The market for modern materials for construction is constantly updated with new samples that allow you to get the best results at a minimum cost. PVC roofing is a prime example. Consider what materials are used to create such coatings and what are their advantages.
The main requirements for roofing are reliability and durability.
Roofing is an expensive type of repair, so every homeowner wants to choose a type of roofing that can last for a long time without requiring repairs.
The coatings from which pvc roofing is created have quickly gained popularity due to their unique performance qualities.
Among the main advantages:
- High reliability;
- Elasticity;
- Excellent adaptability to a variety of climatic conditions;
- High resistance to damage such as puncture and stretching;
- No need for costly maintenance during operation.
Polymer membrane roof
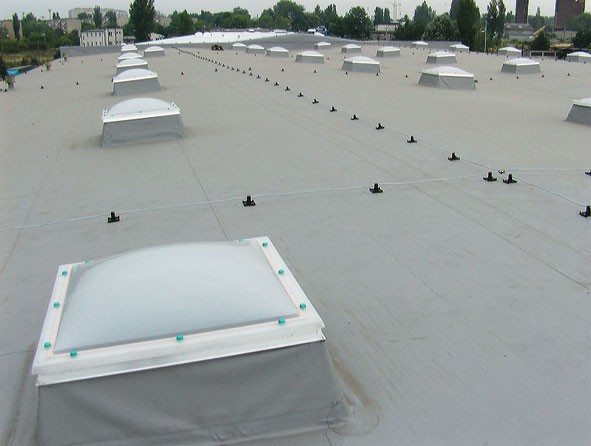
Roofing membranes made of polymeric materials are very popular. This material allows you to create not only very reliable, but also very attractive roofing coatings.
This is facilitated by a variety of colors, as well as a large width of the roll material, which allows you to get by with a minimum number of seam joints.
Types of polymer membranes
Modern builders use mainly three types of polymer membranes, these are:
- EPDM (EPDM);
- TPO (TPO);
- PVC-P (PVC).
The oldest and most widely used material is synthetic rubber (EPDM) membranes. The first roofs made from this material (in Canada and the USA) have been in operation for about forty years. The membrane is lightweight and highly elastic.
Installation of this roofing material carried out using a special self-adhesive tape or glue.
PVC membranes are a high quality material characterized by elasticity and durability. As a rule, PVC roofing is created from membranes that are reinforced with polyester mesh.
The connection of individual layers is carried out by hot air welding. The top layer of the membrane contains additives that increase the resistance of the material to solar radiation and atmospheric influences.
TPO membranes are a polymer material based on rubber and polypropylene. As a rule, for membrane roofs reinforced membranes are used, which are characterized by high strength. Seams on this material are created by welding.
Installation of polymer membranes
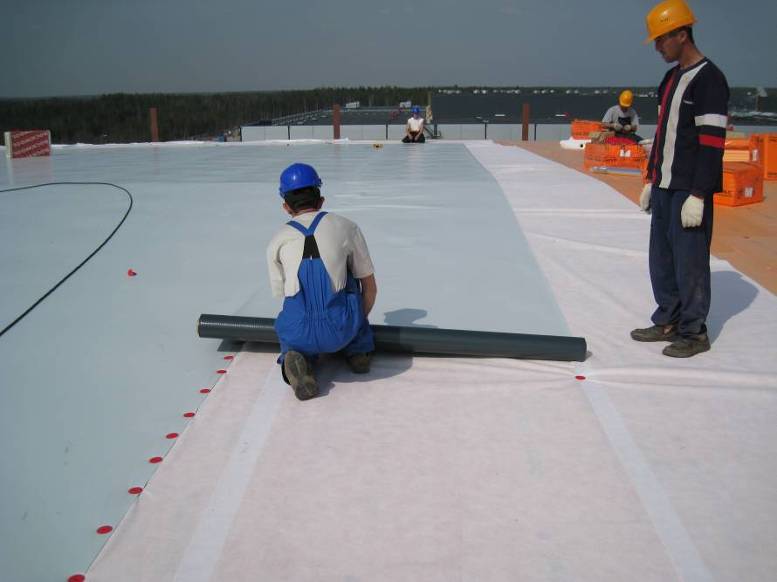
Generally, PVC and TPO coatings are more commonly used today.
To connect them, three methods are used, among them:
- Welding using hot air;
- Welding with a heating wedge;
- Diffusion welding using a solvent.
Diffusion welding is performed as follows. A special solvent is applied to dry and cleaned surfaces, then a load is placed on top.
Advice! The overlap of the membranes should be at least 5 cm, and the minimum width of a high-quality welded joint should be at least 3 cm.
