The production of metal tiles is a rather complex and multi-stage process, and its subtleties are clear only to specialists. However, to get at least a general idea of how metal tiles are made is necessary for everyone who plans to work with this roofing material.
After all, only by understanding what technological operations are performed in the manufacture of metal tiles, we can fully use all its advantages.
Technological chain of production of metal tiles
The technology by which the production of metal tiles takes place has remained unchanged for quite a long time - after all, in the process of its formation, it has been repeatedly adjusted and improved by foreign manufacturing companies.
The only stage in which changes are constantly made is the stage of applying a protective polymer coating.
This is due to the fact that new types of technological polymers appear regularly, and along with changing materials, the properties of metal tiles also change - the production of relatively simple roofing materials is modernly replaced by the production of high-tech modern tiles.
In its most general form, the technological chain for the production of metal tiles includes the following steps:
- Rolled metal base (galvanized steel sheet)
- Passivation (application of protective coatings)
- Protective polymer application
- Profiling
- Cutting and packaging
For different types of equipment, the sequence of these stages may be different, but they have the same result: at the output, we get a sheet of metal tiles cut “to size”, which is a multilayer “pie” based on stainless galvanized steel, only metal tile colors and I will be different.
The video shows the production process of the most popular roofing material on an automatic lines for metal tiles Monterrey, starting with a coiled metal decoiler, then - the perfect stamping of steps on a rolling mill, the operation of shears for cutting metal (and 3D shears) and at the end - a store of finished sheets - a receiving table.
Next, we will consider the main stages that the blank goes through the line for the production of metal tiles.
Metals for metal tiles
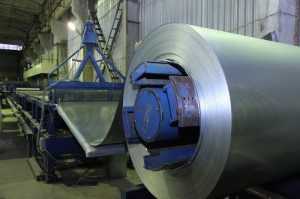
The raw material for the production of metal tiles is cold-rolled hot-dip galvanized steel coil.
The roll of steel is installed in a special decoiler, which passes the steel through a lubricator and feeds it to the rolling mill.
An important factor at this stage is not only the quality, but also the thickness of the metal.
It is important that the coiled steel has the most even and smooth surface, since any surface defects adversely affect the reliability of fastening based on passivation and polymer layers.
As for the thickness of the metal, the equipment for the production of metal tiles from most manufacturers is focused on working with a workpiece with a thickness of 0.45 to 0.55 mm.
And here there are several nuances:
- Swedish metal tile companies tend to use the thinnest metal, 0.4mm. On the one hand, the resulting metal tile has a smaller mass, but on the other hand, it requires significant accuracy during installation. For this reason, some construction companies consider Swedish metal tiles to be non-standard and refuse to use them.
- Unlike the Swedes, domestic manufacturers of metal tiles prefer to work with a thicker base, however, starting from a thickness of 0.55 mm, steel is rather difficult to form, so a specialized line for the production of metal tiles should be used for it. In addition, metal tiles on a thick base will inevitably have deviations in configuration, which will necessarily affect the quality of the joints.
- The use of a base of 0.5 mm can be considered optimal.On the one hand, such a metal tile is molded quite easily, on the other hand, it has the necessary margin of safety. The technology for manufacturing metal tiles on a steel base with a thickness of 0.5 mm is widely used by Finnish companies.
Steel used for metal tile manufacturers, is sequentially subjected to longitudinal rolling.
As a result, we get a tape with a characteristic profile, which, in order to become a full-fledged metal tile, lacks protective coatings and final molding.
Metal tile coatings
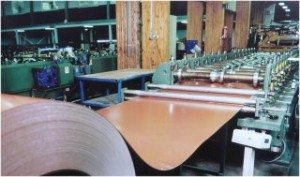
Protective coatings of metal tiles, ranging from a passivating layer to a varnish covering the polymer, are designed to prevent the development of corrosion on a steel base.
Besides, these coverings give to a metal tile esthetic appearance and protect it from fading under the influence of an ultraviolet. As a rule, the service life of a metal tile roof depends on the quality of the protective coating.
Most often, the metal tile production line is designed in such a way that polymer coatings are applied automatically according to the following scheme:
- Passivation
- Primer
- polymer coating
- Protective varnish
Note! As a rule, a metal tile is covered with a polymer composition only from the top side, and only a colorless protective coating is applied from below.
As a polymer coating can be used:
- Polyester - layer thickness up to 25 microns, high wear resistance, high resistance to temperature extremes. The main advantage of polyester is that it is not damaged during molding, so sheets with an already applied coating can be fed to profile stamping.In addition, polyester is one of the cheapest coatings.
- Pural - coating thickness for roofs made of metal 50 µm, pleasant silky-matt surface structure. A thicker coating is less resistant to molding, but provides higher resistance to external factors.
- Plastisol - layer thickness 200 microns, wide range of colors and maximum resistance to mechanical and thermal influences. However, shingles coated with dark-colored plastisol get very hot under the rays of the sun and therefore actively fade.
After applying protective coatings, the metal tile enters the molding mechanism, where it is given the appropriate profile. After profiling, the metal tile is cut to size and packed.
As you can see, there is a rather complex and multi-stage production - the metal tile undergoes many technological operations designed to give it high performance properties.
But the result is an excellent roofing material, which is a pleasure to work with!
Did the article help you?