Today we will figure out how to make a polycarbonate canopy with our own hands. This type of construction is distinguished by reliability and simplicity, which is very important for those who do not have experience in construction work. Just follow all the recommendations below, and in a couple of days you will enjoy the result of the work.
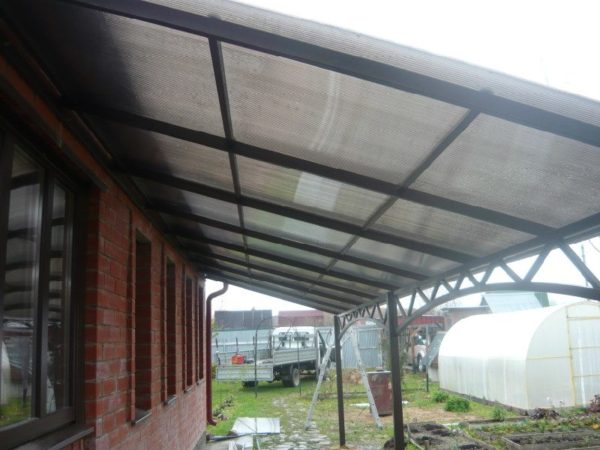
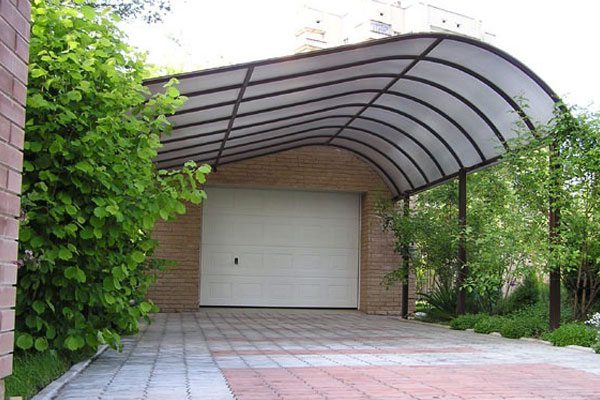
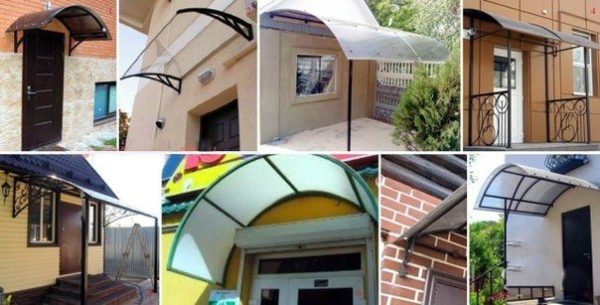
Description of the workflow
To understand the work as best as possible, it needs to be broken down into separate stages:
- Creation of a project of the future design;
- Purchase of materials and tools;
- Site preparation;
- Foundation construction and installation of supports;
- Assembly of the structure;
- Polycarbonate attachment.
If you have a canopy over the porch, then the structure can be attached to the wall, in which case you need to consider a secure fixation system.
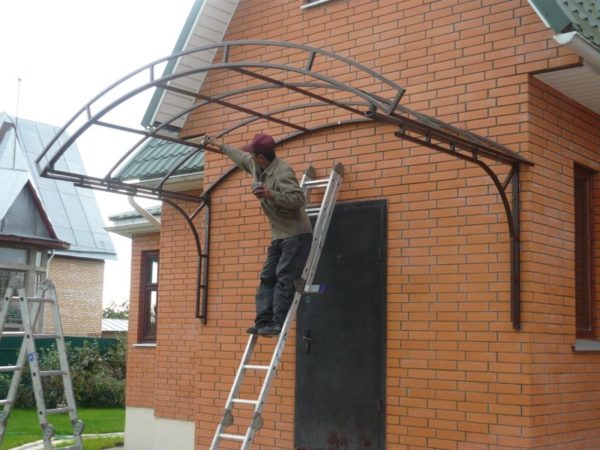
Stage 1 - creating a project
Making polycarbonate canopies with your own hands is very simple for the reason that you can realize almost any idea.
