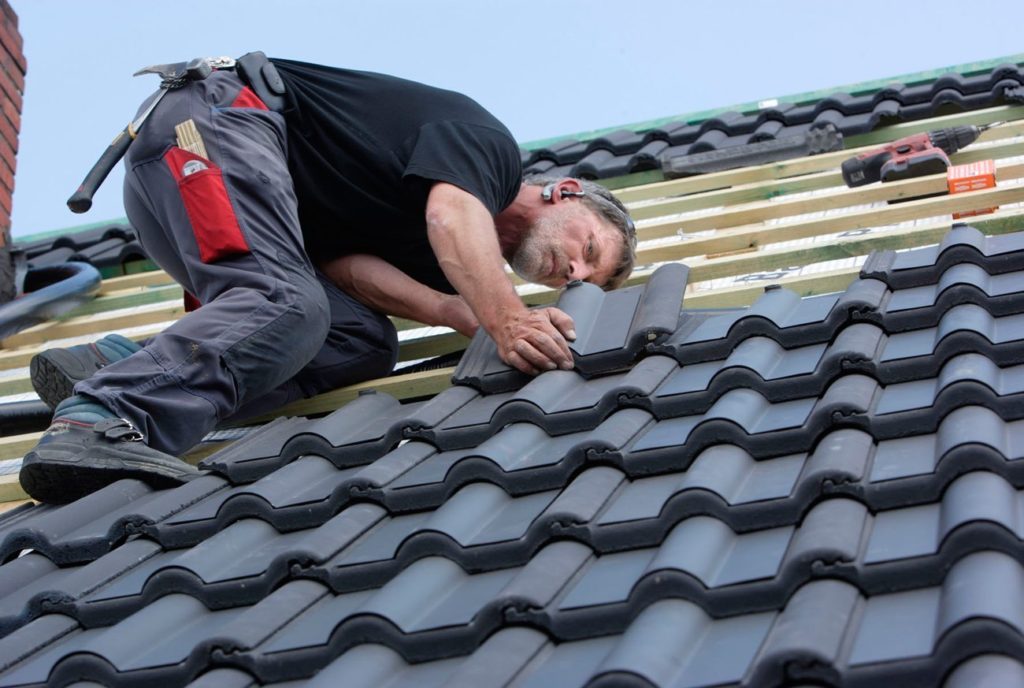
Natural ceramic tiles have long passed into the category of retro materials and a kind of "exotic". But does this mean that it should be completely abandoned in favor of ondulin, metal tiles, bituminous roofing, etc.? Of course not - all the more so it is quite possible to learn how to mount a tiled roof on your own. And if you master this technique, then the result will be quite worthy - both in terms of aesthetics, and in terms of reliability, durability and functionality.
Tiles as roofing material: pros and cons
Features of the production process
Along with thatched and reed roofing, ceramic tiles are one of the oldest roofing materials. So we can safely say that its reliability is confirmed for one thousand years. And although modern products are quite different from the tiles of the times of Ancient Rome, they have quite enough common features.
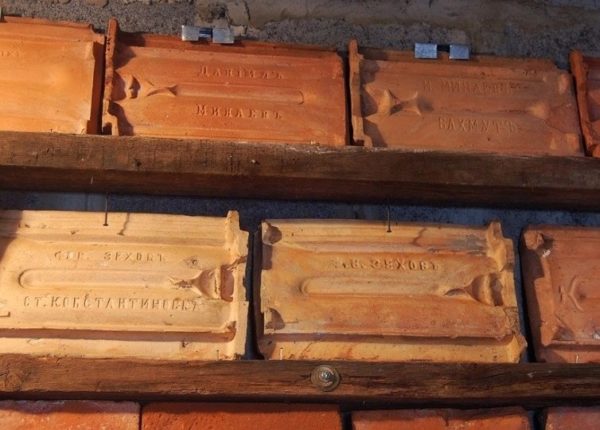
The technology for the production of tiles is relatively simple:
- Raw material. The basis of the material is clay, or rather, a mixture of different clays with high plasticity. To improve the mechanical characteristics, sand and mineral fillers, as well as plasticizers, are added to the clay. In the production of colored tiles, mineral dyes are introduced into the composition of the material.
