Soft welded roofing is an ideal solution for roofs with minimal slopes. The only disadvantage of this option is the high installation requirements, any errors lead to leaks. To rule out problems, read the information below and follow all steps in the installation instructions.
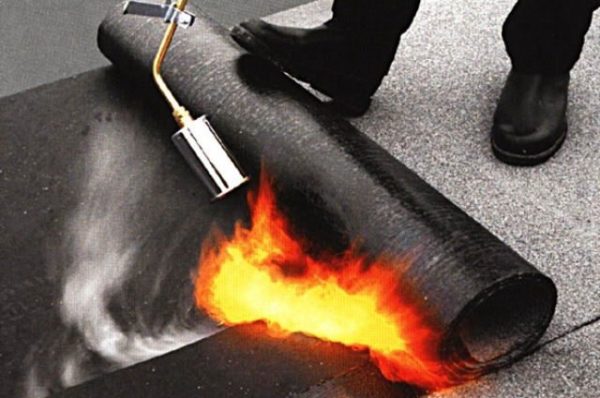
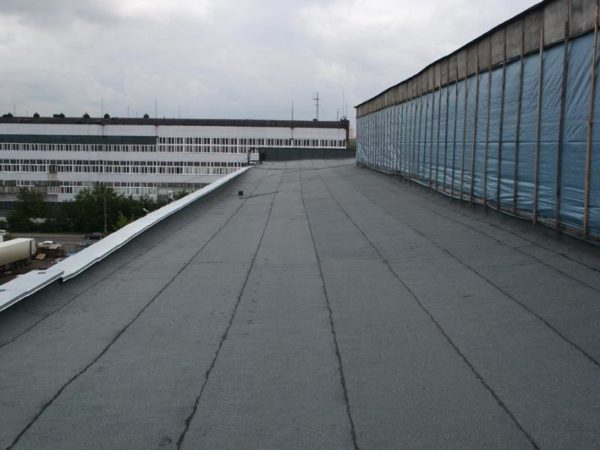
Workflow steps
The technology of soft roofing made of welded materials is complicated only at first glance. If you break all the actions into separate stages and deal with each of them in detail, then no difficulties will arise. The main conditions for a good result are accuracy and the use of quality materials.
The work consists of the following stages:
- Collection of necessary materials and tools;
- Foundation preparation;
- Laying vapor barrier material and surface insulation;
- The device of a cement-sand screed;
- Primer application;
- Roofing material.
If you are repairing the roof, and it was insulated earlier, then you can skip the vapor barrier, insulation and pouring the screed. We'll walk you through the entire process from start to finish.
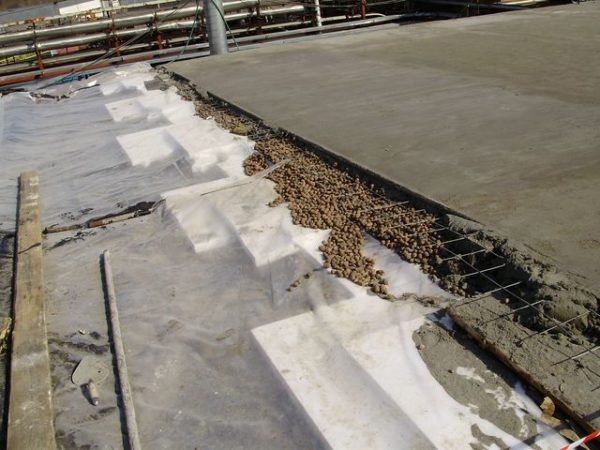
Stage 1 - purchase everything you need
First of all, let's deal with the materials, the entire list is indicated in the table.
