Roll materials have been used for roofing for a long time. They are relatively cheap and are almost the only solution for waterproofing flat roofs. The monopoly was held by roofing material for decades, but then there were roofing built-up materials. What they are, and what they can offer builders - later in the article
Traditionally, soft roofing from rolled materials on flat roofs of multi-storey buildings was laid on hot bituminous roofing mastic.
To do this, a special platform was equipped on the roof itself, where, in addition to the coating material itself, a mastic boiler, the mastic itself, as well as fuel for the furnace were dragged with winches.
With a small number of storeys, “firing” work was carried out below, and the molten mastic in buckets and cans with the help of the same winch rose to the place of laying, leaving black marks on the walls of the building. At the same time, if the housing office took care of its residents, such a picture was repeated once every ten years, or even more often.
This is the life of roofing material - cardboard impregnated with bitumen. Over the years, he gains water, loses flexibility. As a result, in winter, in frost, the sheets break due to temperature deformations, and in summer, since the cardboard does not have biological stability, they rot.
This is not the case with modern built-up roofing material. It has a more complex structure, uses new types of base, has increased plasticity and frost resistance, therefore it is not subject to biological decomposition, and it tolerates winters much better.
The first difference between this class and its predecessor is that such materials do not require prior application of a layer of molten mastic to the base of the roof. They themselves contain it on the reverse side.
All produced built-up roofing materials are reduced to several groups according to various criteria. The first of these is the bituminous mixture used.
It can be made on the basis of oxidized bitumen, or bitumen with polymer additives. Oxidized bitumen is significantly cheaper, but has more modest performance characteristics.
Since raw bitumen melts at a temperature of already 50 ° C, air is blown through the hot mixture to increase it. In fact, this is a natural aging process, as the bitumen oxidizes during it.
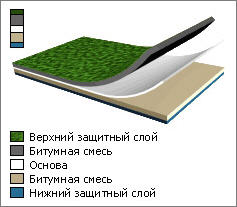
In this case, the melting point rises, but subsequently, under the influence of atmospheric air and sunlight, oily and resinous substances are removed from the material. Hard and brittle fractions remain.
Naturally, this does not benefit the properties of the material. It loses plasticity and crumbles, especially when exposed to low temperatures.
Therefore, it is used as the bottom layer of the roofing carpet, or protected from ultraviolet radiation by sprinkles.
However, in areas where there are no sharp temperature changes, the use of oxidized bitumen is economically justified by its low cost, and the service life will be 15 years or more. This group includes, for example, Bikrost roofing material.
The second group, polymerized bitumen, differs in the polymers used. This:
- Isotactic polypropylene (IPP) is a plastomer, due to which mixtures based on it have the following properties: high density, tensile strength and melting point (up to 140 degrees), resistance to static punching. Frost resistance - up to -15 ° С. It has a high price, it is rarely used in the production of deposited materials
- Atactic polypropylene (APP) - a plastomer, a waste product of IPP, has the same properties, but to a lesser extent (melting point - 120 degrees), resistant to aging, provides excellent adhesion to any surface. Frost resistance - up to -15 ° С. It costs much less than IPP, one of the main additives in bitumen. Sometimes such mixtures are also called plastobitumens, or artificial plastics.
- Styrene-butadiene styrene (SBS) - an elastomer, gives the mixture increased elasticity and resistance to negative temperatures (frost resistance - up to -25 ° C), exactly repeats the surface structure. It has a lower melting point (90-100 degrees) than APP, a shorter aging period. Mixtures based on it are called bitumen rubber or artificial rubbers.
ADVICE! For roofs with complex terrain, it is better to use SBS-based materials, they provide a better fit. Also, homeowners from regions with low winter temperatures should pay attention to this class.
Along with impregnation, the most important component of the deposited material is the base. The quality of the coating and its service life also largely depend on it.
Now, for these purposes, as a rule, three canvases are used:
- fiberglass
- fiberglass
- Polyester
There are also "hybrids" - like polyester with fiberglass.
All polymer fabrics favorably differ from cardboard in their biological stability - they do not rot. However, there are differences between them in strength and other qualities.
Fiberglass is a material formed by a chaotic throw of fiberglass filaments, then fastened together with glue, or in another way.
Since waste can also be used in its production, it is the cheapest of the bases for roofing and other materials. However, it has a relatively low strength and a shorter service life compared to others.
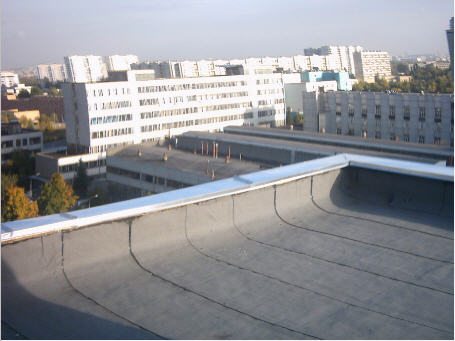
Fiberglass is a fabric made of fiberglass. It is 3-5 times stronger than fiberglass, proportionally and more expensive.