But as part of creating a project, you need to consider several factors in order to get the best result:
- To begin with, it is worth deciding on the type of structure. It can be free-standing, attached to a building, or completely wall-mounted.. It all depends on the type of canopy and the purposes for which it will be used. Think carefully before choosing a specific option, do not miss a single nuance, so that later it does not turn out that the design is not very convenient to use;
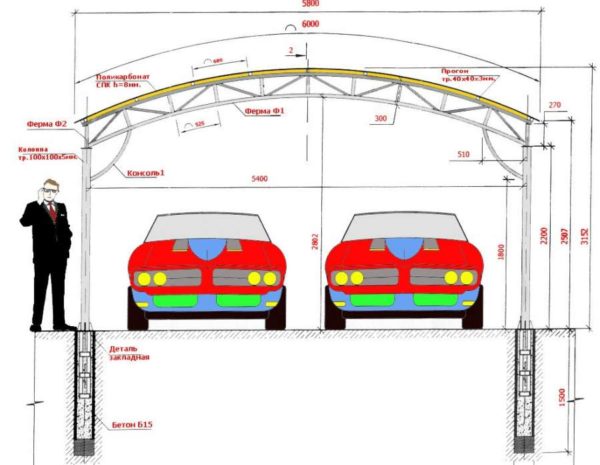
- You also need to decide how much space you have. Often you have to proceed not from your wishes, but from the free space that can be used. If there is enough space, then it is better to make the structure larger, as practice shows, extra space under the roof will never hurt;
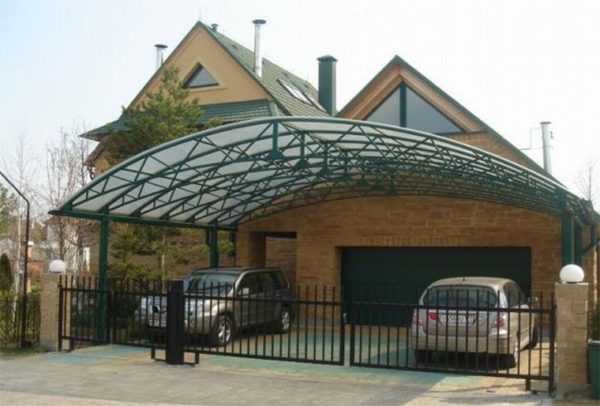
- A drawing is being made. Accuracy is not needed here, it is important to note all the main dimensions so that you can roughly imagine the final result and make material calculations. Do not chase fancy shapes, this greatly complicates the process. It is much more reasonable for the first time to take up the construction of a shed canopy or a simple arch with a minimum of details and a simple design.
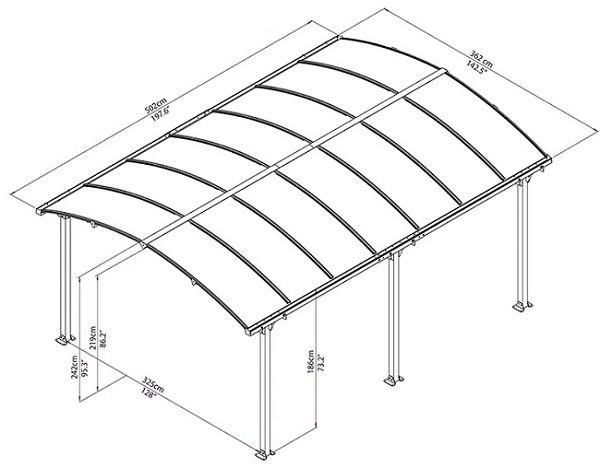
If you chose the option with curved arches, then I advise you to purchase them ready-made. Without certain skills in welding and metal forming, it is unlikely that you will be able to get the same trusses.
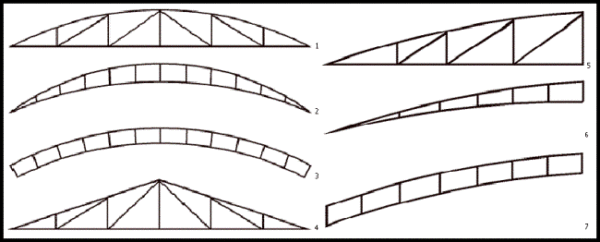
Stage 2 - purchase of materials and tools
When the sketch is on hand, you can proceed to the calculation and purchase of materials. We will consider a metal canopy as more durable and reliable. The list of everything you need is indicated in the table.