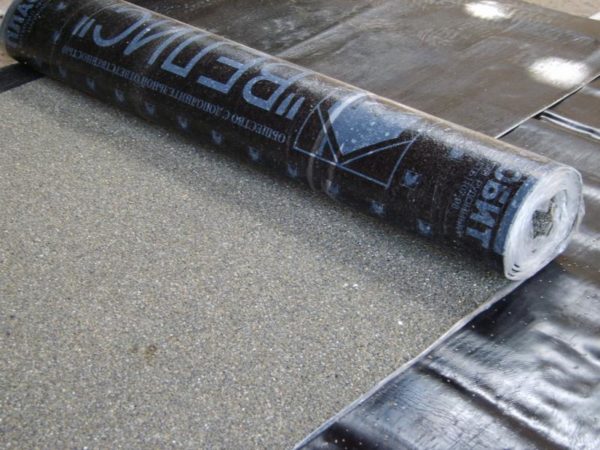
Material | Description |
Roll roofing | The built-up roofing material is on sale in rolls 1 meter wide and 10 meters long. There is a bottom layer and an upper one, you need to use both options, do not try to save money. There are many manufacturers on the market, I use Technoelast material, the price of the lower layer is 1100 rubles per roll, and the top layer is 1900 rubles |
Vapor barrier material | There are many options, choose those that fit under the screed and have a large thickness. When buying, always take it with a margin, because at the joints you need to make laps of 15 cm. A roll of 70-75 square meters will cost 700-800 rubles |
insulation | You need to use either extruded polystyrene foam or high-density mineral wool. Personally, I prefer the first option, as it is much stronger, not afraid of moisture and has high thermal insulation characteristics.
"Penoplex" 5 cm thick is sold in packs of 8 pieces, which cost about 1,500 rubles. Packed 5.76 square meters |
Screed mortar | The easiest way is to buy a ready-made M150 mixture in bags and simply dilute it with water. This will simplify and speed up the workflow. But you can prepare the solution yourself, then you need to purchase sand and cement |
primer | With this composition, the base is processed before gluing the waterproofing material. The primer closes the pores in the screed and improves the adhesion of the roofing. Sold in buckets of 20 liters and costs about 1600 rubles |
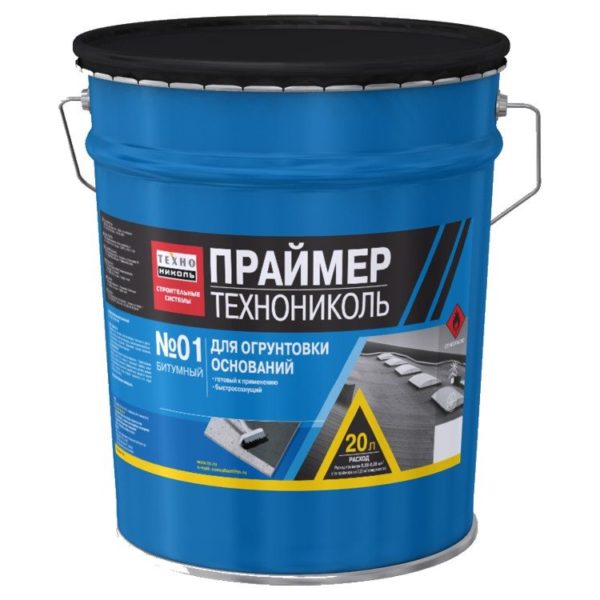
When installing a soft roof, you need to use the following tool:
- To level the surface, you may need a puncher and a grinder;
- A level and a rule are used to control the plane;
- The solution is best prepared with a concrete mixer, since its volumes will be large;
- The primer is applied with a wide brush or roller;
- The roof is heated by a gas burner, you don’t need to buy it, it’s easier to rent it.
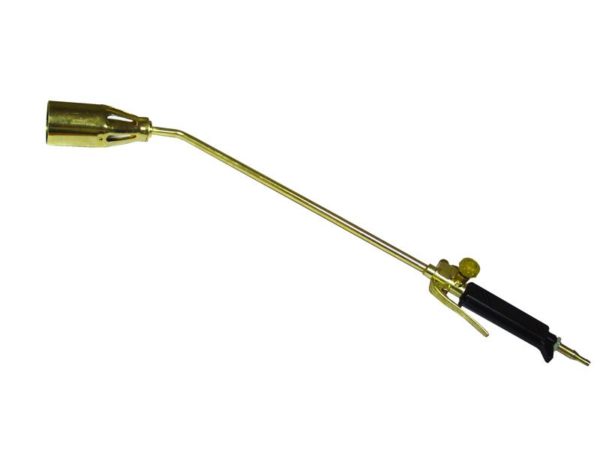
Before starting work, I advise you to look at the roofing pie diagram shown below. It will give you an idea of what the end result will look like. That is what we will be working on.