Polyester is the most expensive, but also the most practical of the bases.Differs in the increased durability and plasticity, besides - provides high-quality absorption and coupling with the impregnating mastic.
Protective covering
Upper layer roofing material needs protection, since the mastic itself is a rather soft material, moreover, it is at the “forefront” of the impact of all negative atmospheric factors. First of all, it is:
- Ultraviolet radiation
- Solar heating
- Precipitation
- Mechanical impact (tree branches, etc.)
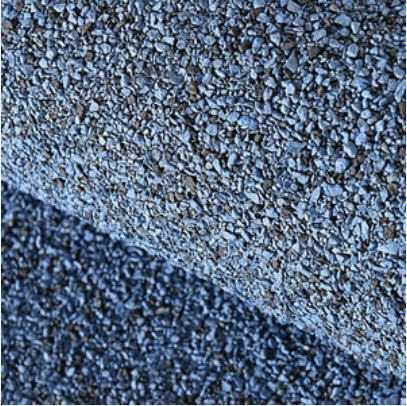
To minimize all these influences, various coatings of the top layer of the roofing material are used.
The most popular protection is various types of mineral dressings, applied even in the factory to hot mastic.
The dressing differs in the size of the fraction:
- Coarse-grained
- medium grain
- scaly
- fine-grained
- pulverized
The latter type is usually used to protect the back of the material from sticking, as well as for the double-sided coating of those modifications that are intended to make the first layer of the roofing carpet.
Slate, basalt, ceramic chips, sand are usually used as raw materials. Also, some types have a foil coating, or are covered with a polymer film (including on the reverse side).
The structure of the "pie"
Soft roofing, even from modern rolled materials, is usually performed in at least two layers. At the same time, they can be performed from various grades of material, depending on what requirements are imposed on each of the layers.
As a rule, the backing layer is distinguished by the absence of a protective coating on the upper side. It is also technologically allowed to use materials with lower strength in it, which reduces the total cost of the roof.
Also, other types of rolled material can be used in places of various joints and junctions.
What to pay attention to?
When choosing a suitable roll material, the main factors influencing the choice are:
- The complexity of the roof relief and its slope
- Temperature conditions of the region (in summer and winter)
- Average annual rainfall
- Roof serviceability
- Possible deformation loads (vibration, building shrinkage)
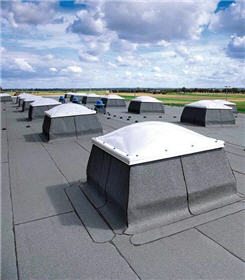
Based on this, the material should be selected, first of all, according to the required plasticity. This is, undoubtedly, the most important characteristic for a soft roof - provided that the necessary strength is observed.
If frost resistance is important, grades based on SBS fillers are better suited, for example, Bipol roofing material. They are both quite plastic and have increased frost resistance. The same class is best used on complex roofs.
Important information! At low temperatures bitumen loses plasticity. For each specific impregnating mixture, there is its own indicator in degrees below zero. The material becomes rigid, and, at the same time, shrinks under the influence of cold. If the loss of plasticity has reached a certain limit, the material does not withstand and cracks. Subsequently, these cracks lead to leaks inside the building and damage to the roofing carpet.
Also, in areas with a hot climate, the heat resistance of the material is also important.Under the influence of high temperature (and in some places it can reach 100 ° C on the roof), the top layer of mastic can float, forming spots that allow water to leak.
Also, on a roof with a slope of about 15%, it is also possible for the entire roofing carpet or part of it to slide along the slope. Here it is better to use various materials based on APP - they are more resistant to high temperatures, and have a high adhesion to the base material.
Getting Started
When the material is selected, it's time to proceed directly to its installation. Naturally, it is necessary to initially carry out the necessary measurements in order to imagine in advance in what order the work will be carried out.
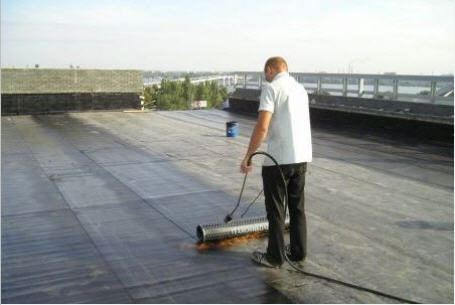
On flat and low-slope roofs, roll materials are laid along the roof slope, where the slope is about 15% - perpendicular to it, from the bottom edge to the top in both cases.
