It is difficult to argue with the fact that a roof covered with metal tiles involuntarily attracts the eye with its beauty and conciseness of forms. With such a roof, the house looks neat and at the same time solid.
Now most owners are sure that only professionals can mount such beauty, I confess, I also thought so, but on closer examination everything turned out to be not so scary and in this article I will tell you how to properly cover the roof with metal tiles myself, without resorting to the services of expensive masters. And to make it easier for you to understand, I broke my story into 10 conditional steps.
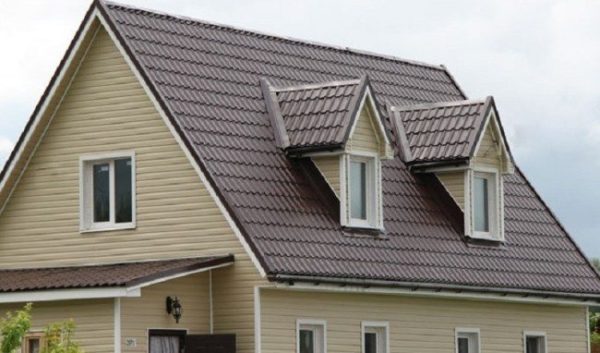
- Thorough preparation is the key to the success of any enterprise.
- Briefly about the choice of material
- Material calculation
- Tool
- Roof installation in 10 steps
- Step number 1: installation of waterproofing
- Step number 2: installation of the crate
- Step number 3: arranging the valley
- Step number 4: how to go around the chimney
- Step number 5: installing fixtures for the drain and installing the cornice strip
- Step number 6: installation of sheets of metal
- Step 7: Installing the ridge and end rails
- Step #8:. installation of ventilation and antenna outlets on the roof
- Step number 9: we mount the snow retainer and walkways on the roof
- Step number 10: arrangement of insulation
- Conclusion
Thorough preparation is the key to the success of any enterprise.
It is no secret that the price of such a roof is far from childish, on average, the cost of 1 m² of coverage starts from 1000 rubles, of which almost half goes to pay for the work of the craftsmen. Here you involuntarily think, is the instruction so complicated to pay so much?
The installation technologies for slate and metal tiles are somewhat similar. But the installation of newfangled tiles has a lot of small nuances, each of which needs to be paid attention.
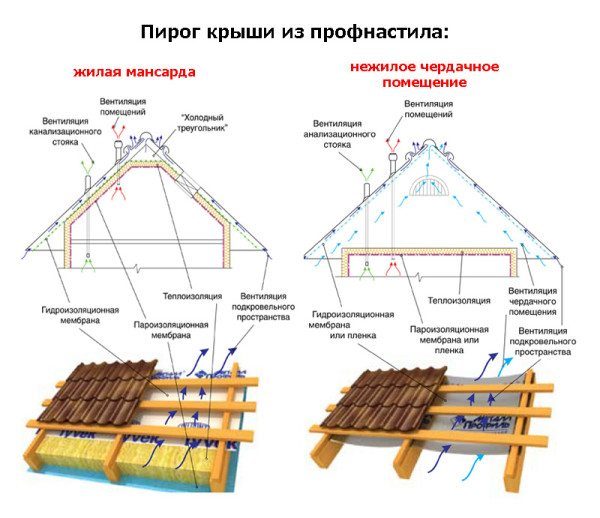
Before you cover the roof with a metal tile with your own hands, you must first choose this very tile. Then calculate how much material you need to buy. And be sure to prepare the tool, because one hacksaw and a hammer will not do here.
Briefly about the choice of material
If the "grandfather" slate is almost the same everywhere, then the tile differs in configuration and, more importantly, in the quality of the polymer coating. The durability of your roof and of course its cost depends on it.
The vast majority of manufacturers of this product take as a basis galvanized cold-rolled steel sheet with a thickness of 0.45 - 0.50 mm.In fact, this is the same profiled sheet, only bent differently and with a wider range of finishing protective coatings.
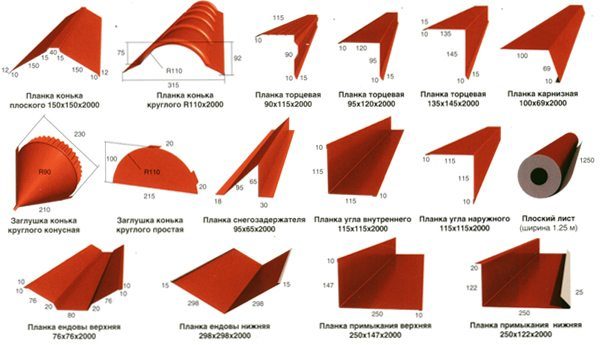
The most common types of polymer coatings for metal tiles | |
Coating type | General characteristics of the coating |
Polyester with glossy finish | In some sources, this glossy coating is also called polyester. Polyester has the most reasonable cost, holds ultraviolet well, but its thickness is only 25 - 30 microns. Therefore, the mechanical strength of the coating leaves much to be desired. Polyester can damage even a thick layer of snow, not to mention a fallen branch. |
Matte polyester | Here, the layer thickness already starts from 35 microns, respectively, and the strength of matte polyester is an order of magnitude higher. The only drawback is that the color range of the material is rather poor. |
Pural | Durable and quite beautiful material with a thickness of 50 microns. The main component of the coating is polyurethane with the addition of polyamide, which provides a unique resistance to sudden changes in temperature. |
Plastisol | Plastisol is deservedly considered a classic of the genre. The coating thickness reaches 200 microns. The basis of plastisol is polyvinyl chloride, on the one hand, PVC provides high mechanical strength, and on the other hand, plastisol can change color, in other words, fade from sunlight. Plus, due to the presence of polyvinyl chloride in some countries, plastisol was banned, although these bans did not affect us. |
Polydifluorite | The latest in fashion, a modern coating with a wide range of colors and unique characteristics of resistance to everything that can threaten your roof.The coating consists of 80% polyvinyl fluoride and 20% acrylic resins. Everything about this product is good, but the price is astronomical. |
There are many configuration options now, and each manufacturer praises its own version. How much I compared, the strength of the sheet depends on the depth of the wave, often it ranges from 22 to 78 mm.
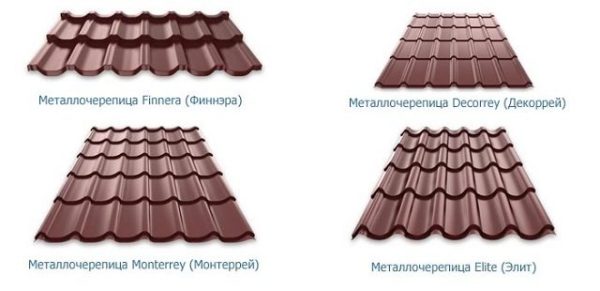
It is believed that the deeper the wave, the more stable the roof will be. But on the other hand, if the wave is too high, the depressions experience a greater load and the protective layer wears out more quickly there. As a result, I came to the conclusion that the optimal wave depth should be approximately 40 - 50 mm.
The width of the sheet is limited by the capabilities of the equipment, that is, the dimensions of the drums with prints on the conveyor, usually it fluctuates around 1m and often these parameters cannot be influenced.
But the length can reach 8m. If earlier it was for the most part strictly fixed dimensions, now more advanced manufacturers are introducing the service of making sheets to order according to your length, and in some cases they can even make a material pattern according to the shape of your roof.