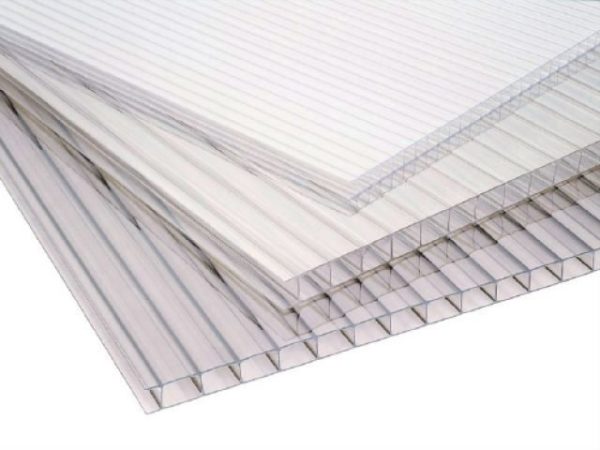
Material | Description |
Polycarbonate | Polycarbonate on the roof of the canopy must have a thickness of at least 6 mm, thin options are unreliable. It is better to take sheets of 8-10 mm, they weigh a little and have high strength. As for the color, the choice is yours, if you need natural light, then a transparent material is best. |
profiled pipe | For racks, it is best to use elements with a section of 80x80 or 100x100 mm. For runs, options of 40x40 mm are suitable, and 40x20 mm is enough for the crate. The quantity is determined by the drawing, it is often possible to buy blanks of the desired length, which simplifies the workflow |
Mortar and mortgages | For a strong fastening of the supports, it is necessary to put embedded elements that are poured with concrete. This allows you to get a very solid base that can withstand any load without any problems. |
fasteners | Polycarbonate is fastened with special thermal washers. If there are joints between sheets, then a connecting strip is needed, the ends are closed with special end elements |
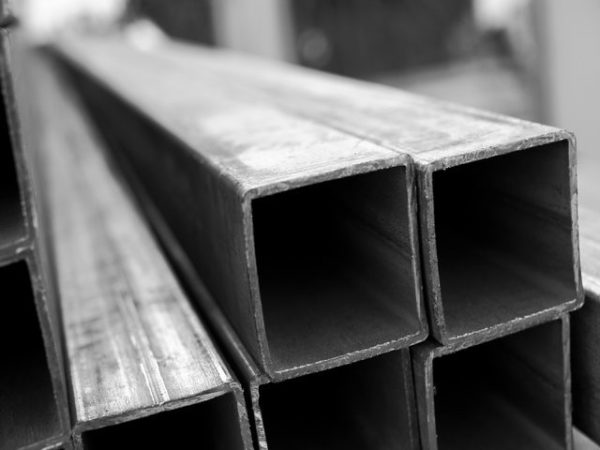
In addition to materials, you also need a tool; without it, you cannot do the work with your own hands.
The main set of devices looks like this:
- Shovel for digging holes for concreting, preparing mortar and laying it;
- Bulgarian and several cutting discs for metal for trimming elements. At the same time, take a cleaning disk, it will also be needed during work;
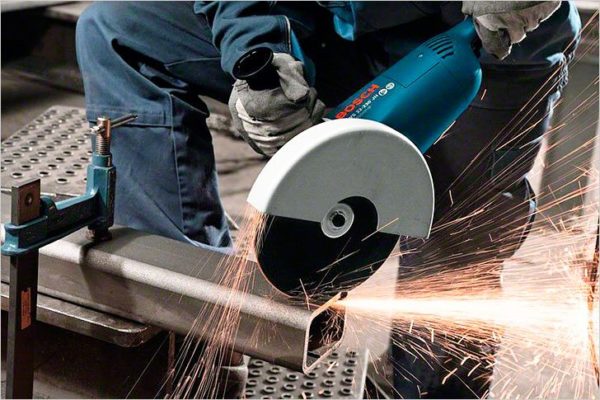
- All connections are easiest to do by welding. If you do not have a machine, then it is worth attracting a welder for an hour. But you can rent equipment, it is inexpensive, and you will only have to purchase electrodes;
