Today, one of the most modern types of roofing is membrane roofing: the arrangement technology used for the construction of membrane roofing makes it possible to obtain an almost monolithic roofing with excellent waterproofing characteristics. For the arrangement of this type of roof, special membrane materials are used, which are abundant on the market - so finding the right material is not difficult.
Membrane roofing materials
There are several types of roofing membranes. Each of them has its own distinctive features, its advantages and disadvantages.
Among the most popular varieties of roofing membranes are:
- PVC membranes are made from plasticized polyvinyl chloride reinforced with polyester mesh. To make membranes more flexible, volatile plasticizers are added to PVC. From PVC membranes, a sufficiently strong and reliable membrane roof is obtained - the installation of PVC roofing membranes is carried out by welding, and the joints between the canvases are not inferior in strength to integral sections. Among the disadvantages of roofing membranes of this type are the presence of volatile compounds released into the external environment, and the low resistance of the membrane sheet to oils, solvents and bitumen.
- EPDM membranes are made from synthetic rubber. Reinforcement of these membranes is also carried out using polyester threads. EPDM membranes are characterized by relatively low cost, long service life, and high elasticity. Among the disadvantages is the need to use glue to connect membrane sheets. As a result, the joints of the membranes become the most “problematic” place, and the repair of the membrane roof from EPDM membranes must be carried out more often, since it is at the joints that leaks occur.
- TPO membranes are made from thermoplastic olefins. TPO membranes are produced both unreinforced and reinforced with fiberglass or polyester. The connection of TPO-membranes to each other is carried out using hot air welding, which makes it possible to obtain a sufficiently strong seam.The only drawback of these membranes is their lower elasticity (compared to PVC and EPDM membranes).
The device of a membrane roof from these roofing materials can be carried out using different technologies. Below we will look at the most commonly used ones.
Ballast fastening of the membrane roof
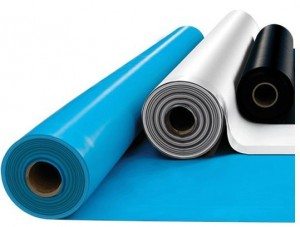
Roof pitch less than 15 the simplest is used - ballast fastening of roofing membranes:
- The membranes are laid on the roof, leveled and fixed (using glue or welding) along the perimeter. Also, fixing is carried out at the junction of membranes to vertical surfaces.
- We lay a layer of ballast on top of the expanded membrane. The best ballast is river pebbles of medium fraction (20-40 mm), rounded gravel and crushed stone.
- Ballast weight must be at least 50 kg/m2
- If unrounded gravel or broken stone is used for ballast, in order to avoid damage to the membrane fabric, we lay mats or non-woven fabric on top of it, the density of which exceeds 500 g/m2
Membrane mechanical fastening
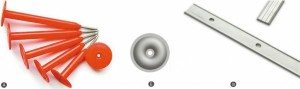
If the supporting structure of the roof is not designed for the loads that are necessary for the ballast fastening of the membranes, mechanical installation of the membrane roof is used.
Also, mechanical fastening is used when the roof structure does not allow gluing membrane waterproofing material.
The basis for mechanical fastening can be reinforced concrete, corrugated board, wood, etc. To fix the membranes along the edges and along the perimeter of the protruding elements of the roof, specialized edge rails are used with a sealing layer applied to the underside.
Fastening the membrane materials themselves on the very roof is made using telescopic fasteners, consisting of plastic umbrellas with a wide hat and metal anchors, or large-diameter disk holders.
Disc holders are recommended for use if the roof slope exceeds 10.
We install mechanical fasteners in the overlap zone of roofing membranes. The spacing of fasteners should not exceed 200 mm. If roof pitch angle exceeds 2-4, then an additional fastener line is installed in the valley zone.
Note! If the mechanical fastening of the roofing membrane is carried out directly to the base of the roof, a layer of geotextile material (non-woven fabric) is laid under the membrane in order to avoid damage to it.
Sticking roofing membranes
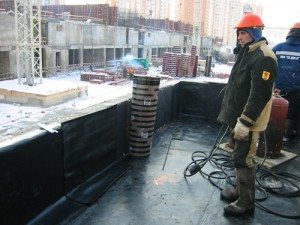
The gluing of roofing membranes is used relatively rarely, since this technology of membrane roofing is relatively uneconomical and does not provide the necessary strength for fixing the roofing material to the base.
And yet, in some cases, adhesive bonding is used - most often where other methods are not applicable. In this case, it is necessary to use adhesive mixtures whose tensile strength exceeds the mating strength of the underlying roof layers.
It is also recommended to glue the roofing membrane not over the entire area, but only along the perimeter of the roof, in the overlapping areas of the panels, and also - in the most problematic areas - on the ribs, in the valleys and at the places where the membrane adjoins vertical surfaces (buildings on the roof, chimneys, ventilation channels, etc.)
Heat-welded roof systems
Many roofing membranes are heat-welded. For this, a special welding machine is used, which produces a jet of air with a temperature of 400-600 C. Recommended width of welded layer for roofing membrane is 20mm to 100mm.
The connection of the panels of the roofing membrane by welding ensures the tightness of the system. In addition, the weld, unlike the adhesive, is not affected by ultraviolet radiation.
To date, heat-welded systems are the most modern and reliable, however, the complexity of their arrangement can become an obstacle if you decide to make such a roof with your own hands.
The membrane roofing technology described in this article is applicable for both large buildings and small outbuildings.
And if you carefully study all the properties of membrane roofing materials and the features of their application, then we are sure that you will get a reliable and durable membrane roof!
Did the article help you?