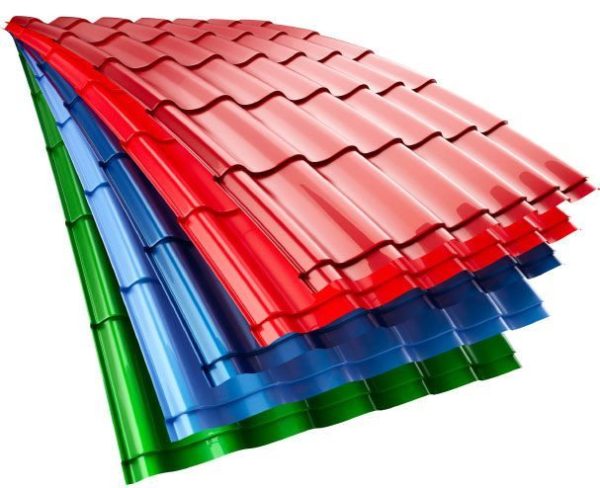
If you decide to cover the roof with a metal tile with your own hands, then it is better not to take on complex multi-level structures, especially those that have semicircular arches and various broken transitions. The maximum that an amateur without experience is capable of is a standard gable roof with an attic window, although nothing is impossible for a creative person with hands and a head.
Material calculation
Of course, each roof has individual dimensions, so for example I will take the average calculation of a simple gable roof with the size of each slope 8m wide (distance along the edge of the slope) and 4.5m long (distance from the slope cut to the ridge):
- We measure the length along the rafters, that is, from the ridge to the edge of the rafter leg, after which we add 50 - 70 mm to this value (different models of tiles come with different overhangs, so read the accompanying documentation);
- To find out the number of rows, you need to divide the width of the slope by the useful width of the sheet, the width of the slope is measured along the ridge. There is a useful sheet width and a total sheet width, these data are also indicated in the documents.
If we have a ridge length of 8 m, and a useful sheet width, for example, 1.1 m, then in the end we get 7.27 rows (8: 1.1 = 7.27). Logically, you need to round up, respectively, you will have to lay 8 rows; - Of course, it is better to order a single sheet along the length of the slope, because the fewer joints, the stronger the roof, and it is easier to fix it. But the transportation of long sheets is much more expensive, so 2.95m is considered the most popular size.
According to the condition of our task, the length of the rafter leg is 4.5 m, we add a sheet departure of 0.07 m to it, plus an overlap at the junction of sheets of 0.15 m, and we get 4.72 m (4.5 + 0.07 + 0.15 = 4.72 ). It turns out that one sheet on the slope will be solid (2.95m), and the second will have to be cut; - Based on these calculations, we have 16 sheets for each slope (8x2 = 16). And since our roof is gable, all you need is 32 sheets of metal tiles with a useful width of 1.1 m and a length of 2.95 m.
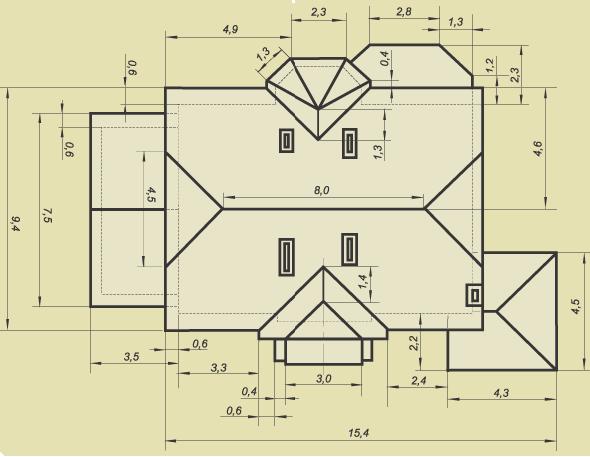
If the roof has asymmetrical slopes or there are more than 2 of these slopes, then calculations must be performed separately for each slope and then everything should be added up.
Tool
Below I will give a recommended list of tools that are used for professional installation of metal roofing:
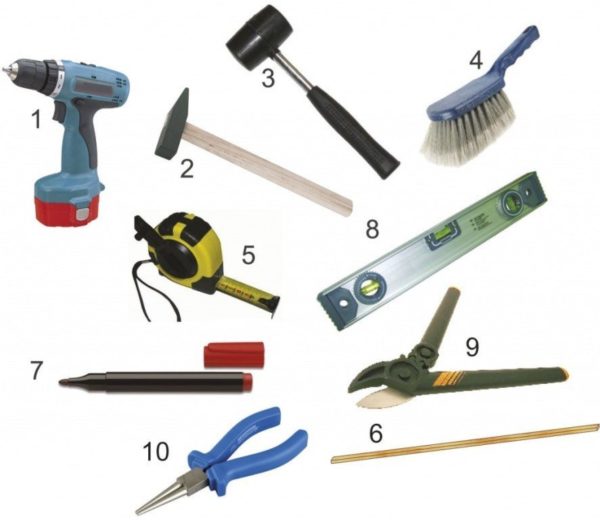
- Cutting electric shears;
- Nozzle on a drill for cutting metal;
- Manual cutting shears for metal;
- Standard lever shears for metal, can be right, left and straight;
- For the installation of fittings, you will need pliers "corrugation";
- Construction gun for sealant;
- Device for smooth bending of metal strips "Strip bender";
- If mounting on rivets is planned, then riveting pliers are needed;
- Construction stapler;
- Mounting knife;
- Adjustable template for mounting the supporting crate;
- Roulette;
- Cord for beating the level;
- Screwdriver with nozzles for different types of self-tapping screws;
- If insulation is planned, then you will also need a knife for cutting thermal insulation.
The use of a grinder for cutting sheets is strictly prohibited. It not only gives a ragged cut, but also “scorches” the edges of the polymer coating. As a result, in places of cuts, the metal begins to rust very soon.
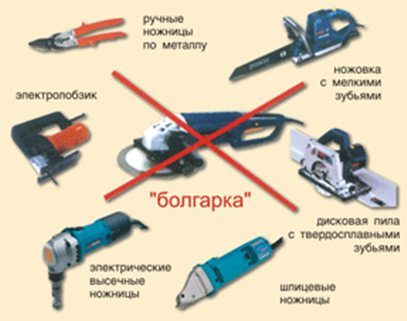
Roof installation in 10 steps
In general, there are 2 types of roofing, insulated and cold. They differ only in the presence or absence of insulation.. And since it is a little more difficult to mount an insulated roof, we will consider this particular option.
