Why is metal seam roofing now experiencing a rebirth? Let's figure out together how the seam roofing is arranged, why it is so loved, what materials are used and what types of seam joints exist. And at the same time, I will tell you step by step with pictures about my own experience of installing such a roof.
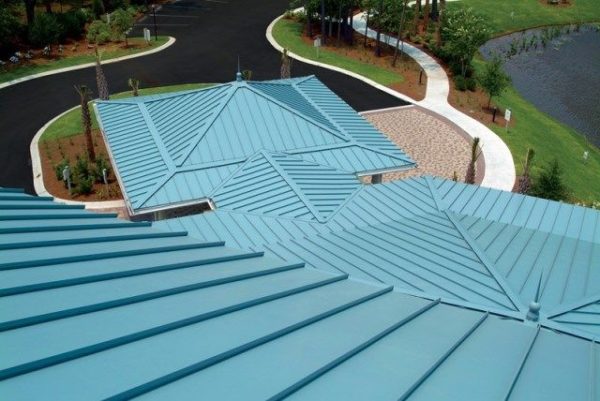
Theoretical part
To be precise, seam roofing is not a type of roofing, but rather a way of connecting metal sheets or strips together. Thanks to this technology, you get a monolithic, completely sealed metal coating without holes from self-tapping screws, nails and other fasteners.
If we explain in a nutshell the device of a seam roof, then it looks something like this: two adjacent metal sheets at the junction, figuratively speaking, are twisted together and then this twist is pressed.
The technology itself came to us from Germany more than 100 years ago, and with it the name came, the fact is that in German "falzen" means the verb to bend or bend.
In the past, iron roofing was insanely expensive because everything had to be done by hand. But after relatively inexpensive equipment and devices were used for the manufacture of seam roofing, the cost of work fell significantly and this type of coating became affordable for almost everyone.
Seams on the roof can be crimped both manually and with the help of a special apparatus.
Let's understand the terms
- Paintings - this is how professionals call metal sheets or strips, which actually cover the roof;
- Falz - this is the same twist between two adjacent sheets of roofing material, it is the folds that immediately catch the eye in the photo and are considered the hallmark of such roofs;
- Kleimer - a small bracket designed to fasten metal sheets to the roofing sheathing.
Types of seam connection
The instruction requires that the slope of such a roof be at least 10º, while the optimal slope is 30º–35º, but when arranging a double standing seam, the roof slope no longer plays a special role, it can actually be anything.
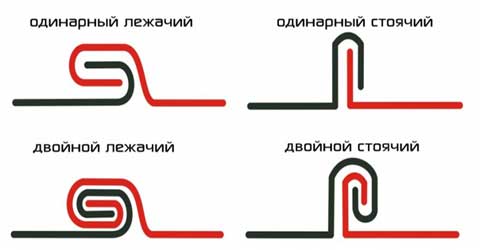
- The connection with a single standing seam is considered the simplest, here the edge of one sheet is bent at 90º, and the edge of the adjacent sheet goes around and clamps this threshold. For a novice master, this is the most suitable option;
- A double standing seam is an improved version of a single fold, only in this design the edges of adjacent sheets are twisted into 2 turns. Such a docking is considered the most reliable and airtight, but without a special tool it is not realistic to equip this connection with high quality;
- Single and double recumbent folds differ from standing folds only in that they are bent to the side (lying);
Standing folds are usually mounted parallel to the movement of water from the roof, and recumbent options are used for horizontal joining of 2 sheets, that is, perpendicular to the precipitation. Simply put, if the length of the sheet is not enough for the entire plane of the roof, then the missing sector from the bottom is attached with a recumbent fold.
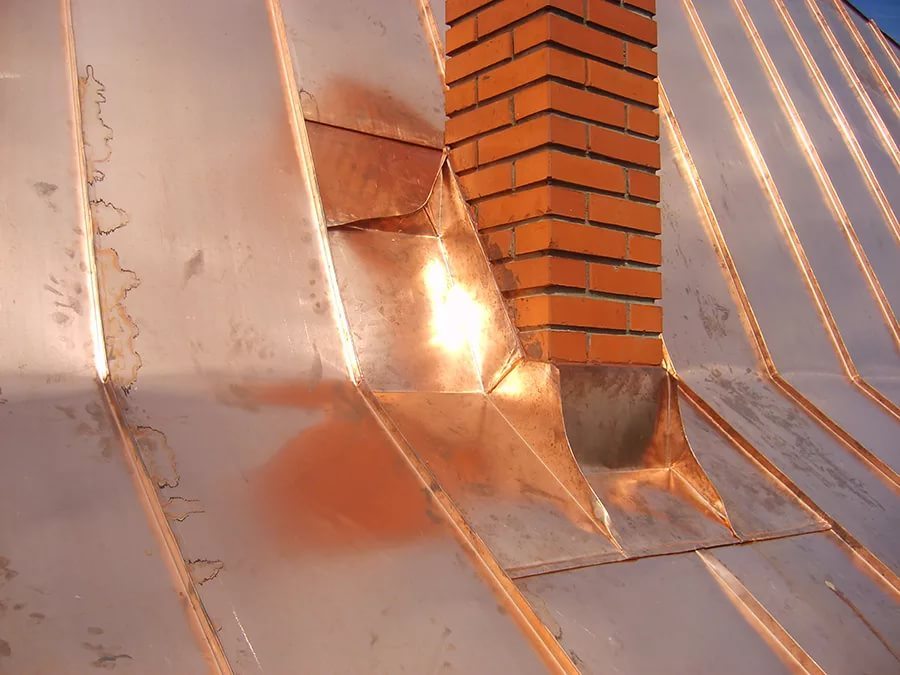
- There is also a clickfold - this is a self-latching design, on one side there is a kind of “tooth”, and the adjacent side, clinging to this tooth, snaps into place, ideal for homemade ones. But the technology appeared relatively recently, and so far its reliability has to be judged by advertising texts.
