated with less labor:
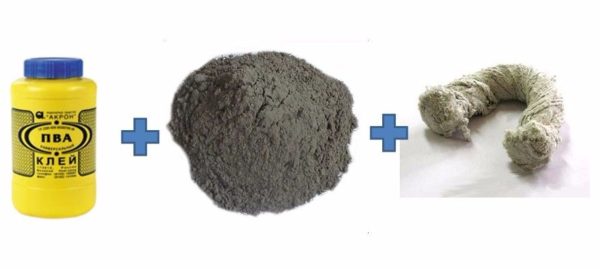
- In dry form, mix M300 cement and fluffed asbestos fiber. Instead of asbestos, you can take jute or cellulose.
All work with asbestos - only in glasses and a respirator!
- We mix joiner's PVA and water in a ratio of 1: 1. We add the cement-asbestos mixture to the resulting solution.
- We bring the product to the consistency of thick sour cream.
We carry out the repair process itself as follows:
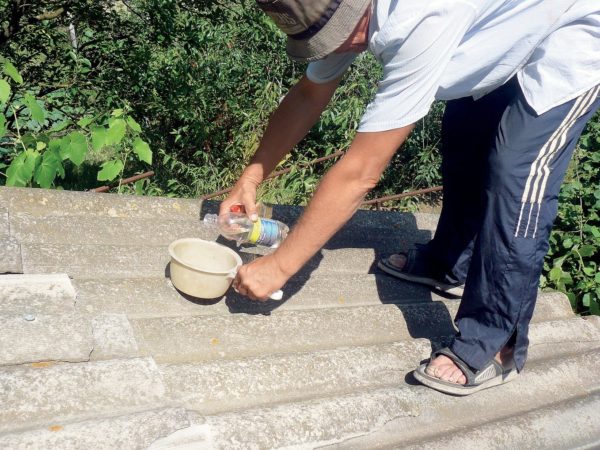
- We clean the roof of dust and debris, then rinse the roof with water from a hose. Thoroughly dry the area to be repaired.
- Cracks and other defects primed PVA glue, diluting it with water in a ratio of 1: 3.
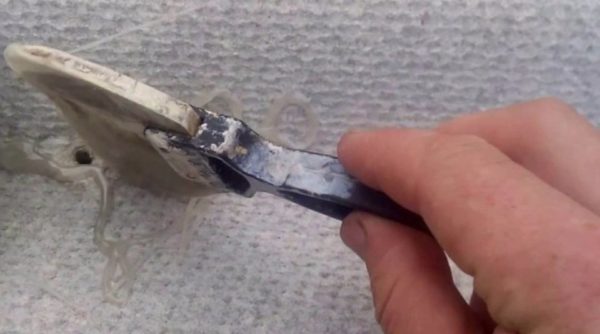
- We fill the defects with a repair mixture, laying it in layers no thicker than 2 mm. You may have to repeat the operation several times to completely resolve the problem.
- It is advisable to repair the slate roof in cloudy weather. So the cement composition dries more slowly and has time to gain strength.
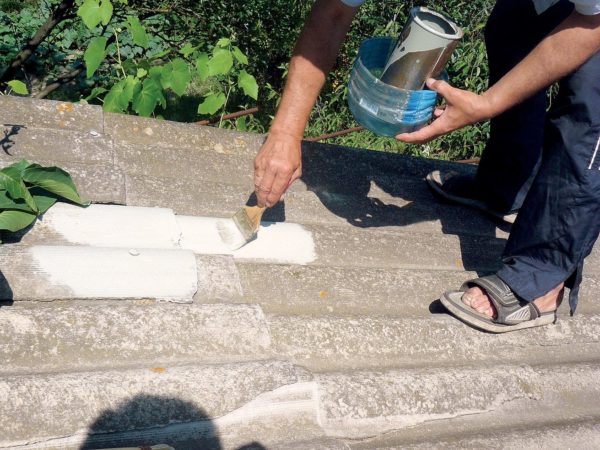
As practice shows, after such a repair, slate may well last 5-7 years without replacement, because the financial efficiency of the event is obvious. True, darker spots remain on the surface after repairs, but let's be honest - we usually choose slate not for its beauty!
In addition, after repair, the roof can be painted - this will not only hide defects, but also give the surface a more aesthetic appearance.
Conclusion
Having figured out what slate is made of, evaluating its pros and cons, and having studied the installation technology, you can successfully use this material in roofing. You can learn the basics of the technique described above by watching the video in this article. And all the questions you have will be answered in the comments.
Did the article help you?