- Molding. Separate elements of a tiled roof are formed from the clay mass by machine stamping. When stamping, the clay is compacted, which makes it possible to remove air from the tile and increase its strength.
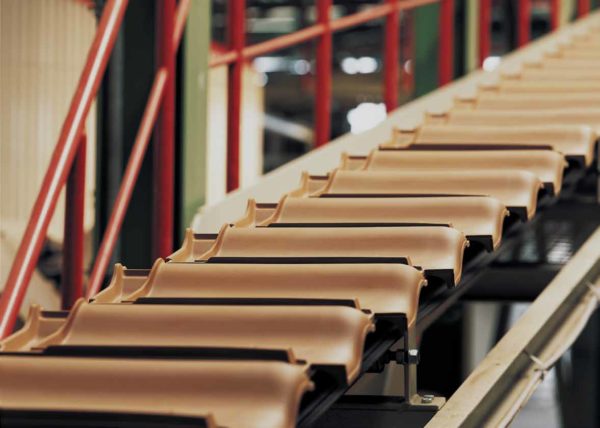
- Drying and roasting. The stamped parts are first air-dried and then fired in ovens at a temperature of 1000 °C. In this case, ceramization of clay occurs.
- Finishing. Ordinary tiles after firing and cooling can be immediately put into operation. If it is necessary to increase the moisture resistance of the material or improve the decorative qualities, then engobing or glazing is performed. At the same time, the front surfaces of the parts are coated with compounds that are resistant to external influences.
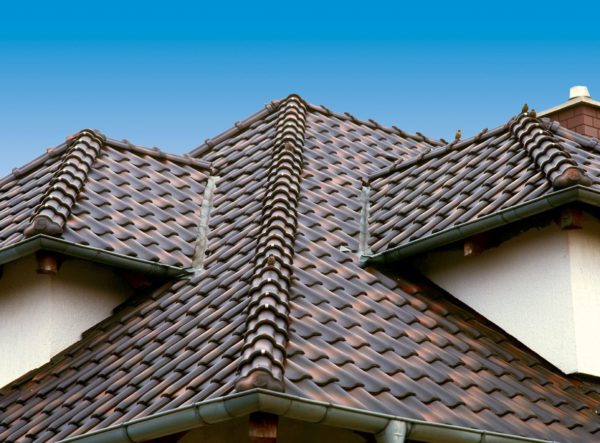
The result is a piece roofing material with a shape that facilitates installation and good performance.
Advantages of ceramic roofing
Natural tiles are quite suitable for covering the roofs of residential buildings, outbuildings and some public buildings. This is due to its advantages:
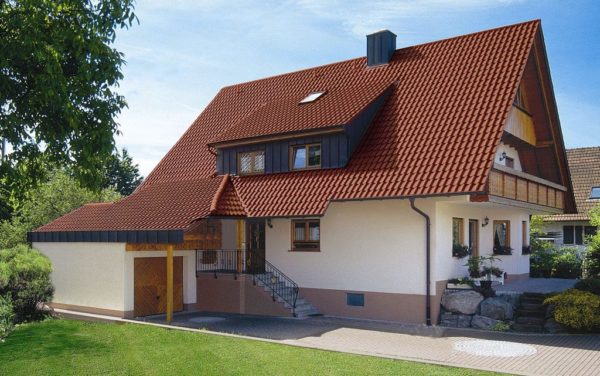
- Beautiful appearance. If even 50 years ago tiles were chosen for other qualities, today design considerations come out on top. A roof made of this material looks very stylish, especially since both classic color options (shades of red and brown) and color models are available on the market.
It is very important that the roofing material is in harmony with the rest of the finish and with the overall exterior of the building. Still, ceramic tiles are almost always antique styling, and it is quite difficult to combine it with modern architectural elements.
- Resilience and durability. Fired clay is durable, low moisture capacity and almost absolute chemical inertness. As a result, a roof made of this material can last more than 100 years.