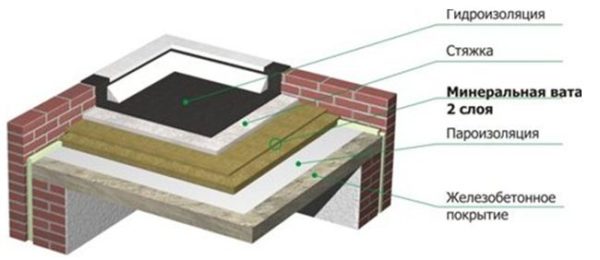
Stage 2 - preparation of the base
The device of the built-up roof begins with the preparation of the surface, this part of the work consists of the following steps:
- First of all, you need to remove the old coating, if any. Sometimes you can leave the roll roofing, but only if the surface is whole and even. Most often, old materials are damaged, and when removed under them, a lot of problems are found;
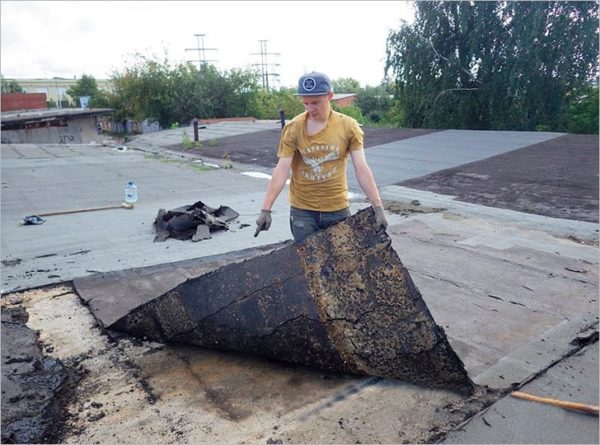
- After removal, most often a damaged screed and half-decayed insulation or crumbling expanded clay are found. This also needs to be removed, since it is impossible to make a solid surface on a dilapidated base. All cracked areas are removed without fail;
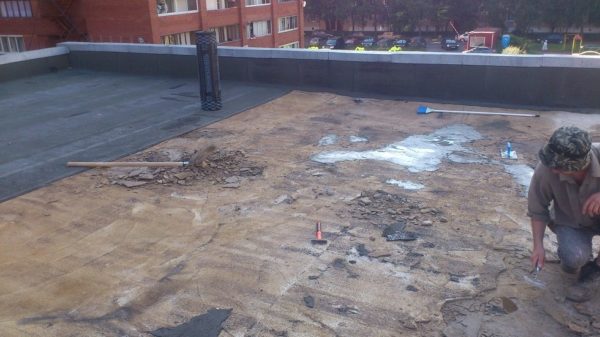
- If you have a new building, then most likely there will be wide seams between the plates. They need to be sealed with a cement-sand mortar, for reliability, reinforcement 6 or more millimeters thick can be laid into the joints. The solution is applied so as to fill the entire void, the plane is leveled from above with a spatula, all excess is removed. The result should be a flat surface;
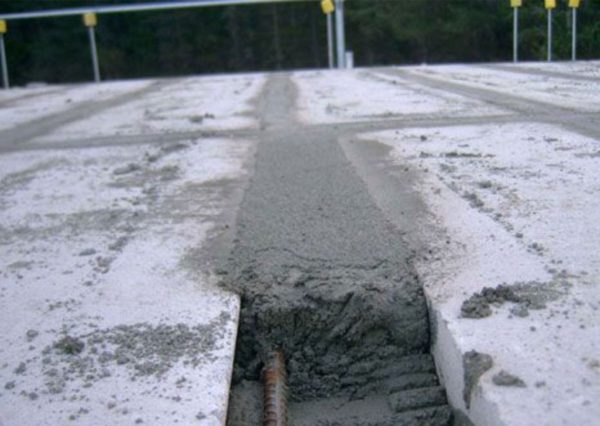
- If there are protruding reinforcement, mortar sagging and other protruding irregularities on the surface, then they should be removed. Concrete and mortar are removed with a perforator with a chisel, and metal elements are cut with a grinder. The plane should be as even as possible, the protruding sections should not exceed a few millimeters. It is best to check the surface with a long level.
- If there are many small irregularities or cracks in the concrete, it is better to repair them as well. For work, you can use special compositions to strengthen the surface. They are applied to the desired areas, after which the surface is leveled with a spatula.
