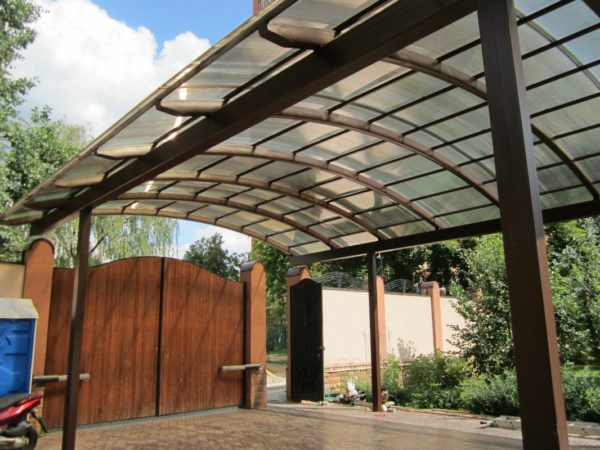
Canopies made of cellular polycarbonate were liked by many buyers, and now they are found more and more often, especially in summer cottages and cottage towns. As part of the article, we will talk about the advantages and features of this material, as well as consider how to install the most popular designs.
Sheds with polycarbonate roofing
What is polycarbonate
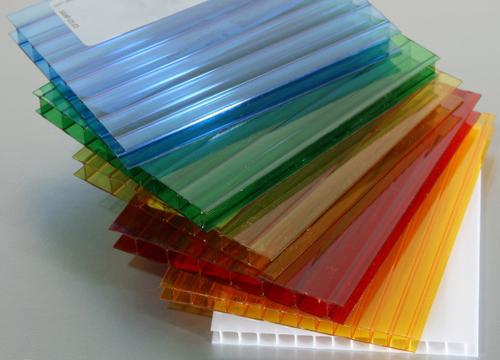
Polycarbonate is a modern type of plastic. The material belongs to thermoplastics, or rather, to compounds obtained from polyesters of carbonic acid and dihydric alcohols.
The material does not occur in nature, but is produced by synthesis at chemical enterprises. It is a heat-resistant transparent substance, insoluble in water and strong enough. It is used in various industries:
- construction,
- bird,
- medical technology,
- instrument making,
- electronics,
- food industry,
- automotive industry and many other areas.
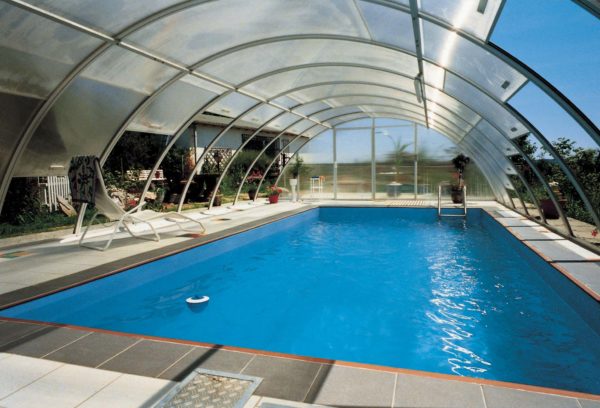
For the needs of construction, polycarbonate is produced in the form of sheets that can be used as building envelopes and roofing materials. They are also used. Sheets are of two types: from monolithic or cellular plastic.
Monolithic or cast polycarbonate is characterized by very high strength and transparency. This is the most durable transparent material of all known in the world construction market, produced on an industrial scale. Of course, the price of a cast sheet is significantly higher (about 5 times) than the cost of a cellular one.
