In addition to traditional roofing materials, materials that transmit light, such as glass and various polymeric materials, are gaining more and more popularity in recent years. This article will talk about what a do-it-yourself polycarbonate roof is, what types of polycarbonate roofs are and what materials are used in their construction.
The main thing that distinguishes such a roof from other types of roofing is that polycarbonate allows you to use sunlight as a source of interior lighting.
In this regard, a number of requirements are imposed on polycarbonate roofs:
- The illumination indicators of the premises must comply with accepted standards;
- The working areas of the premises must be protected from the brightness of direct and reflected sunlight, because for do-it-yourself garage roofs this is highly relevant;
- Polycarbonate roofs must provide full ventilation of the room; in case of fire, smoke must also be removed;
- The roof should not create obstacles for the removal of snow;
- The roof structure must have static strength, for example, like a hip roof;
- A polycarbonate roof must be equipped with steam, sound, hydro and thermal insulation.
Polycarbonate roofs can be built as individual elements such as arches, slopes, domes, pyramids, polygons, etc. At the same time, indoor premises can be both warm and cold, depending on their purpose.
Types of polycarbonate roof structures
There are the following types of structures of light-transmitting roofs:
- Designs based on system profiles;
- Structures made of self-supporting elements that transmit light;
- Skylights and skylights.
The use of system profiles allows you to install any type of polycarbonate roof: one- or two-slope, domed, tent, etc.
Profile manufacturers most often offer ready-made solutions suitable for popular types of roofs, there is also a service for individual development of projects for more complex structures.
For the manufacture of system profiles, materials are used:
- for large spans - steel;
- for small and medium - aluminum.
Useful: the profile can be used with a light-transmitting element, regardless of its type, it is only important to provide a gap between the element and the profile with a sealant, such as synthetic rubber.
For the manufacture of structures based on self-supporting elements that transmit light, only transparent polymeric materials are used, such structures have stiffeners and are usually produced in the form of various segments and arches.
Transparent polycarbonate roof
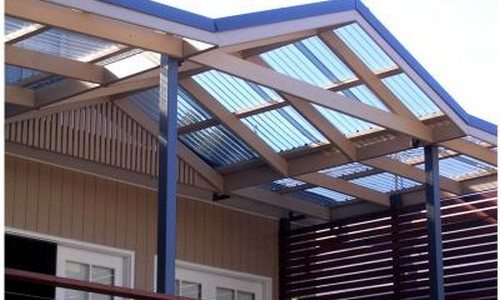
Roof polycarbonate is a polymer, which, according to its parameters, belongs to engineering plastic materials.
This material is able to maintain its physical and mechanical properties at temperatures from -40 to +120 degrees, two types of polycarbonate are currently used in construction: structured and monolithic panels and sheets:
- Transparent monolithic polycarbonate is used as a roofing material and is excellent for the construction of both flat structures and curved roofs, the transparency of which approaches glass. At the same time, this material is not widely used due to the rather high cost, significantly exceeding the price of structured polycarbonate products.
- Structured panels and sheets, often also referred to as cellular or honeycomb, are the most widely used type of polycarbonate in construction, most often used in arched and horizontal ceilings. The weight of this material is 6-10 times less than the weight of standard silicate glass and 6 times less than the weight of acrylic glass.The increased flexibility of the material allows it to be used when covering complex geometric roof structures, such as various types of domes, extended skylights, individual sections of large domes, etc.
A cellular polycarbonate roof is the preferred option for self-construction due to the following advantages of this material:
- Low specific gravity of 0.7 to 4.8 kg/m2, which allows you to create light and at the same time original design solutions;
- Relatively low cost of coverage;
- Good thermal insulation performance;
- High flexibility of the material;
- Resistance to chemical influences;
- Burning resistance;
- High impact strength, which reduces the negative impact of hail and other falling objects;
- Quite a long service life, manufacturers usually give a guarantee for 10-12 years.
Most experts agree that a honeycomb polycarbonate roof is the most successful choice of glass replacement in the manufacture of a light-transmitting roof.
Production of a polycarbonate roof
When talking about how to make a polycarbonate roof, first of all, it is worth mentioning safety precautions, for example, the use of glasses and gloves when working with a grinder.
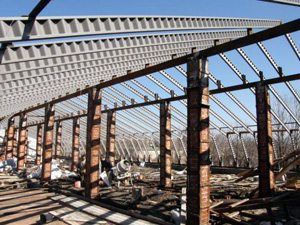
Before you cover the roof with polycarbonate, you should develop its design and either find a ready-made scheme, or develop your own drawings, according to which the roof will be installed.
The procedure for building a polycarbonate roof is quite simple and fast, which is facilitated by the rather significant dimensions and low weight of the material, as well as the fact that the construction of such a roof does not require the use of special tools.
When building a polycarbonate roof, special attention should be paid to the protective coating layer of the material, any damage to which will shorten the life of the roofing.
The first step is to make a supporting roof structure, and the roof slope should be at least 50 °, the slope of 100 ° is considered the most optimal.
The preparation of the roof structure includes the following steps:
- Rafters, the cross section of which is 60x40 or 60x80 mm, are fastened in such a way that the distance between the edges of the roof is 1.04 m, and between the two central axes of the rafters - 1.01 m.
- On the rafters, end and connecting profiles are fastened.
- Limiters are fastened with rivets at a distance of two centimeters from the edges of the profiles.
- The side surfaces of the plates are pasted over with standard adhesive tape to protect against reflected sunlight.
- The upper side of the plate is pasted over with ordinary adhesive tape and the lower one is perforated to prevent the penetration of dust or small insects into the internal cells of the plate.
After the installation of the supporting structure is completed, the installation of the plates proceeds. The connection of cellular polycarbonate sheets is waterproof, so there is no need to treat the seams with mastic.
Next, the plates are laid on the roof surface, positioning them so that the surface with the inscription is facing upwards, while leaving a gap of 5 millimeters between the plates to make an expansion joint.
A cover is attached to each profile, after which the profile plugs are fastened, and the installation is completed.
Next, the roof should be waterproofed with a seam that connects the wall and the top of the cover, as well as silicone mastic and drainage.
To ensure the longest possible and high-quality service life of polycarbonate panels, they should be carefully maintained, the main condition of which is the constant maintenance of cleanliness of the panels.
During operation, dirt and dust accumulate on polycarbonate panels, which can be cleaned with a sponge moistened with soapy water or a soft cloth. In no case should the panels be cleaned with sharp objects, as well as caustic or abrasive preparations.
Did the article help you?