- A brush and paint are needed to create a protective coating. It is best to use 3 in 1 options that contain paint, primer and anti-corrosion additive;
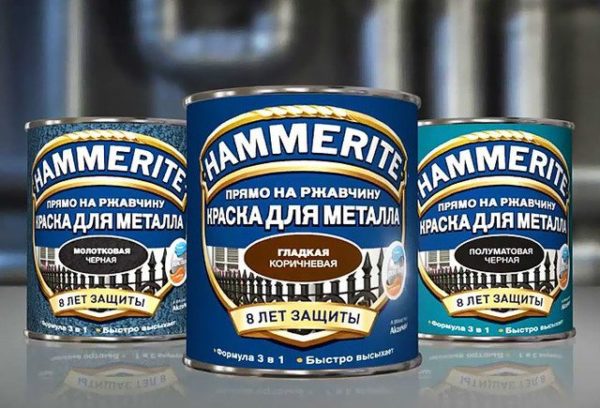
- Polycarbonate is fastened to the frame using a screwdriver with a special M8 nozzle or a bat. Depends on the type of screws;
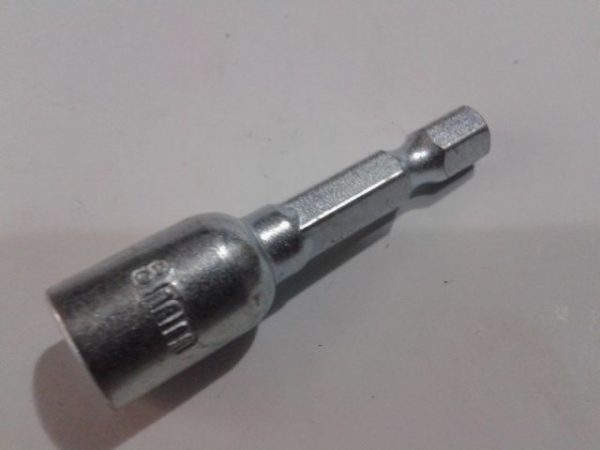
- For measurements and markings, a tape measure and a felt-tip pen are needed. And to control the planes, a level is required.
Stage 3 - site preparation
The instruction for the work is quite simple:
- First you need to make all the appropriate measurements and make the layout of the site. To do this, pegs are driven into the ground, between which a building cord or fishing line is pulled. Don't forget to check the diagonals to make sure the construction geometry is not skewed;
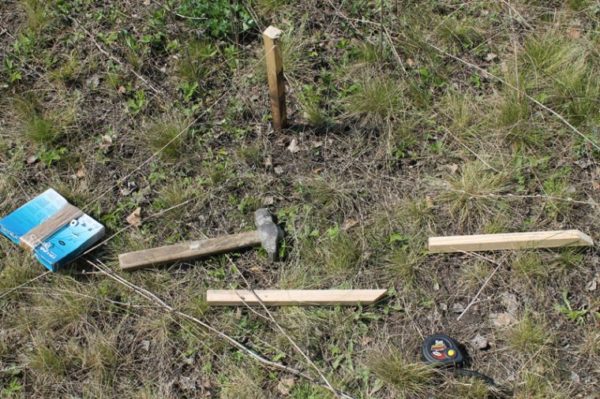
- Then you need to clear the area. You must decide in advance which coating will be laid under the canopy and, based on this, prepare the surface. Most often, the soil is removed and a pillow of sand or gravel is poured. Also, take care of drainage, so that during precipitation, water does not descend under the roof. To do this, you can make the surface slightly higher than the site or lay it with a slight slope;
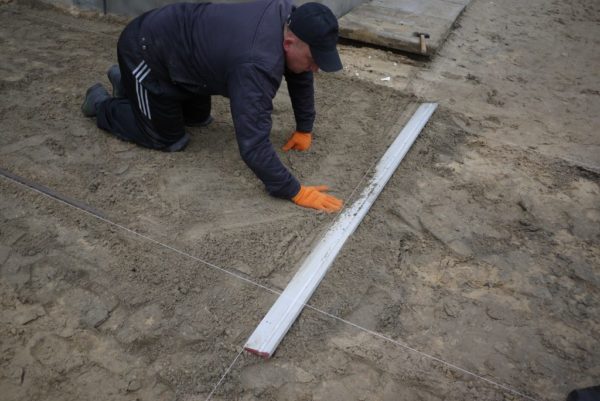
- At the locations of the supports, holes are dug 100-120 cm deep. Work can be done with a shovel, or you can use a special drill, if you have one at hand. The main thing is that the pit should be deeper than the soil freezing line in your area.