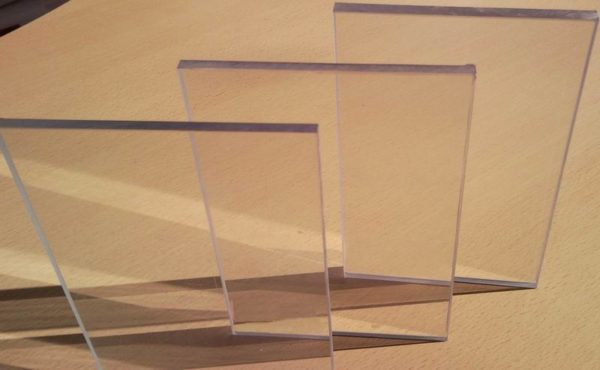
However, for our needs, super strength is not important, but the cost of a polycarbonate canopy is significant for us, so we will consider the characteristics of the honeycomb structure:
- Material is flexible, which is very important for the builder, because it becomes possible to create curved arched surfaces with it;
- High strength it is also preserved with a honeycomb structure, which allows you to mount sheets even on a rare crate or on rafters without a crate;
- High chemical resistance allows the material to successfully deal with the effects of substances dissolved in sediments, as well as inertness allows the use of household chemicals for the care and washing of sheets;
- Light transmittance reaches 76 - 83% depending on the thickness of the sheet;
- Like many other types of plastic, it is not afraid of moisture and biological corrosion.;
- Does not deteriorate under the influence of solar radiation, delays ultraviolet radiation;
- Sheets are light enough, even monolithic polycarbonate is two times lighter than glass;
- Easy to process: can be cut with a knife, jigsaw, can be drilled, milled, bent.
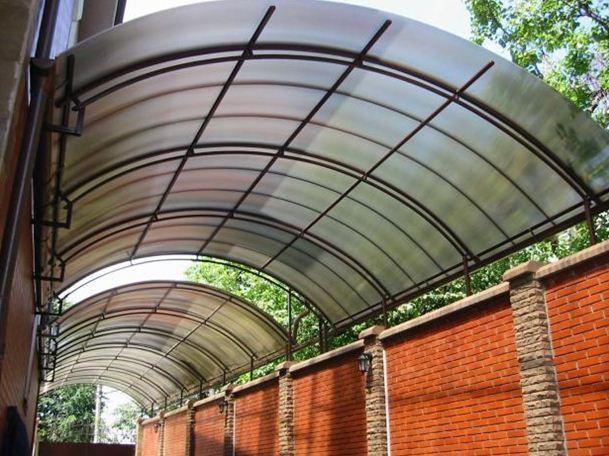
Important! As you can see, cellular sheets are quite suitable for us, and given their low weight and how much a canopy made of polycarbonate with a honeycomb structure costs, we can say that it is cellular sheets that we need.
Varieties of designs
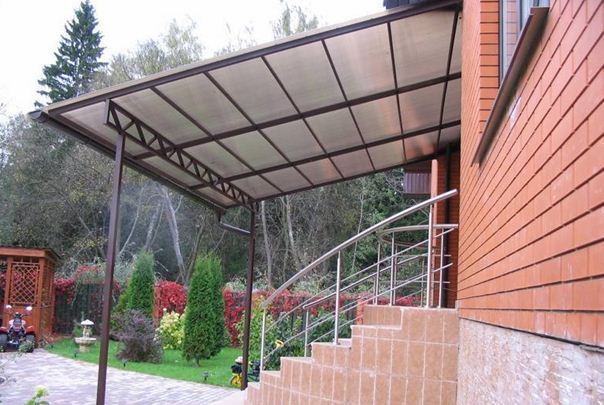
Types of polycarbonate canopies are very different:
- small peaks and huge pavilions;
- simple flat slopes;
- arched;
- domed;
- tent and arbitrary forms;
- wall-mounted and standing on separate supports;
- wooden;
- stone;
- metal.