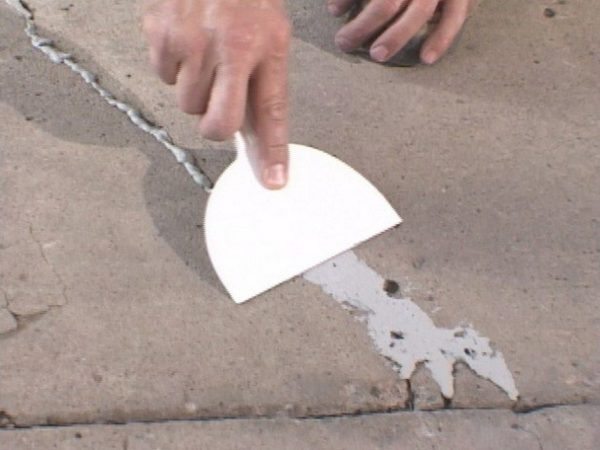
Stage 3 - vapor barrier and surface insulation
Now let's figure out how to insulate the surface. Most often, it is required to lay a layer with a thickness of 10 mm, if there is no such material, then two layers of 5 cm can be laid.
The work looks like this:
- First of all, a vapor barrier is laid on the surface. The material is laid so that it extends 10 cm onto vertical surfaces. The strips overlap each other by at least 15 cm. To ensure additional reliability, the joints are glued with adhesive tape;
The vapor barrier film has an outer and inner side, and it is important not to confuse them when laying. The roll always indicates how the material should be positioned, do not miss this important point.
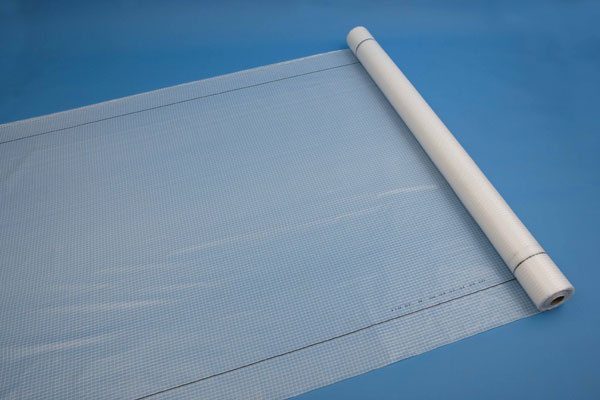
- Installing insulation is a fairly simple process. You need to cover the surface with material and join all the sheets as tightly as possible. It is best to start from one of the sides and work in order so that all the elements fit together perfectly;
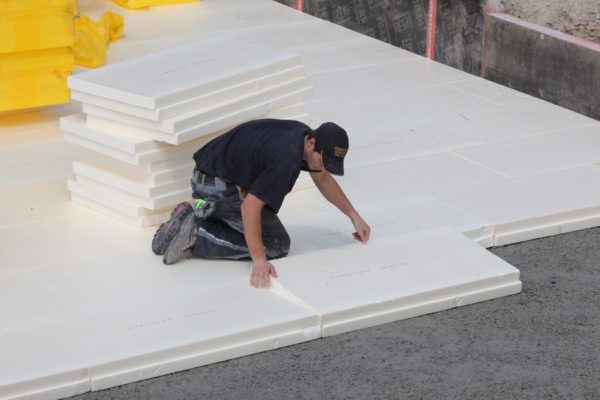
- If the material is laid in two layers, it is important that the sheets are laid with an offset. Moreover, it is best if neither the longitudinal nor the transverse seams match. An approximate laying scheme is shown below, this option provides the best reliability of insulation;
- The finished surface should be even, if somewhere the corners of the sheets stick out, then it is easiest to carefully cut them off.
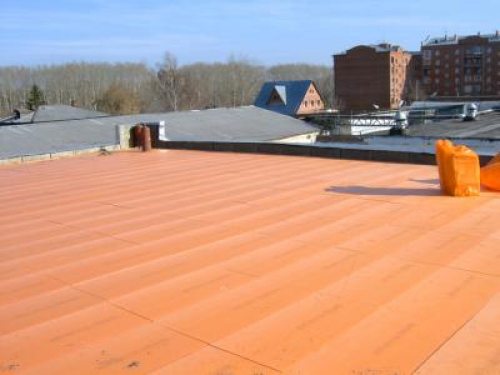
Stage 4 - pouring the screed
A very important part of the work, as we will form slopes to the drain, and strengthen the base.
