Profiled tin sheets are widely used in industrial and civil construction. However, they are not made by hand. How the line for the production of corrugated board is arranged, what they are and what are the differences - later in the article.
Before considering the equipment directly, in order to better understand how its characteristics are determined, you should decide what types of corrugated board are. After all, it is the parameters of the final product that determine the choice of equipment for its production.
Decking, even having the smallest corrugation value (8 mm for wall modifications), turns out to be much stronger than ordinary, galvanized sheet steel, from which it is made.
It is the longitudinal relief that provides its additional rigidity.Therefore, builders widely use it for a variety of purposes: fences and walls of industrial buildings, as a roofing material, for interfloor ceilings, and even as a fixed formwork.
Walls and roofing made of corrugated board do not weigh down buildings and have excellent tightness (Footnote 1).
Naturally, different tasks require different characteristics, and hence lines for the production of corrugated board.
All technological information about consumer qualities is contained in the marking of corrugated board itself, which is important to familiarize yourself with before how to choose a corrugated roof.
There is a state standard for its production - GOST 24045-94, where all the characteristics reflected in the brand are registered.
For example, C44-1000-0.4 means:
- C - purpose of the material
- 44 - corrugation height
- 1000 - useful, or mounting width of the sheet
- 0.4 - the thickness of the metal used
Classification of corrugated boards (Footnote 2):
- WITH - wall decking used for the construction of fences, walls and partitions
- H - roofing corrugated board is used for roofing
- HC - used as a roof covering and as a corrugated board for walls
Important information! For the production of all standard corrugated sheets, 1250 mm wide sheet is used. Different widths of the final product (as a rule, from 750 to 1150 mm) are determined by the departure of the material to the height of the corrugation: the higher the profile, the smaller the width. However, at the same time, strength also increases proportionally.
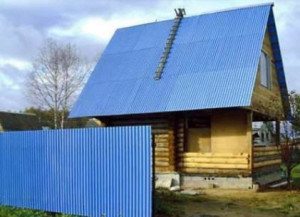
The length of the sheets, in accordance with GOST, can be from 2.4 for wall and 3 m for mixed and roofing materials, up to 12 m for all types.
However, due to the fact that the material is rolled, under the order, manufacturers are ready to cut their products to any size convenient for the customer.
Roofing materials also, in most cases, have a special capillary drainage groove at the top of the corrugation on the outside.
As a raw material for the production of corrugated board, only galvanized rolled metal is used. It can have a thickness of 0.35 to 2 mm. The standard outer diameter of the roll is 1.2 m, while the length of the sheet in it depends on the thickness of the metal.
The steel can have either a conventional zinc coating or an additional layer of protection from a paintwork material or a polymer.
In this case, the coating can be applied on one or both sides, in case of double-sided application, it can be performed with one or different materials.
Important information! The most reliable and durable is corrugated board coated with synthetic polyester materials. But it is also the most expensive and most vulnerable to mechanical damage to the protection. However, the last drawback is mitigated by the presence on the market of special repair compounds.
The typical scheme of the line for the production of corrugated board includes, as a rule, five main devices:
- Uncoiler - a roll of sheet steel is put on its shaft and held to be fed to the processing site
- The forming mill is the main element of the line, where the actual profiling of the supplied material tape takes place.
- Control unit - here you can turn on, turn off and program parameters for working devices
- Guillotine shears - with their help, the finished profile is cut into sheets
- Receiving table - as a rule, corresponds to the dimensions of the sheet being produced at the moment (the width of the table is fixed, and the length can be adjusted). Here, finished products are stacked and packaged for subsequent shipment to the warehouse.
Important information! Some reputable equipment manufacturers that produce various lines for production: the production of corrugated board, metal tiles, other types of rolled products, equip their products with additional devices. For example, it can be a feeding table located between the unwinder and the forming machine, or cut-off shears, which contribute to a quick change of the roll. Naturally, such additions have a positive effect on the technological process, and hence on the quality of the finished sheet.
However, the main element of any line is the rolling mill. It consists of symmetrical pairs of shafts (stands) installed on the frame, which, due to mechanical compression, form a corrugation on the sheet, rolling the tape through itself.
The more their number, the deeper the profile is obtained. After all, the tape cannot simply be taken and at the entrance to the mill set it to the desired bend (the width of the raw material is greater than that of the finished product).
In this case, the metal, at a minimum, will lose its plasticity on bends, and, most likely, it will break. In addition, it will be very difficult to stretch it through the form in this case.
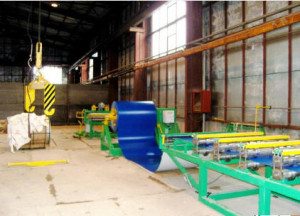
During the passage, the original material is deformed from a smaller bend to a larger one. Accordingly, the diameter of the forming cylinders grows from pair to pair, and the distance between them decreases, up to the last stand, where the corrugated board acquires a planned size.
In connection with the described features of the technology, it is practically impossible to produce products of different profiles on the same mill.
Each type requires its own width of the bed at the place of installation of the stands, as well as the corresponding diameter of the cylinders. However, there are models that allow the production of material with the same corrugation height, but with different sheet widths.
Theoretically, it is also possible to produce another, having not too big differences in the height of the corrugation, rolled products. However, in this case, you will need a complete set of equipment, including stands and guillotine shears.
Taking into account the costs of installation work, such a solution from a financial point of view will not differ much from the installation of a new line. What any manufacturer can vary is the thickness of the metal, the type of its coating, and the length of the finished corrugated board.
An electric power plant is installed on the frame as a drive, the power of which determines the maximum thickness of the processed metal and the rolling speed.
However, the mill not only performs the main work itself, but is also a supporting structure for some of the rest of the equipment - at least the control unit and the guillotine, which also plays an important role.
Shears of a guillotine incorporate any line of production of a professional flooring. They repeat the geometry of the outgoing profile and have a hydraulic, electromechanical, less often pneumatic drive.
The quality of products largely depends on them, since the edge of the corrugated board should not have burrs, and the bend formed at the cut point should not affect the length of the sheet by more than 0.5 mm (according to GOST).
Since the cutting edges of scissors are the main working element that affects these indicators, they periodically require sharpening or replacement.
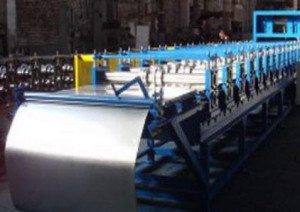
To control the entire set of mechanisms, a control unit is used. At the beginning of the production process, it is programmed for a certain thickness of the source material, the type of coating, and the required sheet length is also set here.
These devices have electronics to shut down the line in the event of a problem.
Equipped with such a controller, the corrugated board production line is considered semi-automatic. This is due to the fact that filling a new metal tape when the old roll is over is done manually.
The rest of the time, the staff (who is represented by one worker on most lines) remains to observe the absence of malfunctions - the equipment will do everything itself.
And now you only need to familiarize yourself with sheet roof installation instructionsand your home will be transformed!
Information sources
- Article from
- The largest manufacturer of roofing materials
Did the article help you?