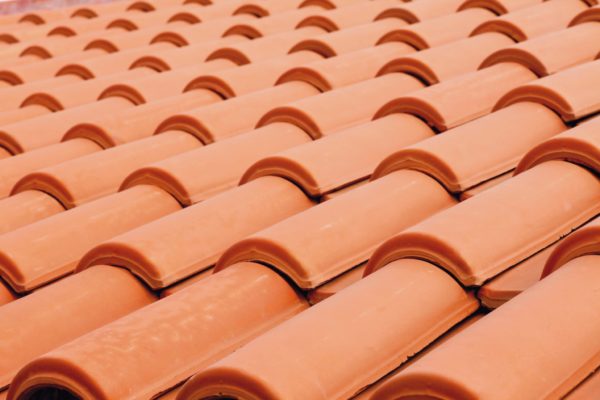
- Heat and sound insulation. The tiled roof is quite thick and heterogeneous. This provides both a decrease in the thermal conductivity of the coating, and a decrease in the volume of external sounds.
- Environmental friendliness. For the production of ceramic tiles, almost exclusively natural raw materials are used. Thanks to this, the roof does not emit toxic substances and is rightly considered completely safe.
- Fire resistance. Ceramic clay can withstand temperatures up to 1000 degrees. This is a residually effective protection of the roof and under-roof structures from ignition during lightning strikes, sparks, falling burning branches, etc.
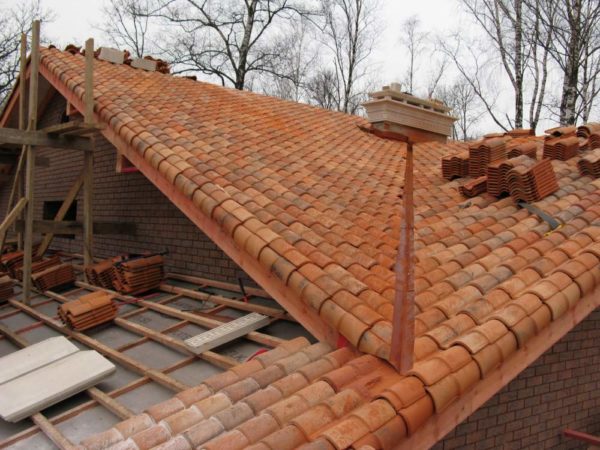
From personal experience, I can also add that the advantage of this material is in the small size of individual parts. With proper skill, tiles can be used to cover almost any shape of roof, and there will be relatively little waste.
Flaws that need attention
Alas, among other roofing materials, tiles cannot claim leadership. This is explained by a number of shortcomings:
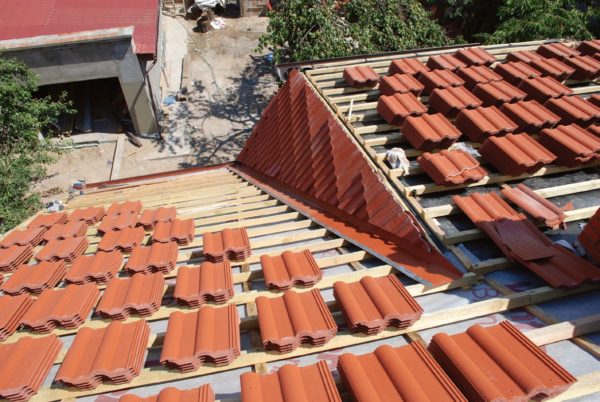
- Big weight. The specific load from ceramic tiles can reach 50–55 kg/m2. Accordingly, both the supporting structures and the truss system must be made with a margin of safety, which leads to their rise in price.
Installation of ceramic tiles on roof slopes of 60° or more is carried out only with the use of reinforced fasteners. This prevents the material from slipping under its own weight.
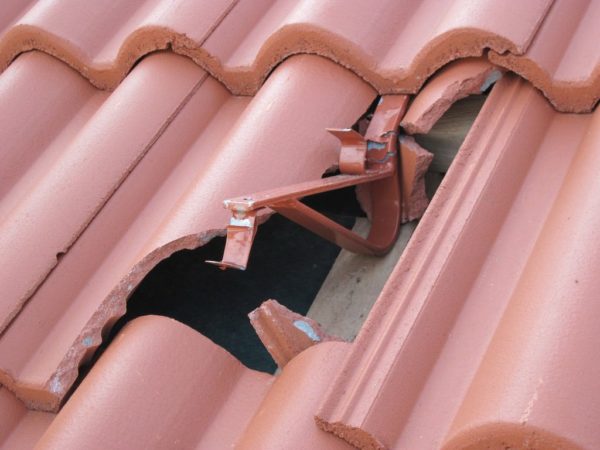
- Fragility. Good compressive strength of the material is accompanied by low impact resistance. As a result, with point impacts (during loading, installation or operation), the tile easily cracks.