The do-it-yourself process looks like this:
- First of all, you need to set up beacons to form the future roof plane.. The thickness of the screed can be from 3 to 10 cm, it is better not to put a very thick layer, so as not to create a load on the floor. Lighthouses are set so that the slope goes to the drain point, large height differences are not needed, 3 degrees is enough. For work, either metal elements or wooden slats are used;
- Sometimes a mesh is placed on the surface for reinforcement, it all depends on the area and loads. If you use the services of an automixer, the solution will be supplied to the roof through a hose, and you will have to distribute it over the surface. Usually 1-2 people work with shovels and a rule, and one rearranges the hose to the required place;
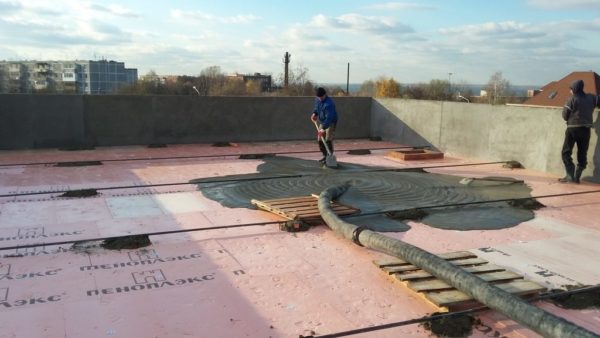
- If the solution is supplied manually, then it is better to place the concrete mixer in the corner of the roof so as not to carry heavy buckets. The mass is distributed section by section, so it will be easier for you to level the plane. You can level the surface both with a special rule and with a flat rail;
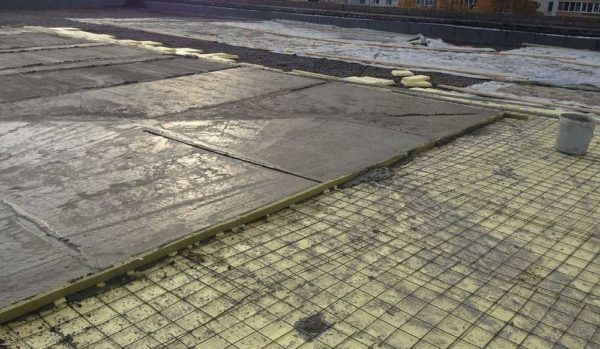
- If you used wooden slats as beacons, then expansion joints are not needed. If metal beacons were used, then it is necessary to cut seams with a depth of 30-40 mm every 5-6 meters;
- The surface must be completely dry, it takes about 2-3 weeks. During precipitation, it is advisable to cover the roof with a film.
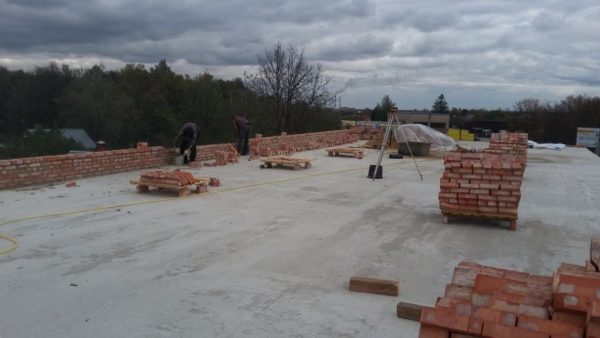
Step 5 - primer application
After the screed has dried, you can start applying the primer. This composition allows you to create an ideal basis for rolled materials, therefore, without such processing, it is impossible to glue the roof.
The workflow is quite simple:
It is important to apply the primer on a dry base. If you do not have a moisture meter to measure humidity, then you can use the popular method. Place a meter by meter piece of film on the surface, press it down and leave for 4-6 hours. If during this time moisture has not accumulated on the oilcloth, then the surface has dried.