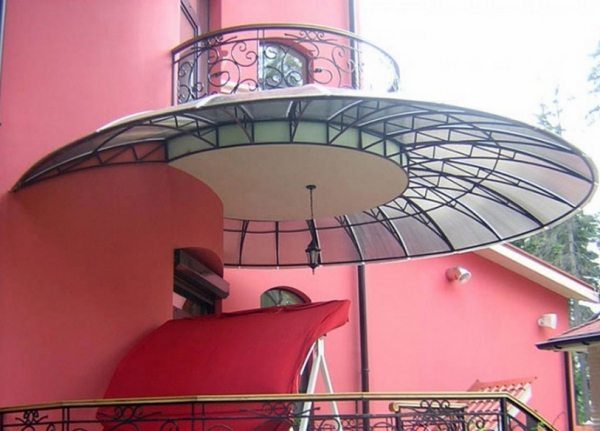
Due to the flexibility of the material, the arched canopy made of polycarbonate has gained particular popularity. Its main structural difference is the bent rafter legs, which create a curved surface.
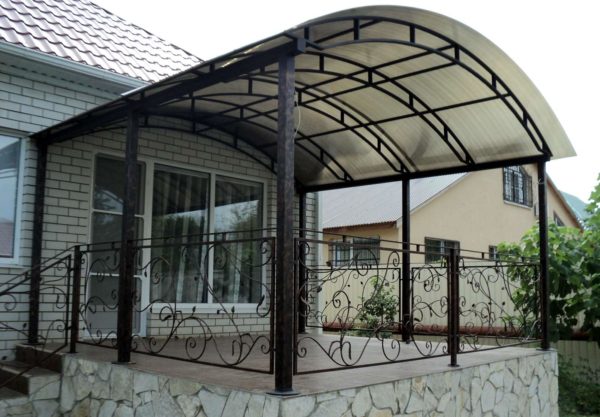
Important! Since it is difficult to bend wooden or steel parts equally at home, polycarbonate canopy arches are produced at industrial enterprises or in specialized workshops.
In the modern Russian construction market, ready-made kits are most often found, which only need to be assembled and installed according to the instructions. These sets usually include:
- details of the steel frame;
- fasteners;
- roofing sheets
- as well as various additional elements for ends, joints and self-tapping screws.
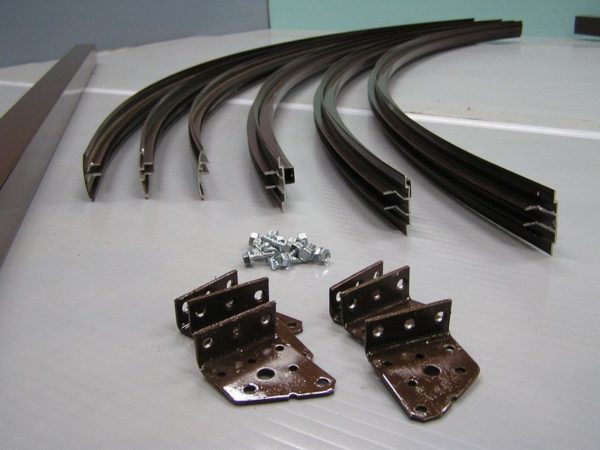
Of course, you can make such a frame with your own hands, and bend the elements of arched rafters on a pipe bender, which can be found in any workshop for artistic forging and manufacturing metal structures. However, for this you will have to work a lot with the project, learn how to handle electric arc welding and a grinder, and also pay attention to the features of steel anti-corrosion treatment.
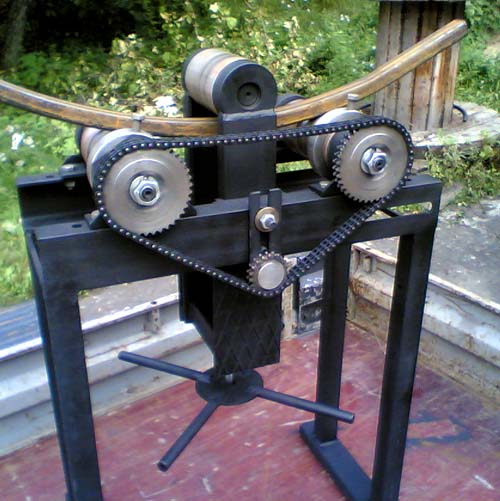
Important! If you want to mount the canopy yourself, then it is better to choose a wooden structure or buy a set of parts in a store, and only deal with the installation and assembly of the structure on the site.