Step number 1: installation of waterproofing
- Waterproofing begins to be mounted from the so-called valleys, if any (“valleys” are the internal connection of two adjacent roof slopes). A roll of waterproofing is rolled from top to bottom to its full length valleys, naturally with an overlap on both adjacent roof slopes;
- After that, the tape of the waterproofing membrane is rolled out horizontally over the entire roof. You need to move from the edge of the roof to the ridge, again with an overlap;
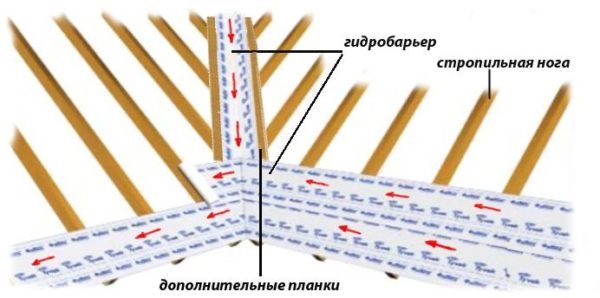
- Between the rafters, the waterproofing should slightly sag 10 - 20 mm, no more. And the overlaps between the tapes of the waterproofing membrane are glued with a special adhesive tape;
- From above, to the rafters, the canvas is fixed with a wooden bar 50x50 mm. I do not recommend taking thinner planks, because you cover the roof for more than one day and the thicker the planks of the crate, the more reliable your construction will be. But keep in mind, 50 mm is the maximum, the slats should not be wider than the rafters themselves;
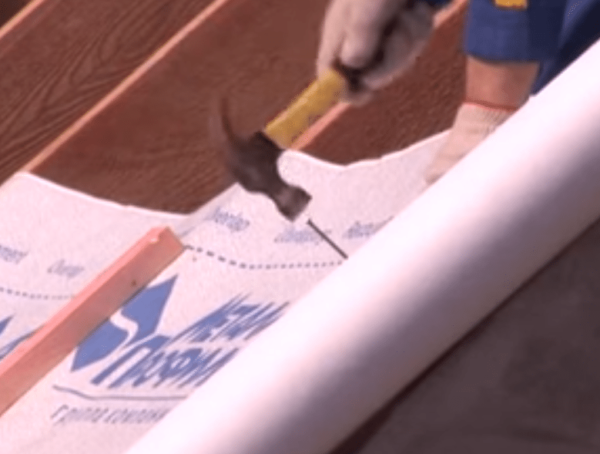
Step number 2: installation of the crate
Do not forget that all wooden structural elements must be treated with a complex protective compound. It makes no sense to make such compositions on your own now, because the price of factory impregnations is quite acceptable, and their quality, compared to homemade products, is disproportionately higher.
- Installation of the lathing under the roof begins with nailing two identical bars 50x100 mm horizontally along the edge of the rafters. The bars are stacked on top of each other. Note that the edge of the roof is formed precisely from 2 bars, if you take 1 bar 100x100 mm, then there is a possibility that it will be led by changes in humidity and temperature;
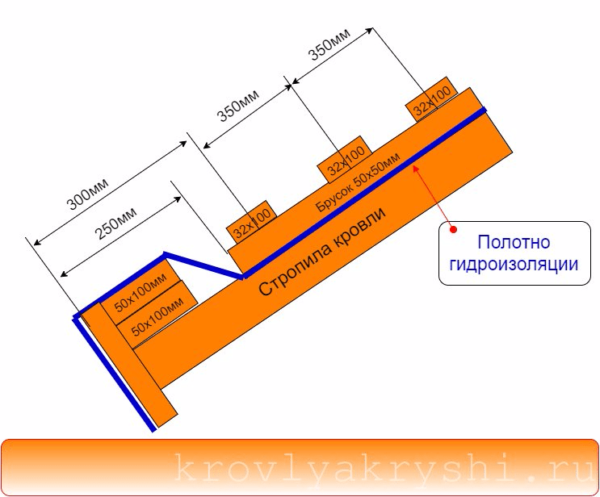
- Further, the waterproofing will need to be brought out over the boards, in other words, wrap the downed bars with a waterproofing sheet, as shown in the diagram. While the canvas does not need to be fixed, we will fix it later;
- On top of the 50x50 mm bar stuffed by us, a crate from a 32x100 mm board is horizontally stuffed, the crate pitch is selected according to the wavelength on the metal tile model you have chosen;
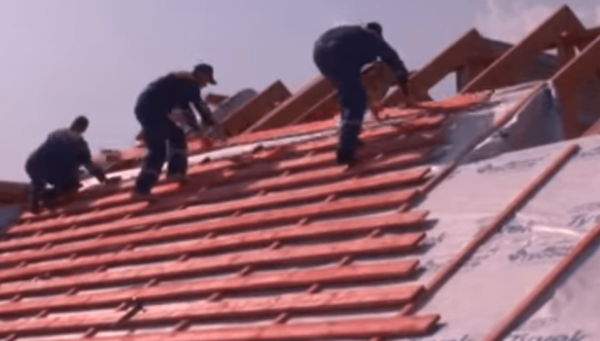
- Here it is very important to accurately maintain the crate step, so each plank is stuffed according to the template. Professionals use an adjustable template, amateurs, in order not to spend money on a tool, simply take a bar and drive 2 carnations into it at the right distance;
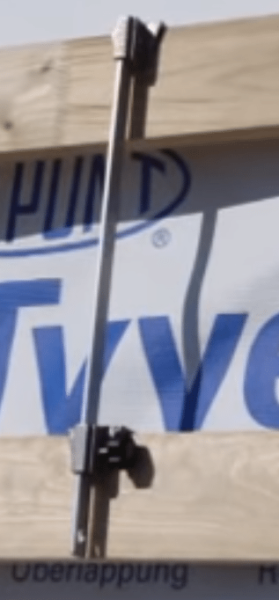
- On the ridge, 2 laths of the crate are butt-packed on each slope, so our ridge is closed on both sides with 200 mm planks.
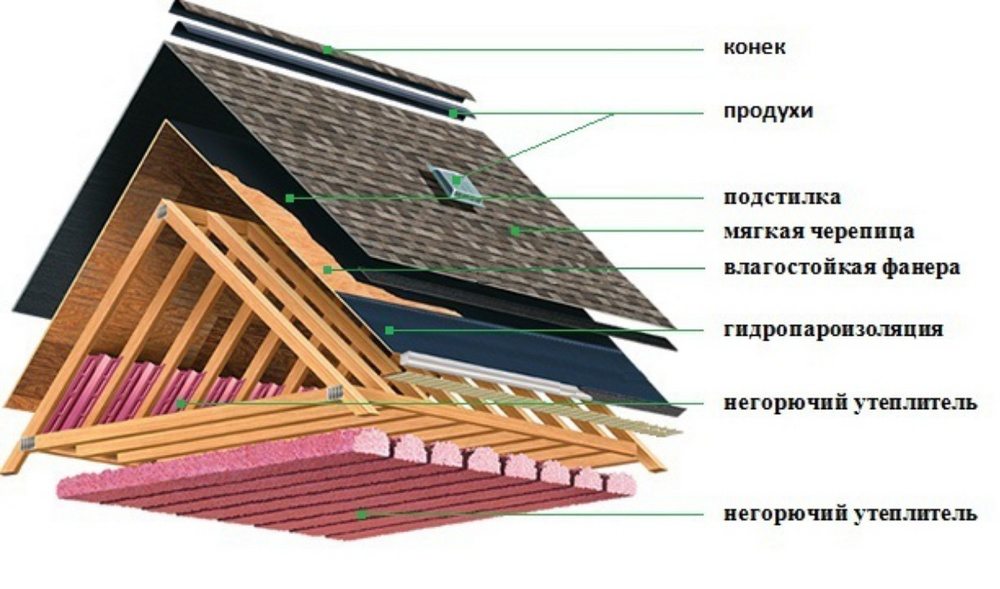
Step number 3: arranging the valley
- If a valley is provided on your roof, but the arrangement of the roof begins with this sector. There is a lower and upper valley. The lower bars are considered working, water flows down this gutter;
- The installation of the valley planks is carried out from the bottom up with an overlap of about 100 mm. The metal is attached to the crate along the edge with self-tapping screws, and the overlaps between adjacent sheets are smeared with sealant;
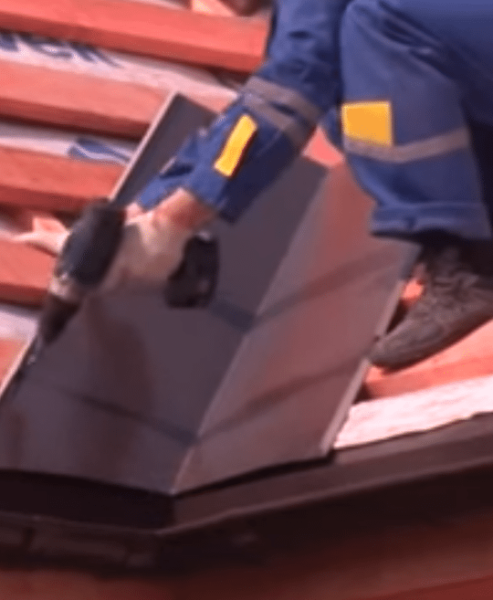
- The metal strips of the upper valley are mounted after the arrangement of the roof and are attached to the screws in the upper wave of the roofing sheet;

Personally, I preferred not to install the upper valley at all. The fact is that this element is purely decorative, plus in the fall foliage is clogged under the upper valley and it is very difficult to clean it out of there.