Welding using hot air is carried out using a building hair dryer or welding machine. In this case, the first sheet of the membrane is reinforced mechanically, then the subsequent sheets are overlapped and welded.
Advice! To avoid wrinkling of the material, the membrane is rolled out along its entire length and strengthened in one of the corners.
PVC and TPO membranes are used where a reliable and prefabricated polymer roof is needed.In addition, it is these materials that are recommended for use in those buildings where the most stringent requirements for fire safety of the roof are imposed.
Polymer membranes are more expensive than modern polymer-bitumen materials by about a third.
But they also have a longer lifespan. Leading manufacturers give a guarantee on their materials for 10-20 years, and the predicted life of the roof (without repair) is about 50 years.
Polymer self-leveling roof
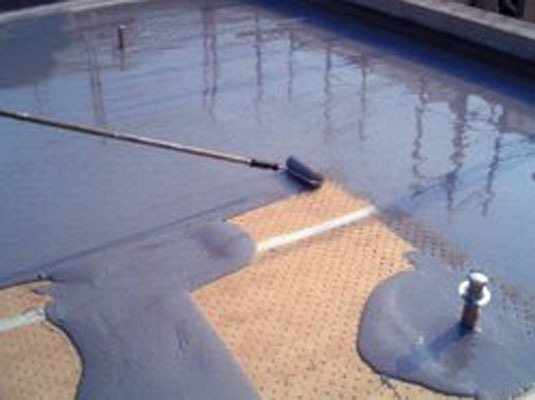
Another way that a polymer roof can be built is the pouring technology. Such a coating has no seams and consists of a waterproofing and reinforcing layer.
As a rule, fiberglass is chosen as a reinforcing layer, and polymer mastic is used as a waterproofing layer.
The main for the installation of a self-leveling roof can serve as concrete or wooden floor slabs, cement screed, metal, insulation boards. Also, such a roof can be mounted on an old roll coating or flat slate.
To improve the reflectivity of a self-leveling roof, the surface is sometimes painted with special roof paints.
This method of construction and repair of the roof is used both in industrial construction and in the construction of residential buildings and outbuildings. As a rule, a two- or one-component composition is used, which is applied to the base by pouring.
After completion of the polymerization process, roofing takes the form of a monolithic material that looks like rubber.
Advantages of self-leveling roofs:
- No seams;
- High level of strength;
- High elasticity;
- Easy installation;
- Resistance to various climatic conditions;
- Long service life;
- Vapor resistance.
A self-leveling polymer roof is, in fact, the same membrane, only it is prepared and applied directly on the roof.
There are two types of material used in this technology:
- Polymer-rubber coating;
- polymer coating.
The latter option is used more often today, as it has a large number of positive properties.
The technology of applying a self-leveling roof is quite simple. The composition is poured onto the prepared base and distributed evenly with a roller or spatula. The most important advantage of such a coating is one hundred percent tightness.
The polymer coating is very elastic, so it does not crack with temperature changes, while maintaining its solidity.
The composition of the self-leveling roof
As a rule, self-leveling roofing is not just a liquid polymer material, but a whole system of coatings.
It includes:
- Polymer composition;
- Primer to prepare the base for application;
- Filler that increases the durability and strength of the coating;
- The reinforcing part, which is most often used as fiberglass or non-woven material made of polyester fiber.
Today, a bulk polyurethane roof is used very often. The advantage of this material is that it is very easy to use even in the most difficult areas, for example, around pipes, antennas, duct outlets, etc.
The polyurethane composition allows you to get a solid coating that resembles rubber.
Such a roof perfectly withstands the effects of various aggressive environments, temperature extremes and has a long service life, especially if a polyester fabric was used as a reinforcing component. Due to its excellent performance, polyurethane self-leveling roofing is used quite widely.
The use of polyurea in the repair and construction of the roof
Another type of bulk polymeric materials that are used in the creation and repair of the roof is polyurea. This is a polymer of organic origin, which allows you to create monolithic waterproof coatings.
Choosing a coating such as polyurea for the roof, you can be sure of its high strength. In terms of wear resistance, this coating surpasses even ceramic tiles, which are used for flooring.
Thus, polyurea is a high-quality material for waterproofing works in construction.
The main advantages of using polyurea:
- fast polymerization. You can walk on the coating within an hour after application;
- Ability to work in conditions of high humidity and low (up to minus fifteen degrees) temperatures;
- High resistance of the obtained coating to solar radiation and high temperature;
- Excellent electrical insulation;
- Durability;
- Fire safety. The coating does not support combustion and belongs to self-extinguishing materials;
- Ecological purity.
conclusions
The use of modern polymeric materials allows in a short time to create roof coverings that are distinguished by excellent performance - reliability, strength, durability.
Did the article help you?