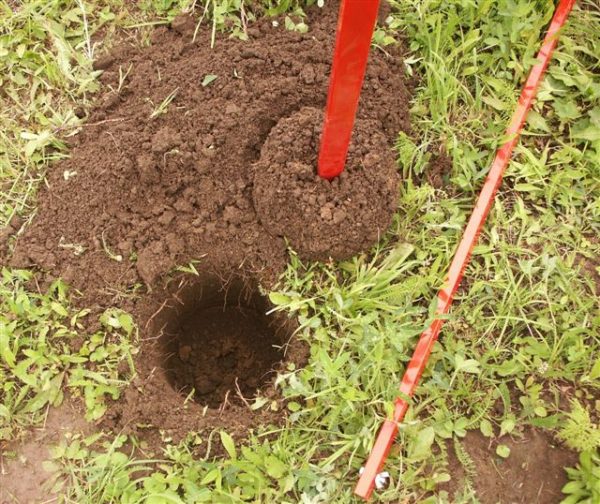
Stage 4 - installation of supports
Installation of canopies begins with the installation of load-bearing elements. Their number depends on the design and size.
The work is done like this:
- First you need to decide how you will fasten the elements. Embedded elements can be concreted and fastened to them with bolts. You can insert the pipe into the pit and so concrete. The second method is much simpler, the first one is good because, if necessary, you can quickly disassemble the structure;
- If you concrete the pillars, then the work is done as follows: stones or large gravel are thrown into the pit with a layer of 20 cm.Next, the pillar is set to the desired height, if necessary, stones can be added. Then all the voids on the sides are thrown with stones, at the same time the position of the element is leveled. The vertical is checked from all sides so that there are no distortions;
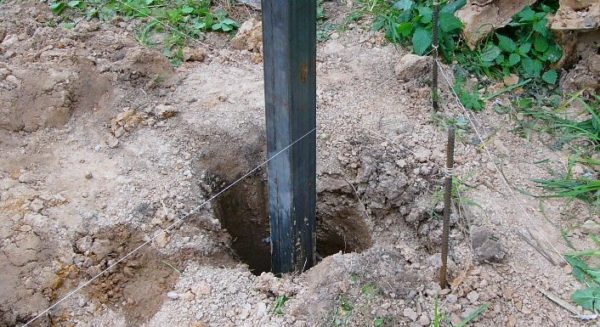
- A solution is prepared from sand and cement in a ratio of 4: 1. It must be liquid enough to penetrate the voids between the stones and fill the hole completely.. Filling is done to the ground level, so that the mass penetrates better, you can pierce it with fittings from time to time;
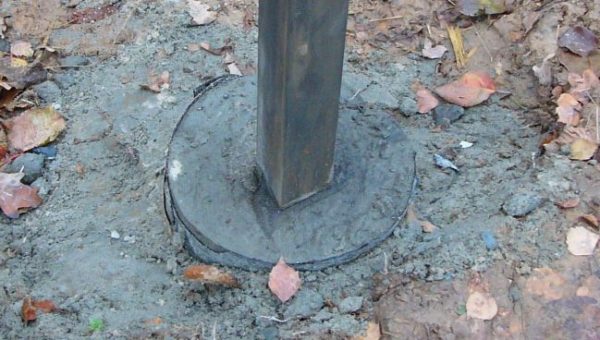
- If you put mortgages, then they are first filled in, it is important to set the elements very accurately vertically and horizontally. The node is concreted, after which it is necessary to weld the mounting pad to the base of the support. After the concrete has hardened, it is fastened with bolts, it is better to take stainless fasteners.