- First of all, you need to stir the primer very well. You can do this with any stick, it is important to lift all the settled components from the bottom so that the mass is homogeneous. If you have a concentrated version, then before use it must be diluted with the composition recommended by the manufacturer on the label;
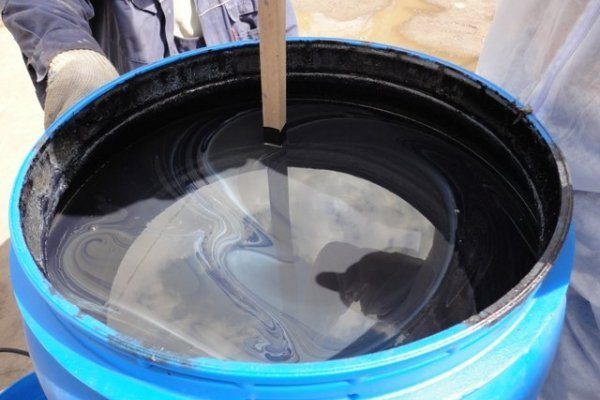
- The easiest way to work is with a roller, it is dipped into the composition and distributed over the screed in a thick even layer. If the treatment area is large, then it is better to make an extension handle for the roller so that you can work standing up and not strain your back. It is important to process the entire area and not miss a single section;
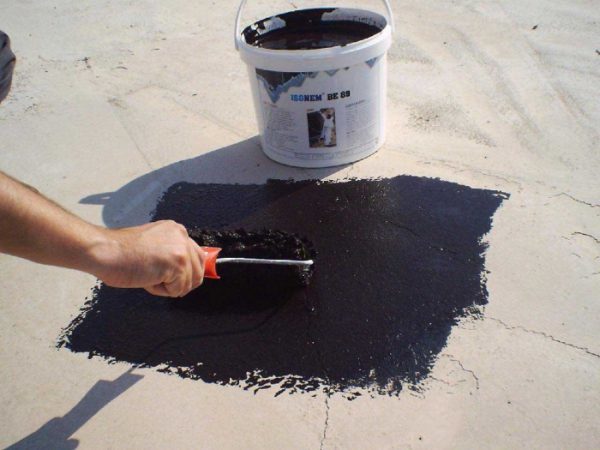

Do not try to save money and cook mastic yourself from gasoline and bitumen. Firstly, this activity is not safe, because you have to lift buckets of boiling resin to the roof and apply the composition also hot. Secondly, such a coating can dry for weeks.
- At an air temperature of 15 to 30 degrees, the surface dries for about a day, sometimes a little more. You need to wait until it is completely dry, as you will need to walk on the roof during work.
Stage 6 - installation of roofing
The built-up roof is glued to the roof according to the following algorithm:
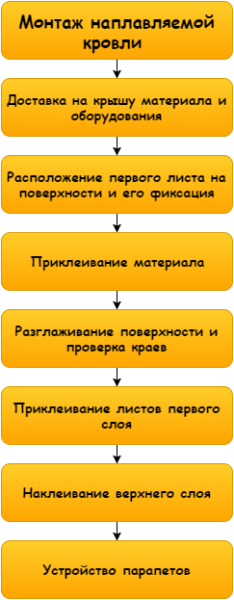
- To begin with, you should bring a gas cylinder with a burner and roofing materials to the roof. If you think it's easy, then it's not. The weight of the welded roll roofing of the lower layer is 40 kilograms, and the upper layer is 50 kilograms. Therefore, it is better to call assistants so as not to leave all the forces already on this part of the work;
- The process of laying the material begins from the lowest section. The roll is spread perpendicular to the direction of water movement. Its position is checked and integrity is checked. If everything is fine, then the edge of the canvas is heated by a burner and glued to the surface. After that, the material is twisted back into a roll.;
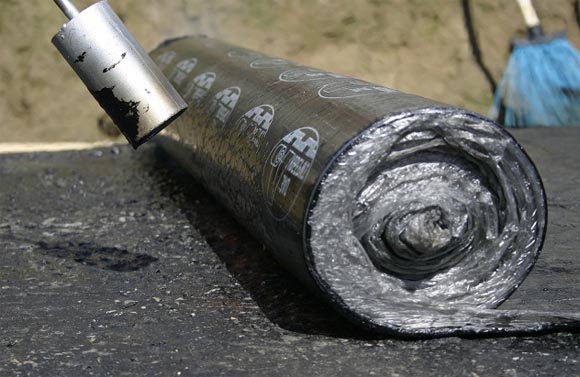
When working with the burner, you must follow the safety rules. Still, this is an open fire and gas, so be careful.