Important information! When laying, be aware of the standard dimensions of the overlaps. They are: with a roof slope of up to 5% - 100 mm in all layers, with large slopes - 70 mm in the lower layer and 100 mm in the upper one. This applies to both joining rows. So are the panels in a row.
Before starting work on the roof, all necessary equipment and material must be raised in an amount necessary to at least cover the planned area. In cold weather, the material must be stored in a warm room before laying.
Before laying, it is necessary to thoroughly clean the surface of the roof base, if laying is carried out on old layers of the coating, check them for exfoliated and weak areas. Such places should be cleaned mechanically.
If necessary, places of contamination must be degreased.Next, a primer is applied to the base with a brush or roller - a special bitumen-polymer mixture that provides better penetration of the molten mastic into the base material.
As a rule, gas burners operating on bottled propane-butane are used to fasten the welded rolled materials (during the preparation of work, a bottle and a hose with a length of at least 10 m are also raised to the roof).
Diesel burners are less commonly used. The team of roofers, as a rule, consists of 3 people.
In the course of work, one of them brings new material, the second works with the burner, and the third levels the laid coating and smoothes its edges with a special comb or roller.
7-10 rolls of material are laid out hardly, taking into account overlaps, and rolled out to the full length for fitting, if necessary, the material is cut in the right places.
After that, the edges of the sheets are glued with a burner, and all rolls are rolled up to the place of gluing. Laying begins with the lowest overlapping panel.
At the same time, the burner is positioned in such a way as to evenly heat the entire width of the web and, at the same time, heat the base. The stacker can roll out "from itself", or "on itself", while using a stroke or a special roller.
If a roller of molten mastic is formed along the edges of the canvas, it means that the work is carried out too slowly, the material overheats and loses some of its protective properties. A too fast pace is indicated by the backlog of the laid material.
Behind the installer is a second worker who rolls or presses the sheet, preventing the formation of bubbles on the surface of the roof, as well as loose edges.
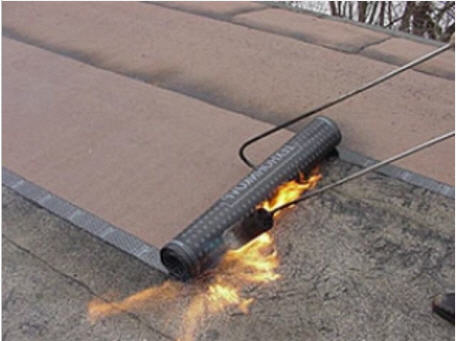
If necessary, individual sections of the canvas can be heated and rolled again.
In cramped places, a hand torch should be used, and rolling or smoothing should be done with special mini-rollers. No bubbles or wrinkles should form in any areas of the roofing carpet.
Pipes are brought out through the surface of the material using embedded pipes with reinforced concrete flanges.
At the same time, the roofing carpet is placed on the branch pipe itself, and the junction is carefully isolated with a special mastic for the roof. Do the same with other protruding parts on the roof.
Vertical sections are laid in the direction from top to bottom with pieces of canvas located along the height of the structural element.
In this case, the ends of these pieces are wound onto the main coating layer. To protect the edges of the carpet on the parapets, protective tin aprons are equipped on top, and the canvas is wound under them.
ADVICE! In places where pipes pass in a strip of material, it is better to make a break. This will greatly facilitate the work of making a hole and laying, ensuring greater accuracy and quality of embedding.
Repair work
In the event of leaks, damage to the roofing carpet, violation of the tightness of the joints, it may be necessary to repair the roof from welded materials. In this case, two solutions are possible, the choice of one of them depends on the specific situation.
If the roof is relatively new, and the damage is not very significant, it is necessary to examine the area around it to determine where the carpet has peeled off, the presence of moisture under it, and other problems. Before repair, the coating is removed on the entire damaged area + at least 100 mm from its edges on normal material.
The entire bare surface is cleaned mechanically, if necessary, degreased. After that, pieces of material of the desired shape are cut out with a spade of 100 mm on the old material on each side. Further, the material is laid in the usual way.
If the damage is significant, you can use liquid mastics, otherwise called self-leveling roofing.
At the same time, the preparatory work is carried out the same, with cleaning and degreasing. Further, by the method indicated in the instructions for use, mastic is applied, also with a 100 mm approach to the main part of the old coating.
ADVICE! In order to avoid the need for repairs for a longer time, preventive roof inspections should be carried out twice a year (after the snow melts and in the fall, before it falls).
Despite the fact that many new, promising technologies have appeared, welded roofing materials will obviously be in service for more than a dozen years.
They are used not only as a finished roof. But also as waterproofing for other types of roofs. Other structural elements.
Therefore, it is worth knowing the technology of their production and installation, classification and repair methods for everyone who is related to roofing - professionally, or in their own home.
Did the article help you?