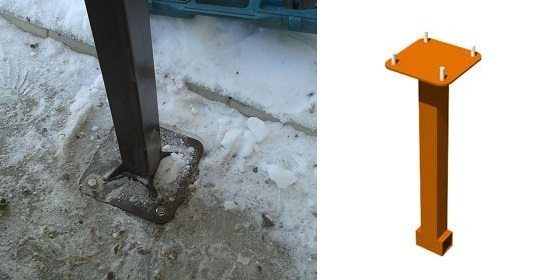
Stage 5 - assembly of the canopy frame
This stage consists of the following steps:
- First of all, longitudinal supports, which are called Mauerlats, are attached to the racks. If you have a ready-made set, then fastening will be done using bolts. If you assemble the system yourself, then the easiest way is to weld Mauerlat to the racks;
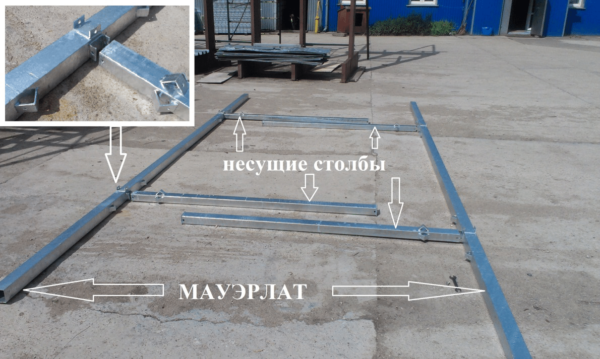
- Next, you need to weld farms. If you have the simplest option and in the metal frame there is only a Mauerlat and slope elements, then this step is skipped. But most often reinforced elements are made, which are placed in increments of no more than a meter. They need to be done in advance, check if they are all the same;
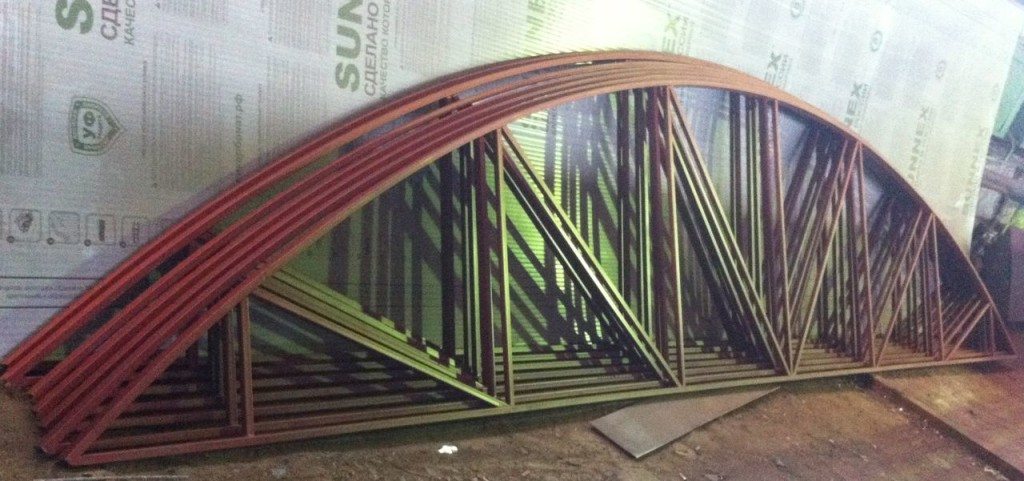
- You need to install farms. First of all, each element is welded to the base, and then stiffeners are placed between them. They are also welded to create a crate on which polycarbonate will be attached;
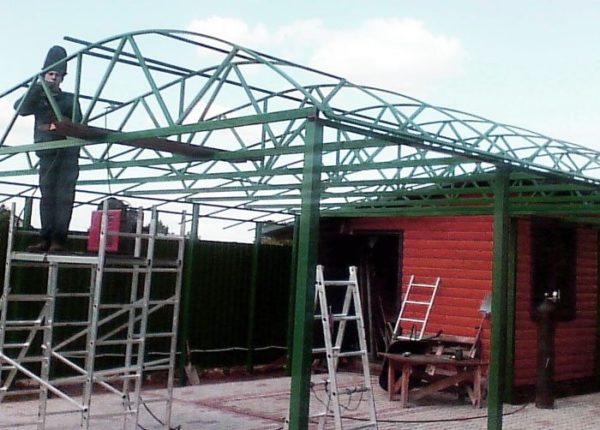
- After finishing work, you can clean the metal where necessary. After that, all surfaces are degreased with gasoline or thinner. The finished base is painted, pay special attention to all joints and hard-to-reach areas. It is important to cover the entire surface to protect the metal from corrosion.