- High price. The average price of ordinary material starts from about 800-1000 rubles per square meter. In addition, for the installation of the roof, additional elements are needed (skates, ridge and cornice strips, valleys, etc.), which rarely cost less than 150-200 rubles per piece.
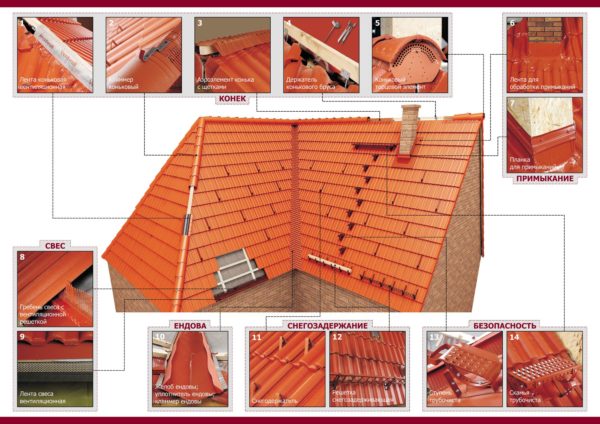
- Complicated installation. Making a tiled roof with your own hands is both difficult and expensive. Articles and videos give only a general idea of the technology, so it is better to master the technique in practice.Ideally, under the guidance of an experienced roofer.
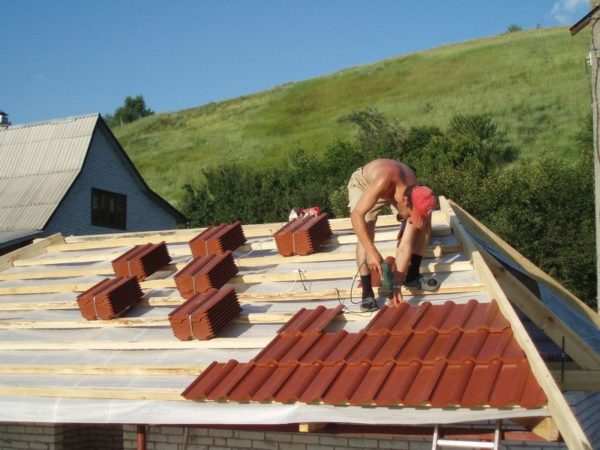
- Low tightness. The optimal roof slope for laying ceramic tiles starts from 22°. If you lay the material on a more gentle slope, then leaks will be inevitable. In principle, you can deal with this with the help of underlayment thermal insulation, but it is better to simply use more suitable products.
As a result, I can say that ceramic tiles, to put it mildly, are far from universal. Everything rests mainly on finances: if money is “back to back”, then it is better to choose another option. If the budget allows, and the tiled roof fits into design buildings, you can slightly reduce costs by self-assembly.
Roofing
Materials and tools
Ceramic roofing is a fairly complex structure that must be assembled according to all the rules. For its device, we need the following materials:
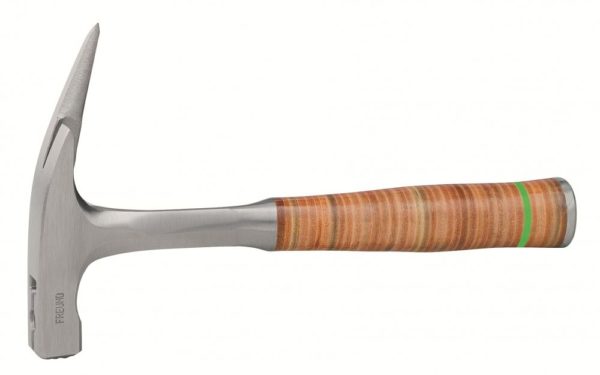
You will also need a set of tools:
- roofing hammers;
- electric saw with a disk for cutting ceramics;
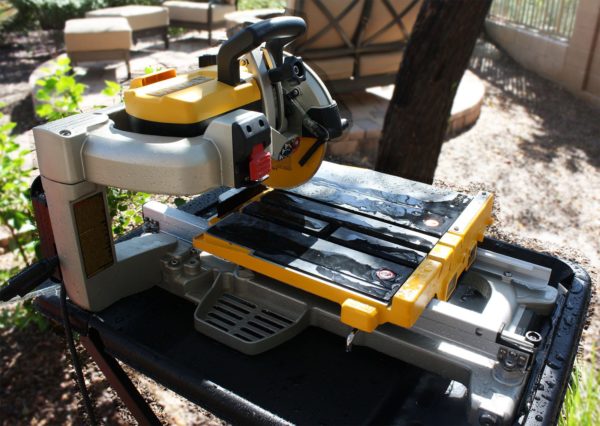
- tile pliers of several sizes for fitting parts;
- screwdriver;
- level;
- roulette;
- plumb;
- measuring cord;
- construction stapler for attaching waterproofing.