Step number 4: how to go around the chimney
- The junction strips are attached to the chimney first. You should start from the bottom bar, then the side bars go further and the top one is installed last;
- The lower junction bar is equipped with a so-called tie.A tie is an ordinary smooth sheet with a flanging, along which water, which will drain through the pipe and inevitably fall under the roofing, flows into the drainage gutter or the nearest valley, so the tie can be quite large, at least half the size of the slope;
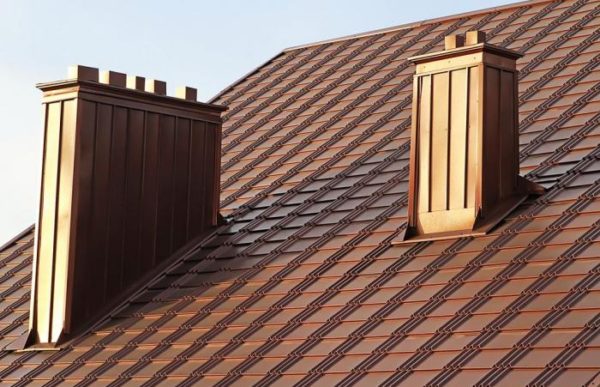
- In order for the adjoining strips to fit snugly with the chimney trunk, small sides are bent on the sheets from above, subsequently these sides must go into the grooves that we will cut along the perimeter of the chimney;
- In order to cut even grooves, first each flanging bar is applied to the installation site and a line is drawn along the upper edge with a marker;
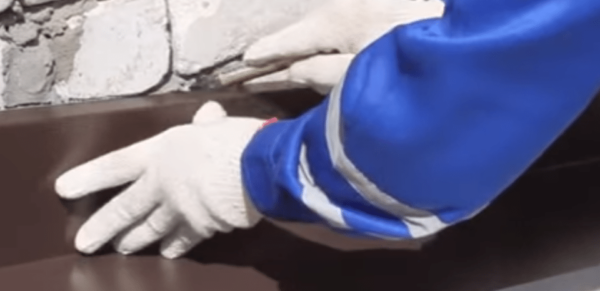
- In order to cut an even strobe, it is best to use a grinder with a large diameter disc. The strobe is cut out along the entire perimeter of the chimney in accordance with the markings, the depth is made according to the dimensions of the curved side;
- You will have a lot of dust from the grinder, so after you cut the strobe, you need to clean it with a soft brush, rinse well with water and wait until it all dries, otherwise the sealant will not take well on a wet and dirty surface;
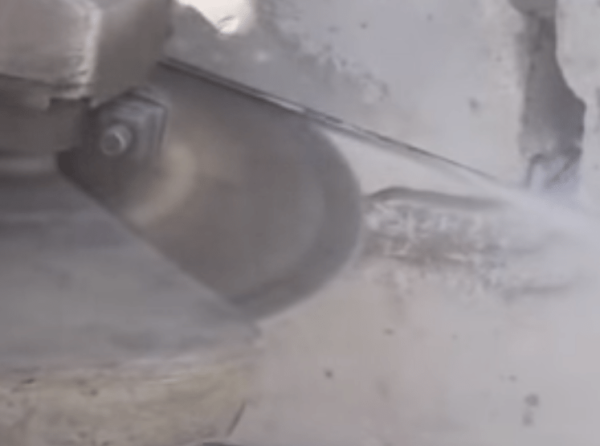
- Now the flanging sectors are inserted one by one. Each sector is sealed with a heat-resistant sealant in a strobe cut by us. And after that it is fixed with screws on a wooden crate;
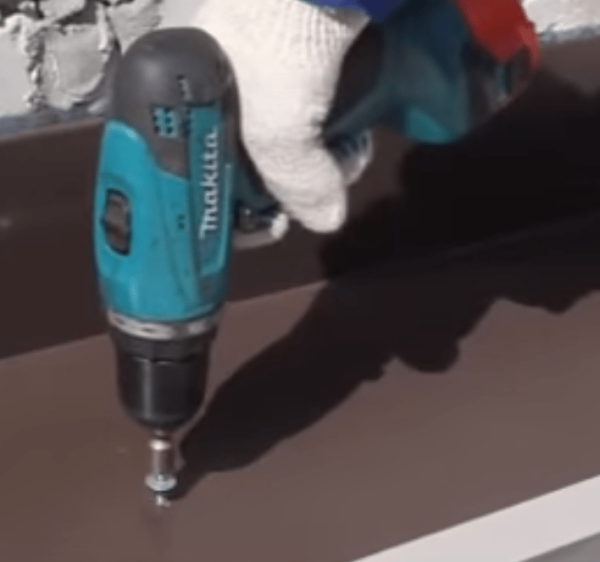
- After fixing all the flanging sectors to the crate, you will need to go through all the problem areas again and coat them with sealant. The area where the roof adjoins the chimney is the most vulnerable place for leaks;
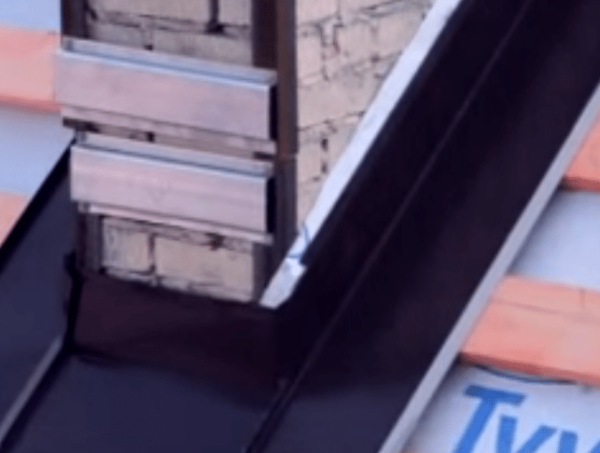
- Sheets of the main coating are already mounted on top of the flanging, and after the installation is completed, another upper flanging is installed. If the pipe is not sheathed with metal, then the technology for installing the upper flange is similar to the one I have already described above, only the lower bar here goes without a tie. On a pipe sheathed with a profiled sheet, the flanging is attached without sealant, simply on self-tapping screws or rivets.