Installation
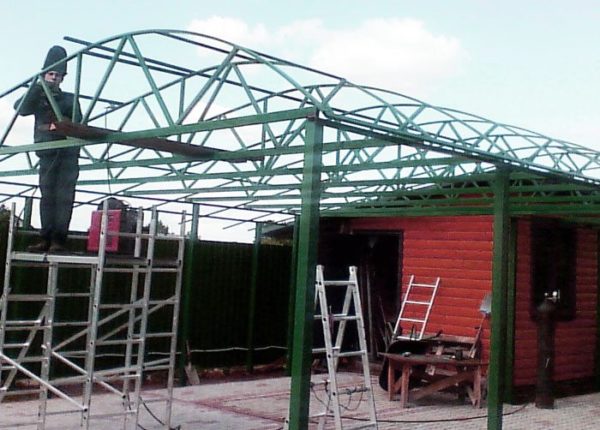
Kits for making canopies can vary greatly in design, methods of attaching parts, etc. However, the general order of work does not change from this, and therefore our instructions show the main assembly steps inherent in most models:
- According to the drawing of the finished structure, given in the technical data sheet for the product, we mark the territory and determine the installation locations for the support pillars. In these places we dig holes with a depth of 60 - 70 cm with a diameter of at least 30 cm;
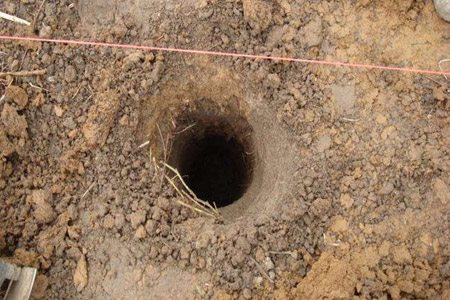
- We install pillars in the pits, set them strictly vertically with a plumb line, fix them with temporary stops and fill them with concrete 1: 3: 5 (cement / sand / gravel);
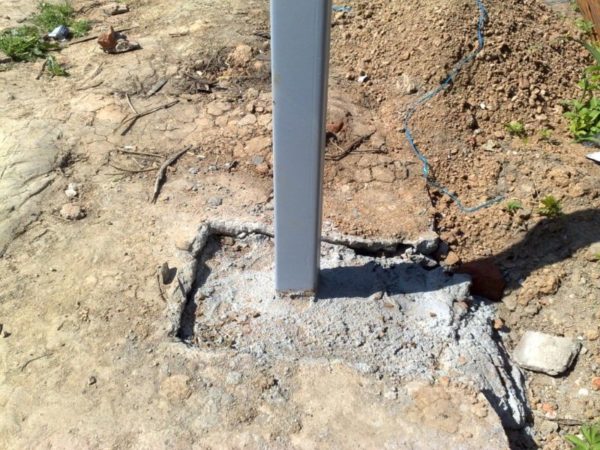
- Depending on the set, we may meet ready-made trusses or in the form of parts. In the second case, the farm will have to cook on its own. In any case - we collect trusses or rafters, if necessary - we adjust to the size;
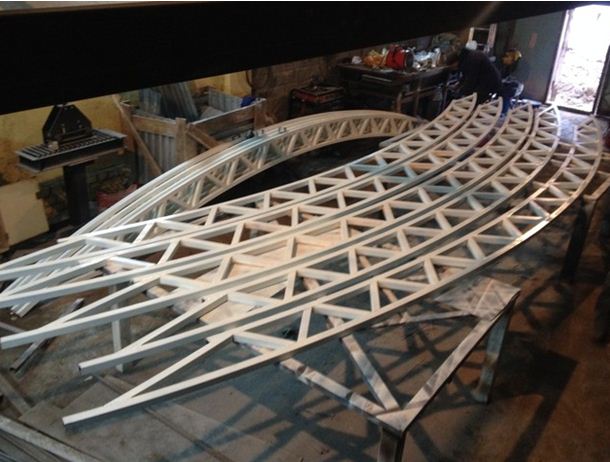