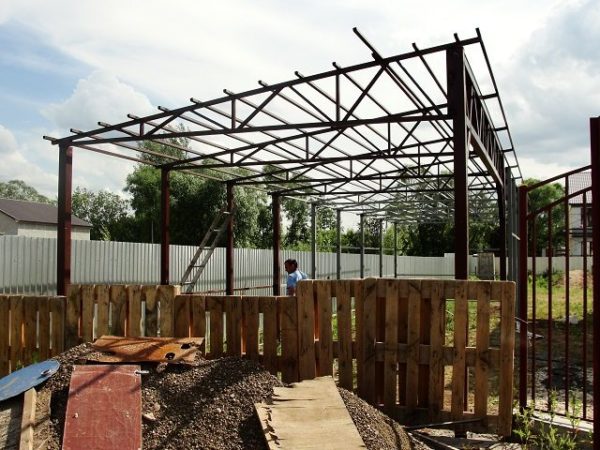
If you are making a visor, then you just need to weld the frame according to the drawing, paint it and fix it to the wall. Installation is carried out using anchor bolts with a diameter of 12 mm and a length of 120 mm or more.
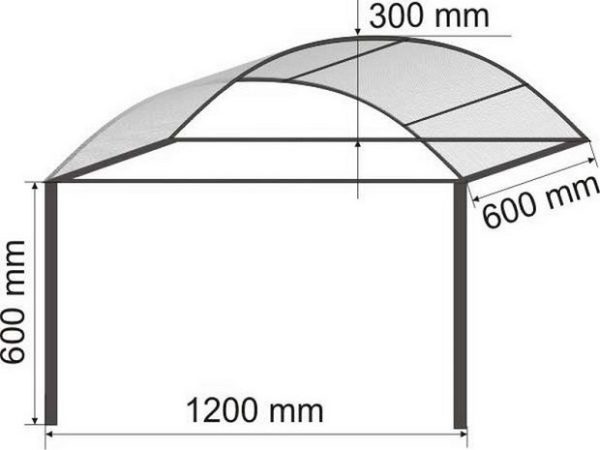
Stage 6 - fixing polycarbonate
This part of the work consists of the following:
- Polycarbonate sheets unfold on a flat surface. You need to identify the UV-coated front side, which usually has a protective film on it. Next, dimensions are made, and the surface is marked for cutting. You can cut material up to 8 mm thick with an ordinary construction knife, running it along a ruler or level. Thicker options are cut with an electric saw;
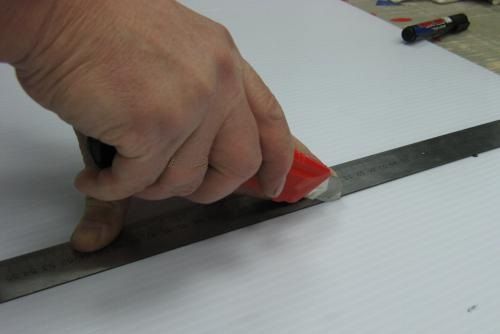
Remember that polycarbonate bends perfectly only perpendicular to the voids. If you bend incorrectly, the sheet will break.
- The sheet is laid in place and leveled so that it lies flat. After that, you can start drilling holes, the diameter of which should correspond to the size of the fastener. They are located in increments of no more than 40 cm;
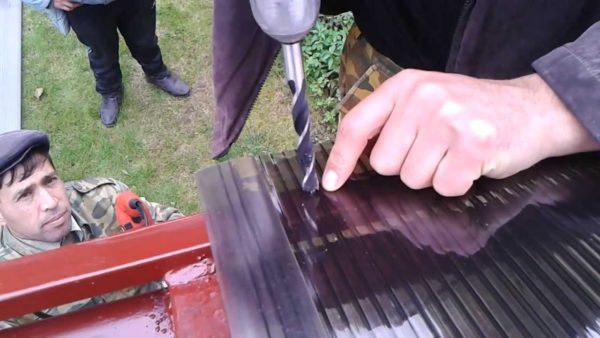