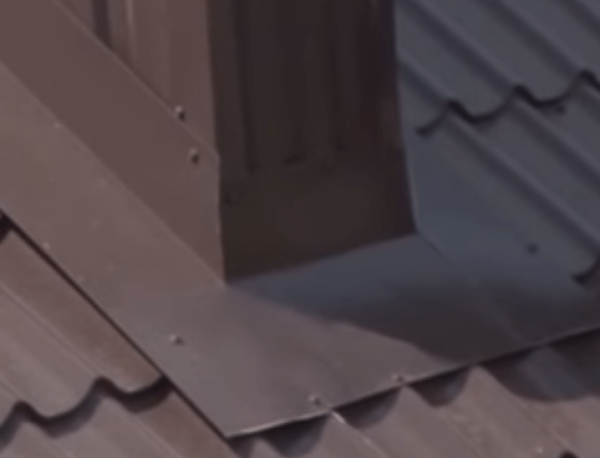
Step number 5: installing fixtures for the drain and installing the cornice strip
- On such a roof, sheds for a drain are installed even before the installation of the main coating. The drain itself should go with a slope of about 3 mm per 1 linear meter. In order not to measure each bar separately, they are marked all at once, numbered and then bent;
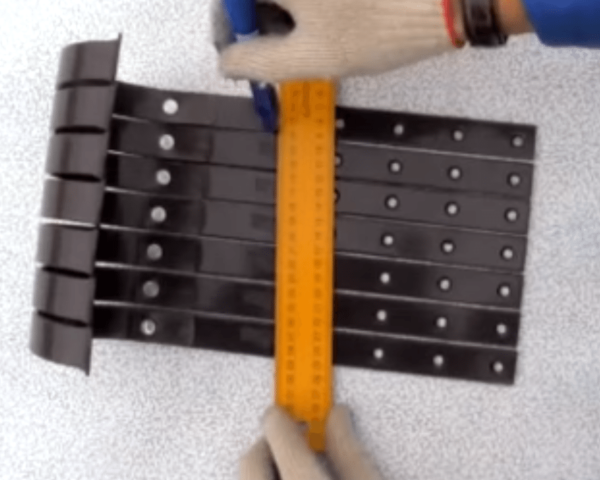
- It is best to bend the gutter holders with a strip bender, in this tool the desired angle is immediately set. Of course, at home you can use a vise and a hammer, but it will take 5 times more time;
- The strips of the holders are attached to the extreme paired laths of the crate with self-tapping screws, with a step of half a meter. Here, be careful with the numbering of the planks, the slightest mistake can knock down the angle of inclination and then, water will constantly stagnate in the gutter, and even worse, garbage will collect;
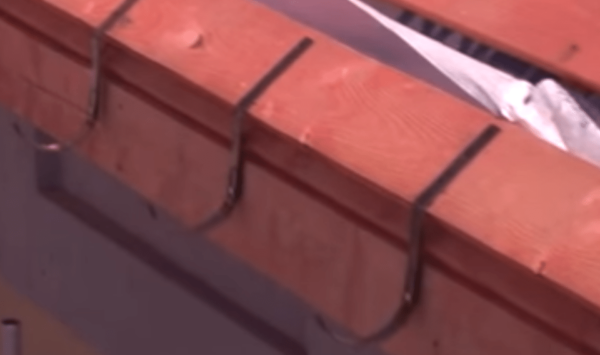
- Now you will need to decide where you will have the outlet funnel, and cut a V-shaped hole for the outlet funnel in the drain with a hacksaw;
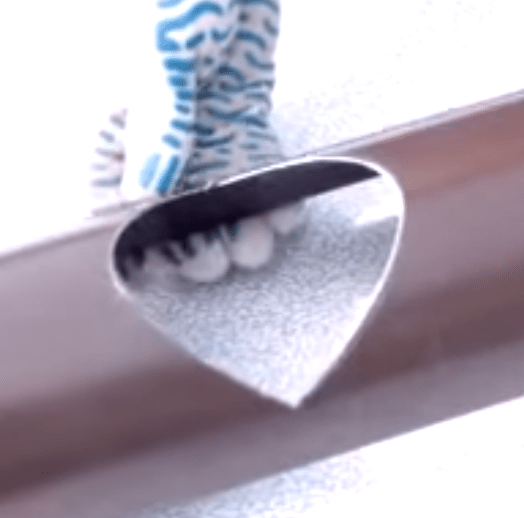
- The holders have special hooks for fixing the gutter, when you insert the drain into the holders, these hooks are bent and firmly hold the gutter.Plugs are mounted on the ends of the gutters. The drain funnel has several hooks, it is put on the gutter from below, after which the hooks are bent at the edges of the gutter;
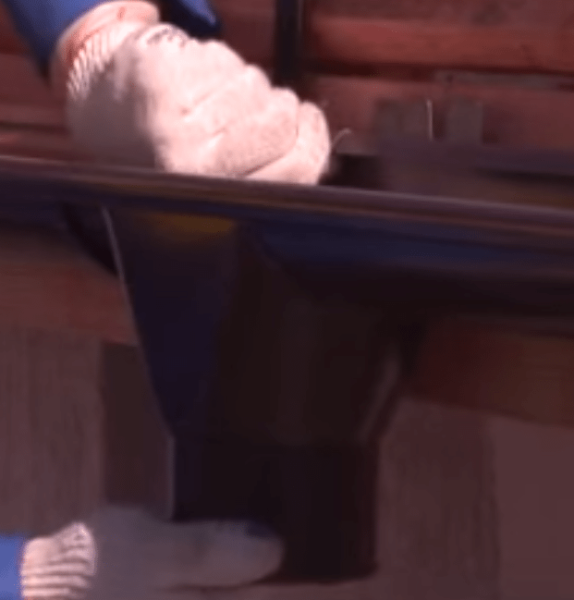
- The gutters are inserted into each other and interconnected with an overlap. In order for the junction to hold firmly and not leak, a semicircular bracket with a rubber seal is put on it from below, there are locks on such brackets that snap into place and are fixed with a tongue;
- A cornice strip is mounted on top of the gutter, which should overlap the edge of the drain; for reliability, such a connection is made with a hook. The upper part of the plank is fixed with self-tapping screws on the crate, after which the edge of the waterproofing sheet is applied and glued to it. As a result, even if water seeps under the roof, it simply flows down the waterproofing sheet into the gutter.