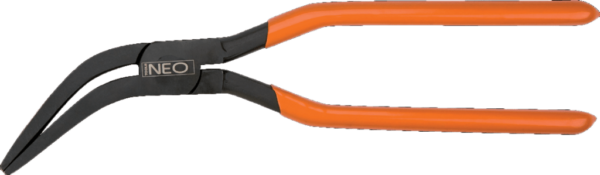
Since the work is carried out at a height, we need to take care of the availability of ladders and hinged ladders along which we will move.
It is also important to have personal protective equipment. At least - a safety system with a mounting belt and a helmet to protect the head from fragments of tiles.
Preparatory stage
Ceramic roof tiles are very demanding on the quality of the base on which they are fixed. That is why, in order to obtain a sealed and durable roof, you need to pay close attention to preparing the roof slopes for the installation of ceramic tiles.
Of course, this instruction is not a dogma: the design of the crate and waterproofing system may differ from the one proposed.But this is the case when it is worth experimenting only if you have enough experience to evaluate the consequences of a particular change in the project.
Installation of tiles
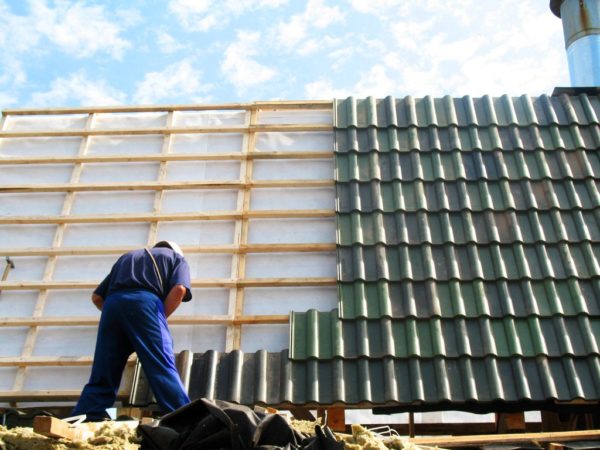
The very laying of ceramic tiles requires accuracy and maximum precision. The easiest way to fix it is with self-tapping screws through the technological holes, but sometimes special brackets are also used for fixing.
This is the most common method of installing ceramic roofing. In some cases, other techniques can be used, but for a start it is desirable to master the "classical" technology.
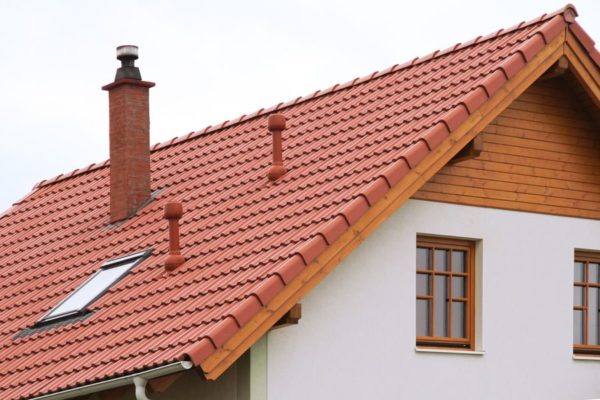
Conclusion
Ceramic tiles are beautiful and durable, but at the same time expensive and difficult to install material. To cope with it, it is advisable not only to read the tips given and study the video in this article, but also to practice. In addition, beginners (and not only) masters can always get advice by asking a question in the comments.
Did the article help you?