- Fastening is very simple: first, a seal is placed, a washer is placed on it, then a self-tapping screw with a drill tip is screwed. After finishing work, the fastener head is closed with a cap, a very reliable and durable connection is obtained. Before mounting, remove the protective film, then you will not pull it out from under the washers;
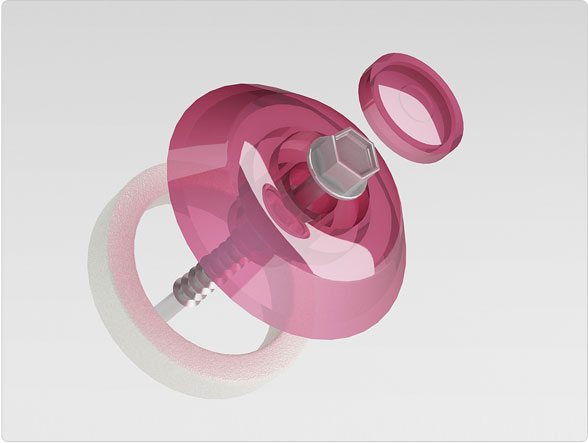
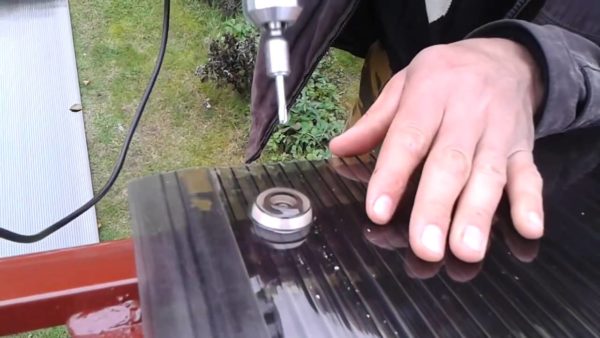
- If you need to connect sheets, then I recommend using a special aluminum bar. Its design and mounting method are shown in the diagram below. Everything is simple: a profile with seals is placed on the lower and upper sides and tightened with a self-tapping screw, and the joint is closed from above with a decorative strip;
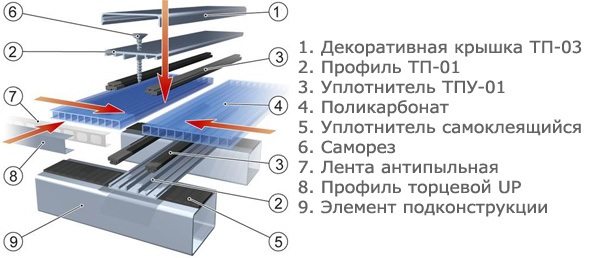
- The end plate is attached like this. First, the end is glued with adhesive tape for additional protection, and then a plug is put on. When working, it is easiest to help yourself with a spatula, bending the edge of the bar.
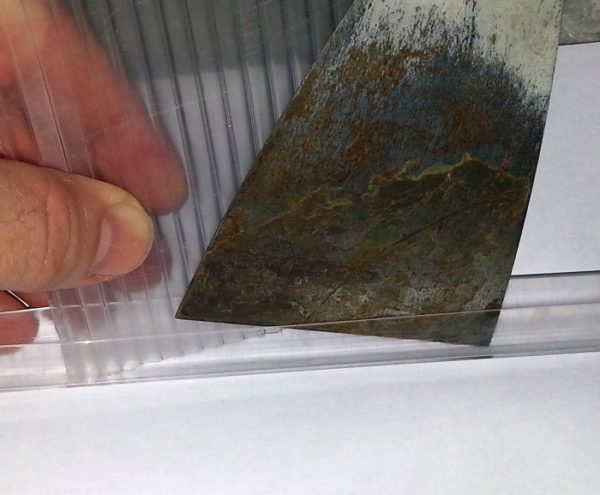
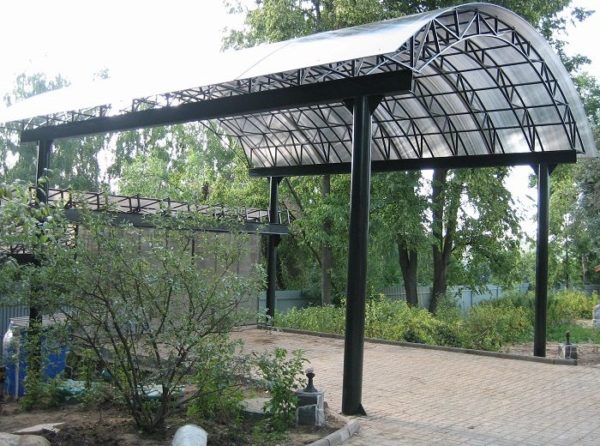
Conclusion
Making a canopy on your own is easy, use the recommendations from this review, and you will get an excellent result. The video in this article will show you some of the important points of the workflow. If you have any questions, then write them in the comments, we will analyze each of them.
Did the article help you?