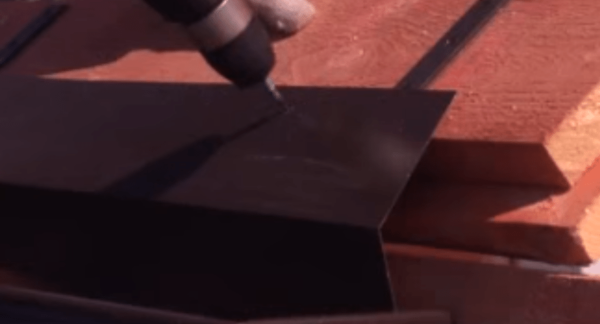
- If the roof has an impressive size, then it makes sense to install dividers and water pressure absorbers in the most problematic places of the drain, so that during a rainstorm the water does not overflow over the edge of the drain;
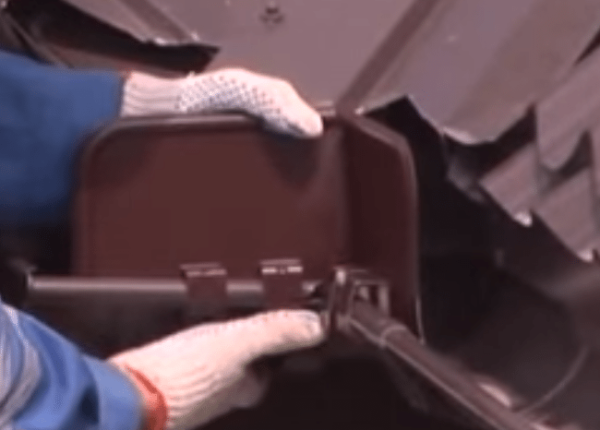
Step number 6: installation of sheets of metal
- On complex roofs, before lifting the sheets up, they need to be cut out on the ground. To do this, the sheet is placed on a solid base, marked and cut. Naturally, with a metal thickness of half a millimeter, the edges of the cuts should in no case be left unprotected, corrosion “eats” them very quickly;
- To protect the edges, you can use a special paint in aerosol cans, which manufacturers offer, but I think that this is an extra “pumping out” of money from the buyer, so when I have to cut a metal tile, I put a jar of alkyd-urethane varnish next to it for outdoor work, and after cutting I immediately cover the edge of the sheet with a brush. If the varnish is used only for these purposes, then one small jar is enough to process the joints on a large roof;
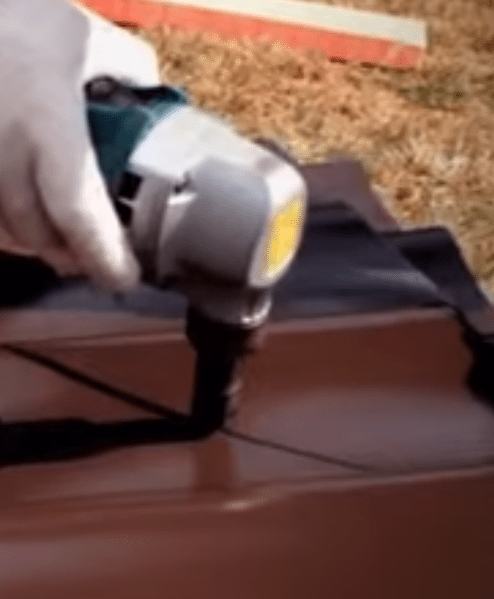
- Sheets of metal tiles are a rather fragile thing, with such a thickness of metal and dimensions they are very easy to damage or bend, so the material must be lifted onto the roof very carefully. The easiest way is to put 2 or 3 long logs from the ground to the roof and move the sheets up along them.
Although this article is about how to cover the roof with a metal tile with your own hands, you do not need to understand everything so literally. Honestly, I have not yet seen anyone single-handedly cope with such a task. Ideally, you will need three more assistants, their professionalism does not play a special role, the main thing is that there is someone to support and serve.
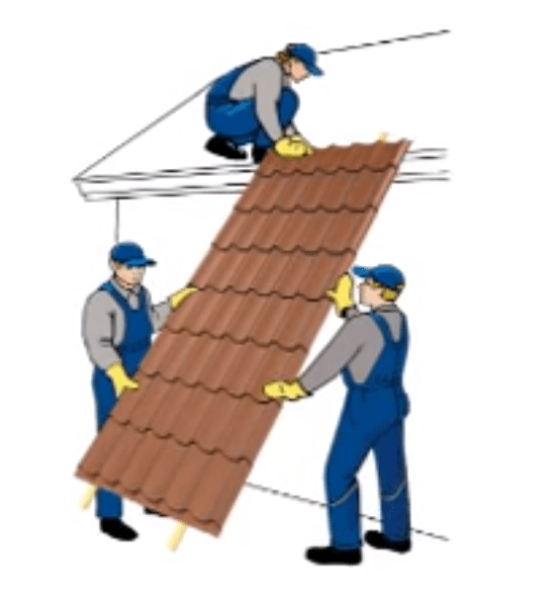
- As I already said, it is much easier to work when the length of the sheets is equal to the length of the roof slope, in this case the first sheet is aligned along the ridge and along the edge of the roof, after which it is fixed with self-tapping screws;
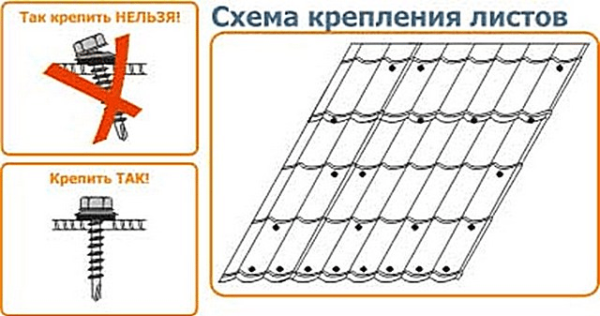
- All self-tapping screws used for the installation of metal roofing must be with press washers, often the color of the screw heads is matched to the color of the roof. When fixing sheets, self-tapping screws are driven through the wave, in a checkerboard pattern, into the lower part of the wave;
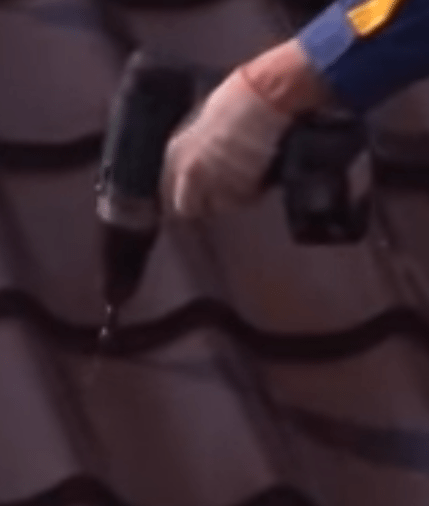
- In different models of metal tiles, the sheet joining system may differ, but generally speaking, the sheets are overlapped;
- Short sheets are mounted a little differently than long ones, their laying is carried out according to the batch principle. That is, 3 sheets from the edge of the roof are mounted first. Then the next row is attached above them, this will be considered one package. Now you move to the side and also begin to lay the second package of sheets and so on until you sew up the entire roof;
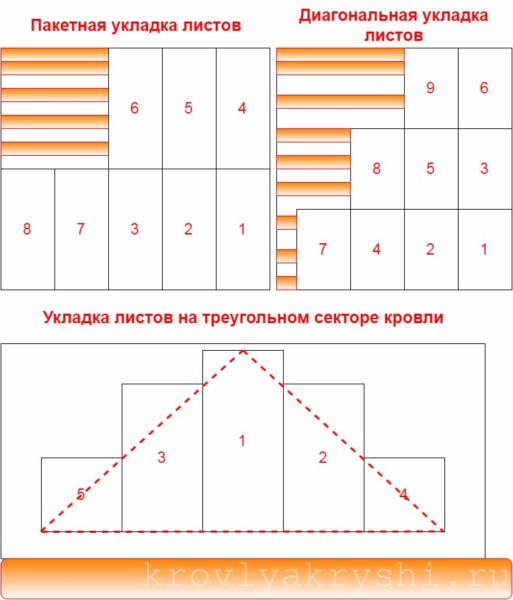
No matter how hard you try, in any case, you will have to step on and walk along the already mounted sheets. Remember that the metal is thin, and this should be done very carefully. Shoes should be soft, feet should be placed only on the lower edge of the wave and it is desirable to fall on the laths of the crate, their location is easy to determine by self-tapping screws.