- The material is glued as follows: the lower part of the material is heated with a burner so that it becomes soft, after which the piece is glued. As the work progresses, the roll gradually unwinds, and as a result, you get a securely fixed material. It is important to properly heat the roof, the bitumen should turn out soft, but not drain from the base, if fibers are visible, it means that the surface is overheated;
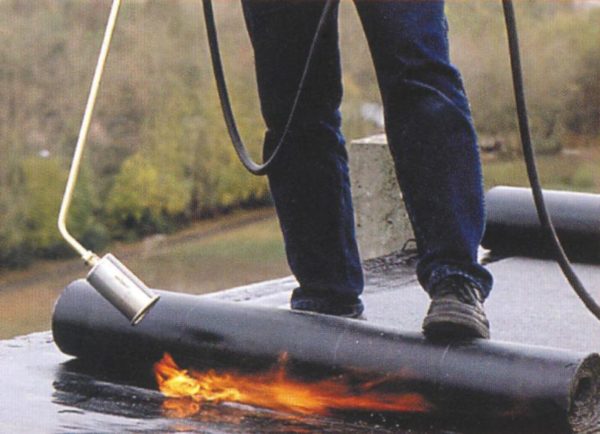
- It is impossible to walk on the material until it has cooled down, the surface is leveled with a roller in the direction from the middle to the edges. You need to smooth the material and press it while it is still hot and sticks well to the base. Pay special attention to the edges, if somewhere they stick poorly, then the material is lifted with a spatula, warmed up and glued again;
- The next roll is placed with an overlap of 8 cm on the previous one. There is a strip along the edges that is easy to navigate. The sheet is glued in the same way as the previous one, if everything is done correctly, then a roller of bitumen about 1 cm wide is formed along the edges when pressed.. Naturally, special attention is paid to the joints. So work continues until the entire roof is pasted over;
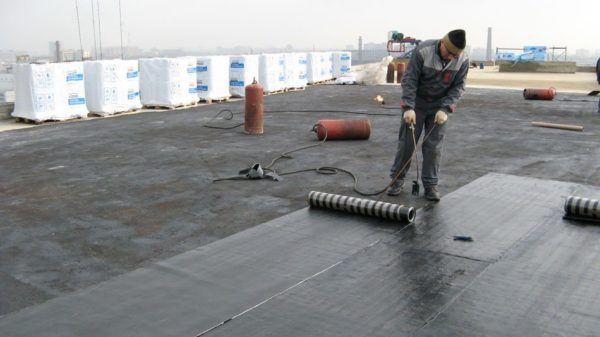
If the roof is flat or the slope is very small, then it is recommended to lay the two lower layers of roofing material. This provides additional reliability. It is important to remember one thing here: the sheets are offset with an offset so that the joints do not match.
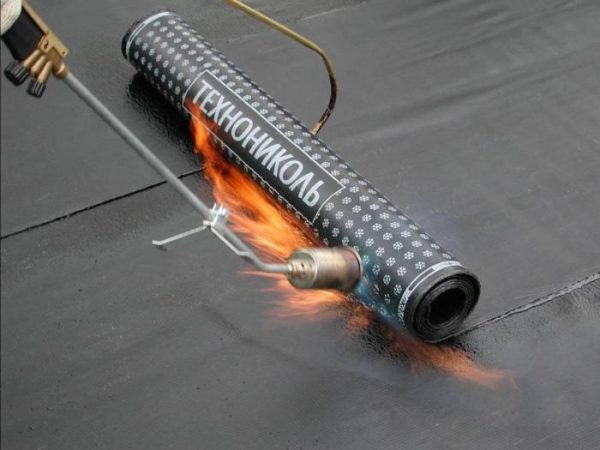
- The top layer has a topping on the surface, it protects the roof from damage and from destruction by the sun. The first sheet is also placed in the lowest place, but do not forget about the offset of the seams, it must be at least 15 cm. The edge is glued, after which the roll is folded back and glued in the same way as the bottom layer, it is important not to overheat the material and observe the dimensions of the joints ;
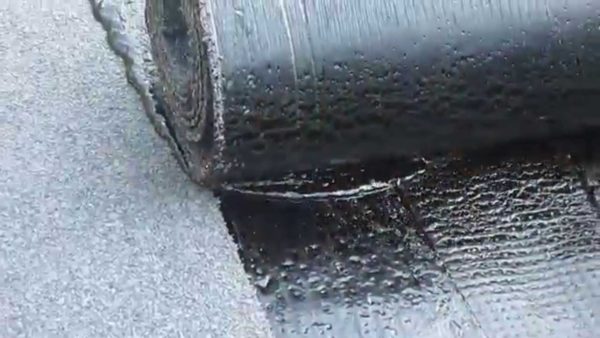
If the overlap at the longitudinal joints is 8-10 cm, then when connecting the end sides, an overlap of at least 150 mm must be made.