- In the meantime, our concrete has hardened and gained preliminary strength, and we begin to mount the top trim. To do this, we find the appropriate parts and weld them along the upper perimeter of the pillars, connecting them into an integral structure;
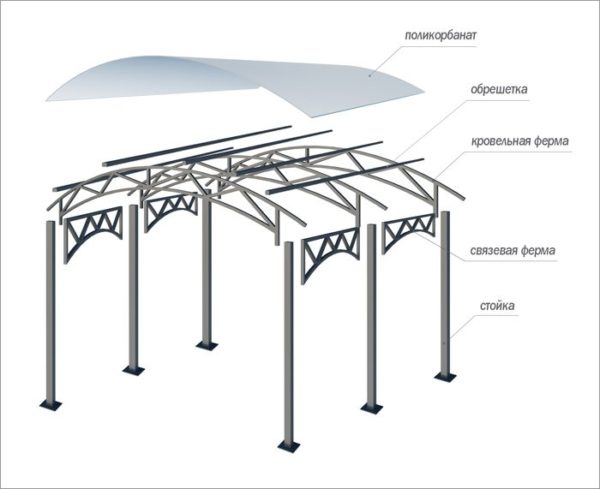
- According to the manufacturer's instructions, we mount arches or trusses on the top trim of the pillars. Here, both welding and bolted connection of elements is possible. Rivets are sometimes used;
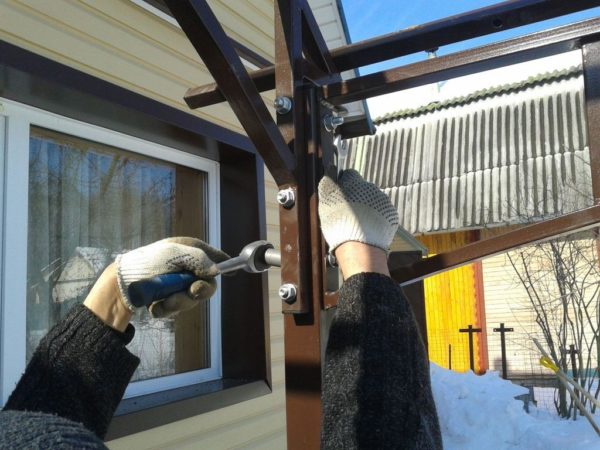
- We cut polycarbonate sheets in accordance with the size and pitch of the rafters. Next, we insert them into the mounting grooves and close them with an aluminum cover at the joints, close the ends with special plugs.
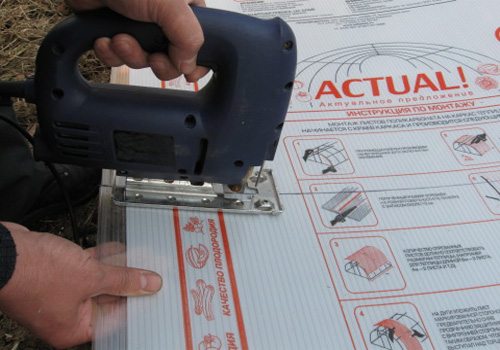
Important! The direction of the channels of cellular polycarbonate must match the direction of the bend of the arch, otherwise you will damage the material.
Conclusion
Canopies made of polycarbonate are beautiful, reliable and easy to install. The video in this article complements the instructions, makes it clearer and more understandable.
Did the article help you?