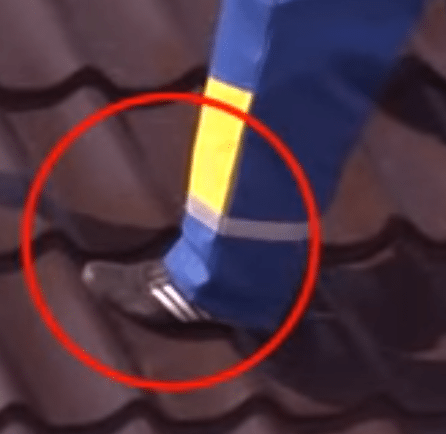
- It is often difficult for beginners to work with a screwdriver, or rather, not even with the tool itself, but with the level of tightening screws. In this case, it is important to find a middle ground; it is impossible to crush or undertighten the screws. There are no special recommendations here, you just need to fill your hand.
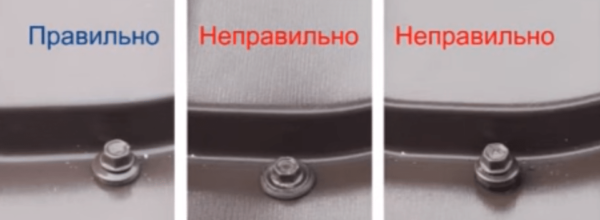
Step 7: Installing the ridge and end rails
- Ridge bars are semicircular and triangular. From the point of view of operation, there is not much difference in them, but it is believed that semicircular planks look better, respectively, and they cost more;
- From the ends, semicircular ridge slats are closed with plugs. Plugs, in turn, are also straight and semicircular, in this case, semicircular plugs are used on tent-type roofs, and straight ones on standard ones;
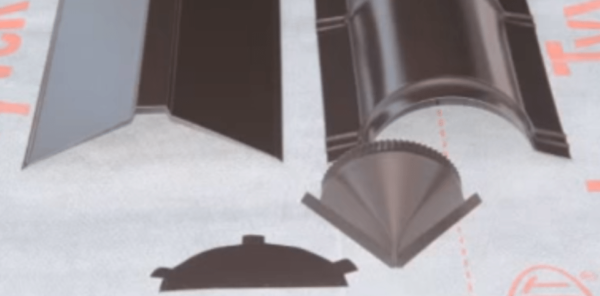
- Whichever plugs you choose, they are fastened with self-tapping screws.That is, bend the fixing tabs on the plug at 90º, insert it into the end of the bar and fix it with a self-tapping screw or rivet;
- First, you simply attach the bar to the ridge and put a ridge seal under it, it is selected for the sheet configuration. The ridge bar itself is screwed to the sheets of metal tiles with self-tapping screws, you need to fasten it through one wave;
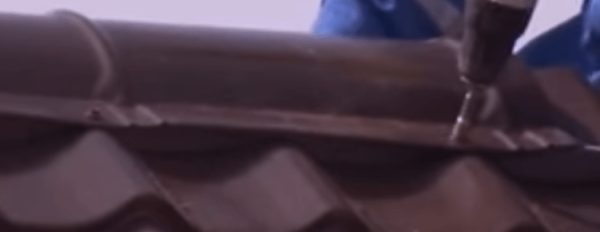
- Special end strips are mounted on the ends of the roof slopes. From above, they are wound under the ridge bar and immediately fixed with a self-tapping screw. Then, along the entire length, they are fastened with roofing screws with the same pitch as the sheets of metal tiles.
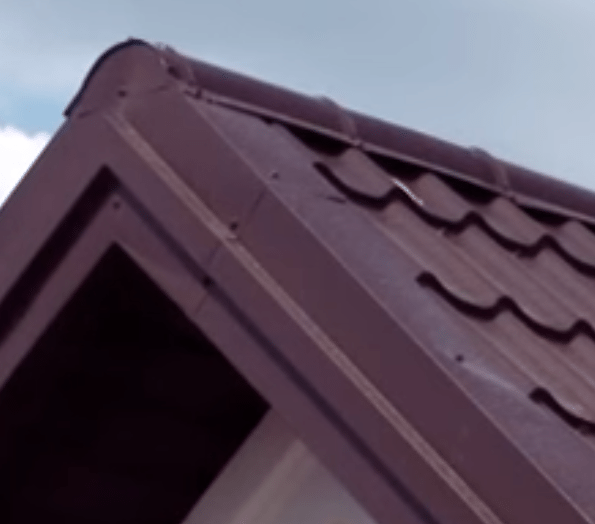
Step #8:. installation of ventilation and antenna outlets on the roof
Not a single modern roof can do without the installation of sewer, ventilation and antenna outlets on it. The installation technology of such structures is generally similar.
The most difficult is the installation of a sewer sewer pipe (a sewer pipe is called a sewer ventilation pipe).
- All such outputs are mounted on the upper crest of the wave. In the set of any such overlay there is a paper template, which serves to mark the base into which this overlay will crash. You just need to take this template, put it on the top crest of the wave and outline it with a marker;
- After that, take scissors for metal and cut an even hole in the roof, do not forget to varnish the edges of the hole;
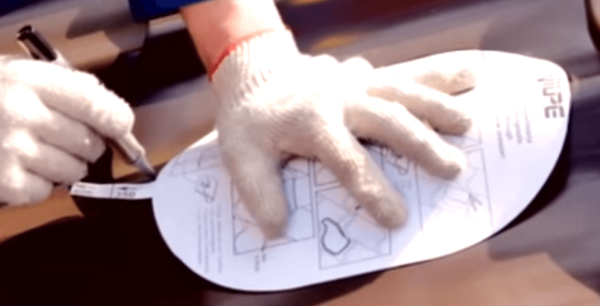
- Further, the instruction prescribes to remove the metal tile sheet and mark and cut a similar hole in the waterproofing sheet along the inner edge of the lower seal and cut it with a knife;
- Now you need to generously lubricate the edges of the sealant with sealant, bring it under the waterproofing, bend the fastening strips and screw these strips to the roofing crate with self-tapping screws. After that, the sheet of metal is put in place;
- Although when I was faced with the need to install a fan outlet, I did not completely remove the sheet. After the window in the metal sheet was cut out, I marked and cut out the window in the waterproofing, and then I cut off most of the mounting strips on the sealant and fixed the sealant not on top of the crate, but at the end of the bearing strips. Of course, I had to tinker, but it was not necessary to completely remove the sheet of metal tiles;
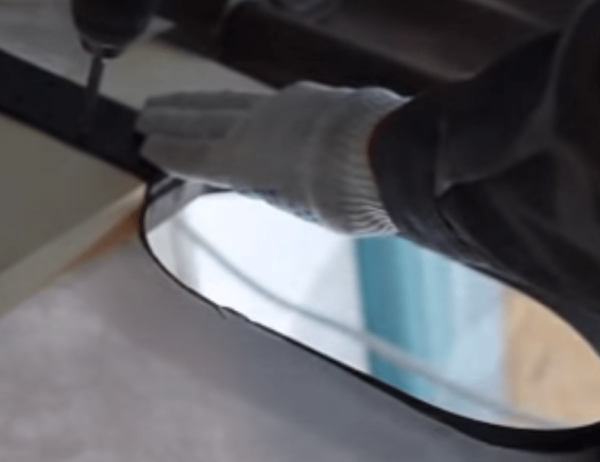
- On roof slopes with large areas, it is necessary to equip under-roof ventilation. It is a little easier to install than a fan one. Here you only need to cut a window in a metal sheet according to the template, smear the edges of the lining with sealants and screw this lining to the roof with self-tapping screws. Since the ventilation is under-roofing, it is not necessary to touch the waterproofing sheet;
- The antenna output is approximately the same. Here, of course, the waterproofing will have to be perforated, but a fan pipe with a diameter of about 100 mm is one thing, and a thin tube for installing an antenna output is quite another.