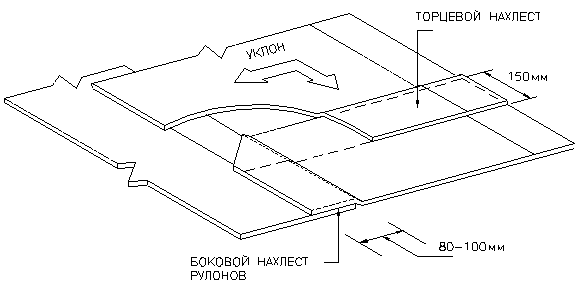
- Pay special attention to the joints, they are carefully rolled with a roller so that there are not even the slightest voids.An indicator of good fastening is a protruding edge bitumen. If problems arise, the edge is bent, warmed up and glued again;
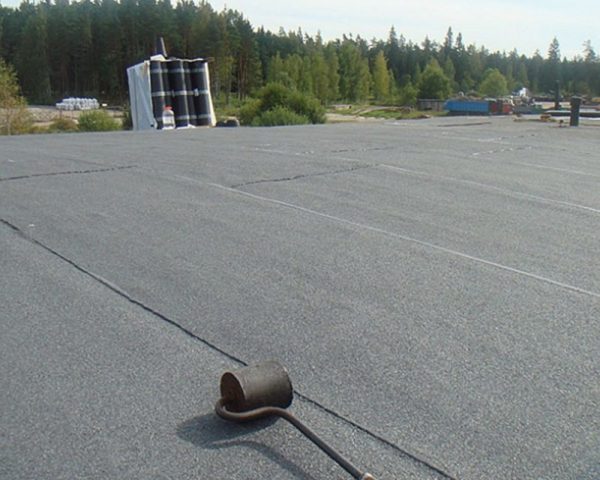
- Work continues until the surface is completely covered, it is important to place the sheets evenly and warm them well for perfect adhesion;
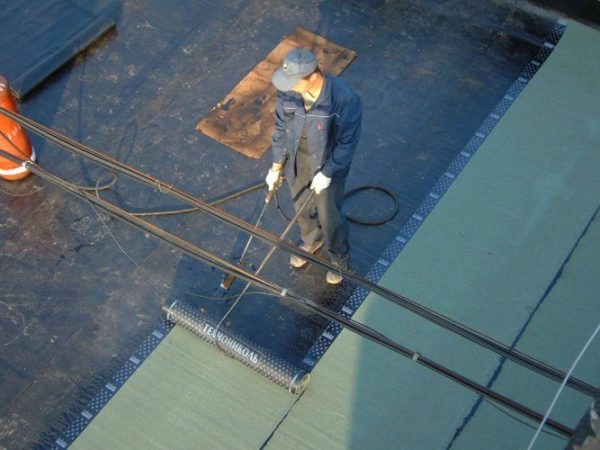
- Now let's deal with the parapet, first a piece of the bottom layer is taken of such a size that it goes 20 cm onto a vertical surface and 25 cm onto a horizontal one. The piece warms up well and sticks. The top layer should go to the vertical by 35 cm, the edge is fastened with a rail, and the rest is glued as usual.
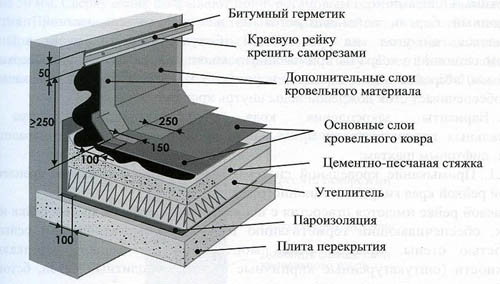
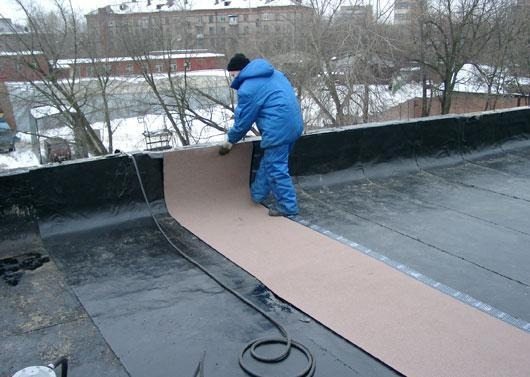
Conclusion
After reading this review, you could be convinced that the built-up roof can be laid on your own. The main thing is to carefully observe the technology and securely glue the sheets. The video in this article will help you understand the topic even better. And if you have questions about the workflow, then write them in the comments under the review.
Did the article help you?