The modern universal coating includes corrugated board. It is used in private construction, at industrial facilities, for the construction of prefabricated structures. New equipment + corrugated board production makes it possible to obtain roofing and facade material. The topic of this article will not touch on the installation conditions of this practical material. We will touch upon points regarding the technology of its manufacture.
Production stages
The production of corrugated board is based on the methods of profiling smooth steel sheets (with galvanized and decorative coating) to obtain corrugated profiled sheets from them.
Profiled sheets have found their application as:
- material for walls in the construction of industrial, prefabricated buildings, pavilions;
- material for exterior and interior cladding of buildings;
- sheets for the manufacture of formwork;
- modern roofing material in industrial and residential buildings;
- profiled sheets for the construction of partitions, permanent or temporary fences.
Decking is manufactured and sold with a protective polymer coating and various wave heights.
The production of this material includes the following steps:
- development of a manufacturing project, taking into account the type, color, length and number of profiled sheets;
- production of a profile on rolling equipment;
- delivery of finished products to the consumer.
High-quality production of profiled sheets requires specialized equipment for the production of corrugated board.
Attention. Only technically high-quality equipment makes it possible to obtain a building material that meets standard requirements. Products manufactured on low-quality equipment have deviations in geometric shapes and sizes, which leads to a discrepancy between the quality of the material and its price.
Profile production
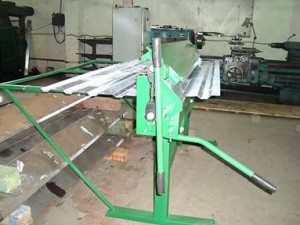
Equipment for the manufacture of corrugated board is used to create trapezoidal profiled sheets. Thus, corrugated board is a sheet bent profile with a trapezoidal corrugation.
Metal profile for roofing are made of durable steel by cold profiling.
Depending on the application and the needs of customers, the profiled sheet can be uncoated and with it.
The production of a coated material is necessary if it is used for outdoor work. The uncoated profile is used when constructing formwork for pouring concrete.
Each type of corrugated board has a different thickness. In the case of using high-quality raw materials, that is, first-class steel, a profile with a zinc coating of 20-26 microns is produced.
Reducing the coating thickness to 10-13 microns leads to an increase in wear.
Advice. Thus, the manufacture of corrugated board with your own hands should take place only with raw materials that have a grade 1 coating and equipment manufactured by well-known engineering companies.
Production requirements
The design of production for the production of profiled sheets must comply with the following requirements:
- the room under the equipment must have a concrete floor with a flat surface;
- production requires special equipment with a carrying capacity of more than 5 tons;
- the temperature in the production room should not fall below 4 degrees, and when working with pneumatic mechanisms - 10 degrees;
- the room must be equipped with gates for the convenience of unloading raw materials and loading finished corrugated board;
- it is necessary to provide places for storage of rolled steel.
When creating equipment for the production of corrugated board with your own hands, it is necessary to fulfill the requirements for its placement:
- Machines are placed in such a way that there is access to their nodes during maintenance or technical inspection.
- For convenience, unwinders should be installed near the storage of raw materials.
- If there is not enough space in the room, the warehouse of finished corrugated board can be organized in a separate building.
Attention. The fulfillment of all these requirements, plus the availability of high-quality equipment, makes it possible to produce profiled sheets with a length of 1-12 m. There is equipment with the ability to manufacture sheets with a length of 25 m.
Manufacturing process
Decking is a production that begins with a design sketch and mathematical calculations. Next comes the choice of coating color and thickness of the flooring.
Only after that, the manufacturing process is directly carried out using roll forming machines to obtain roofing, wall, floor profiled sheets.
The production technology of corrugated board includes the following steps:
- rolled steel is installed in the uncoiler of the rolling machine;
- through the rolling mill, the strip metal reaches the shears, where the control cut takes place;
- from the control panel, the parameters of the length of the sheets and their number are set;
- in automatic mode, the machine rolls sheets;
- cutting sheets to measure also occurs automatically, and the finished corrugated board reaches the receiving stacker;
- finished sheets are subject to labeling and packaging in polyethylene film.
Equipment for the production of
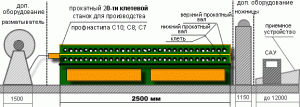
The equipment for corrugated board is divided into cold and hot method of sheet metal processing. More common are cold-processed rolling machines that do not require heating of the feedstock.
Such lines carry out rolling and cutting of metal.Manufacturing is called profiling, due to the fact that the metal takes the form of a profile.
Profiled sheets of various modifications are produced on different equipment. The scope of its use depends on the type and type of profile.
For each type of sheet, depending on the height of its corrugations, which characterizes the material, the equipment develops different pressure.
Production equipment varies according to the level of mechanization:
- automated;
- manual;
- mobile.
Mobile equipment for the production of arched corrugated board is used if it is necessary to manufacture sheets on a construction site. They are used for structures with arch elements - hangars, granaries, airfields.
Manual equipment is applied to the production of corrugated profiles for corrugated board small size and quantity. Technological operations on it are performed in manual mode.
Basically, manual equipment is used by construction organizations in metal processing workshops. It is necessary in the production of additional elements.
Automated machines are represented by an automatic or semi-automatic line of equipment. They include a set of mechanisms that are mounted in sequential order.
Both the arched corrugated boarding equipment and the automated one make it possible to produce profiled sheets at a fairly fast pace.
Attention. Manual machines are not recommended for rolling raw materials with paint or polymer coating.
Production line composition
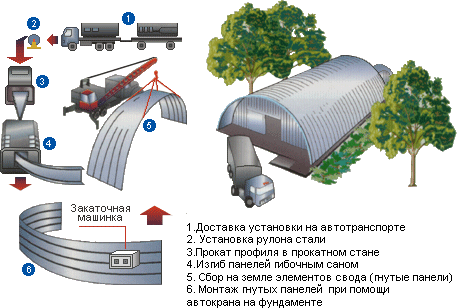
The standard production line has the following composition:
- console decoiler for steel coils;
- rolling mill for profile formation;
- guillotine shears;
- receiving device;
- automated control system.
The equipment looks like this:
- Galvanized, thin steel sheet is placed on the cantilever decoiler.
- The feedstock in the form of a strip enters the rolling mill, which contains a certain number of pairs of stands. The quality of the products obtained depends on the number of stands. Each pair contains rollers of a given geometry, which are mounted on the lower and upper shafts.
- The steel sheet, passing through the stands, acquires the intended geometry.
Production equipment can be equipped with a touch panel, electromechanical scissors, receiving roller tables, clamping devices and a table necessary for creating an edge, a waste collector.
The main piece of equipment is the rolling mill. It is with its help that the profiled sheeting of a given profile is made of smooth steel.
The demand for profiled sheets is growing every year. Therefore, according to experts, investing in the production of rolled steel is considered economically justified.
For the production of high-quality material, the development of a demanded resource, a production line of a high-class technical condition is required.
Did the article help you?