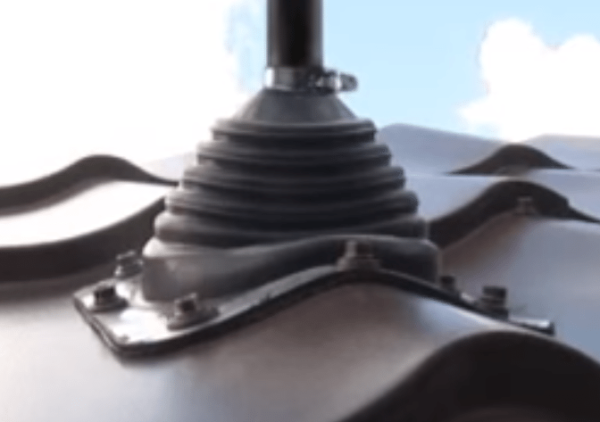
Step number 9: we mount the snow retainer and walkways on the roof
In most of our great power, heavy snowfalls in winter are not uncommon, and on roofs with a serious square there is a need to install snow retainers.
They are two parallel metal tubes mounted on several vertical plates.
- The bearing bars of the snow retainers are installed on the lower part of the wave and fastened with several bolt screws. To do this, you need to pre-drill several holes for bolt screws in the roofing sheets;
- Bearing strips are installed on rubber gaskets, through which the bolt screws are screwed into the roof;
- At the last stage of installation, profile tubes are inserted and fixed into special holes in the carrier bars. The snow retainer itself can be built up as long as you like;
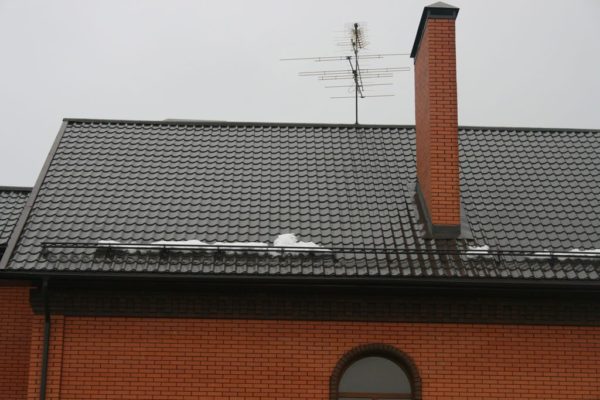
- Since the roof is usually quite steep and smooth, special transitional bridges with an adjustable angle of inclination are mounted on it for safe movement. The installation of such bridges is similar to the installation of snow retainers.
- The only difference is that the guide rails are attached both to the roof and to the bridge itself, after which the desired angle of inclination is set and the structure is finally fixed.
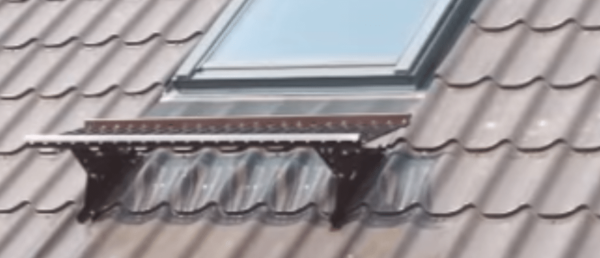
Step number 10: arrangement of insulation
- To insulate the roof, cotton slabs of thermal insulation are used, in this case basalt wool is best suited. Do not confuse cotton slabs and cotton mats. Plates have a dense structure and clear shapes, and mats are a soft insulation. Surely most of you have seen glass wool, so this is an example of a cotton mat;
- Plates need to be cut 2 - 3 cm wider than the distance between the rafters. This is done so that the insulation fits tightly between the rafter legs;
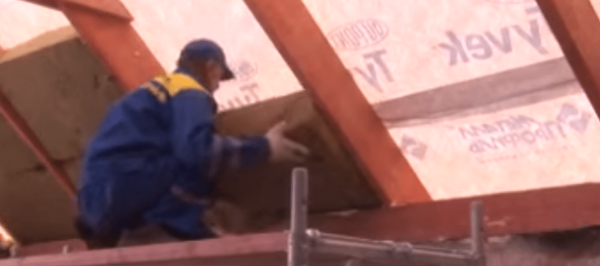
- Further, a vapor barrier membrane is stretched over the insulation and fastened to the rafters with a stapler, it is needed so that the cotton slabs do not absorb moisture;
- Keep in mind that such membranes allow steam to pass in only one direction, as there are corresponding marks on the membrane itself. In this case, the direction of steam movement should be from the stove to the room. Otherwise, since we have waterproofing installed on top of the insulation, moisture will accumulate in the cotton slabs and they will eventually become unusable;
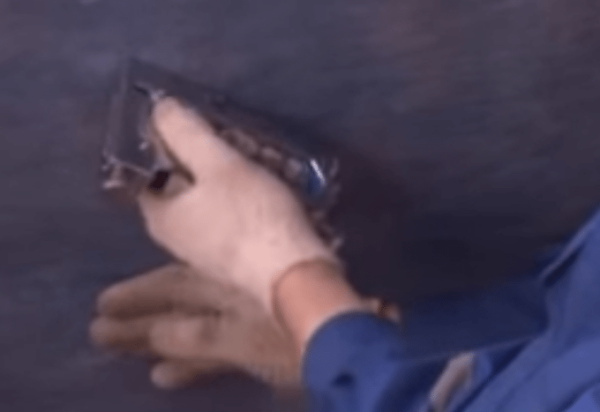
- The interior attic can be sheathed with any suitable material. Most often, the owners choose between clapboard, plywood and drywall.
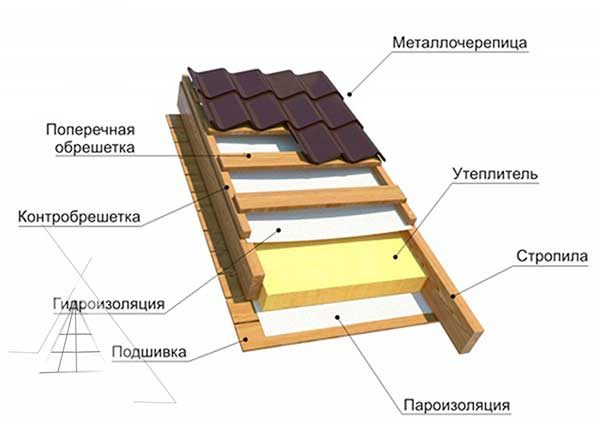
Conclusion
I tried to describe in as much detail as possible how to properly cover the roof with metal tiles. The photos and videos in this article show the intricacies of this process. If after watching you have any questions, write them in the comments, we'll talk.
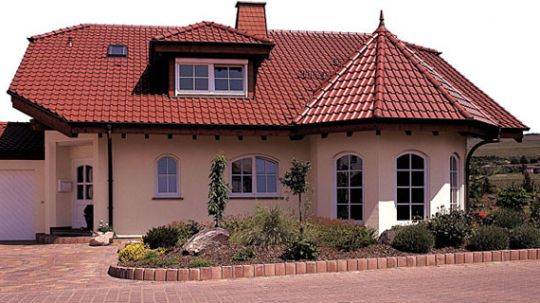
Did the article help you?