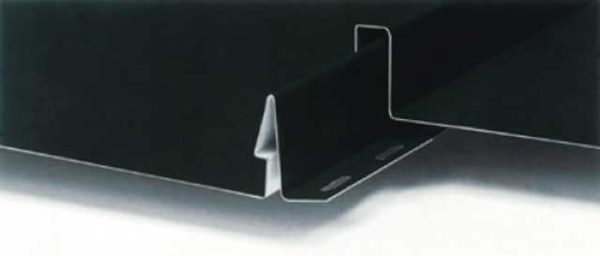
What kind of metal roofs are covered
Steel. Cold-rolled sheet steel is traditionally considered the patriarch of this direction, it all started with it. Previously, it was simply painted, now there are painted paintings, galvanized paintings and galvanized paintings with polymer coating.
The first 2 options will not last long, they are afraid of mechanical damage, for example, a branch that has fallen on the roof and acid rain, and galvanization coated with pural, polyester or plastisol can stand up to 50 years without repair.
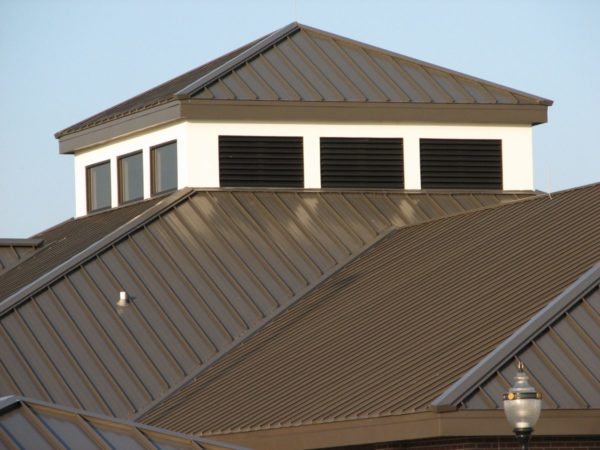
Copper. This is the most expensive seam roof, but the copper sheet is worth the money. If you cover a copper sheet with a layer of patina, then your roof will shine for decades, but even without a patina, copper oxide forms a strong film on the surface, although there will be no such shine.
In addition, no acid rain or scratches on the copper roof are terrible. Installation of a seam roof made of copper is easier to perform than, for example, steel, since copper itself is much softer.
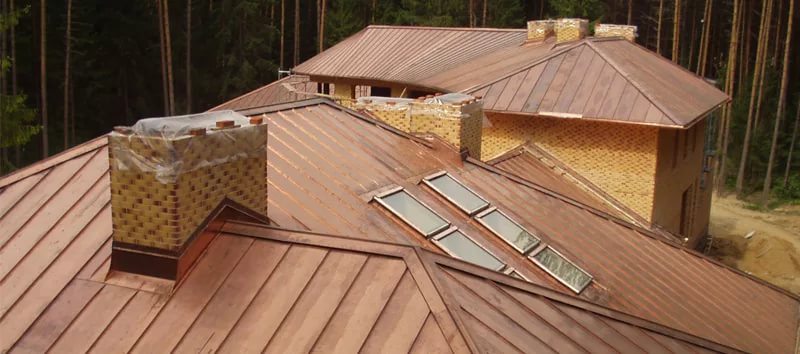
Zinc-titanium. This alloy appeared on the roofs of Western countries back in the seventies of the last century; such a silver-gray seam roof immediately captivates with its beauty.
But it did not take root in our country: firstly, the installation of zinc-titanium roofing requires a professional approach, and secondly, its price is slightly lower than for copper. Plus, the service life is about 50 years, which is quite comparable with good steel roofs.
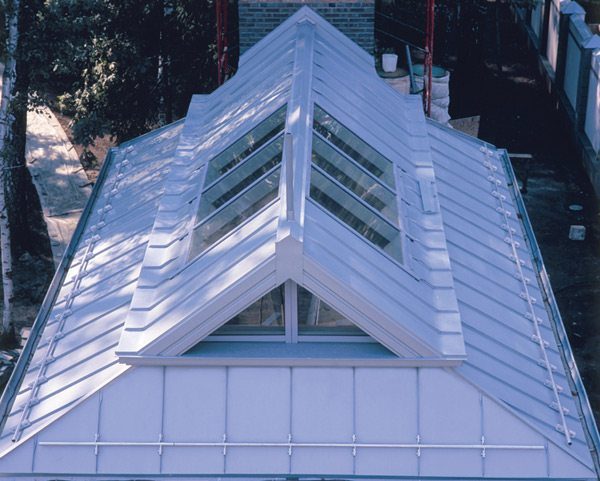
Aluminum. Aluminum roofing is more expensive than steel roofing, but cheaper than copper roofing.This metal does not rust, is not afraid of mechanical damage and aggressive chemicals, and most importantly, aluminum is much lighter than its competitors.
The only negative is the high coefficient of expansion when heated, but with high-quality installation, this does not matter.
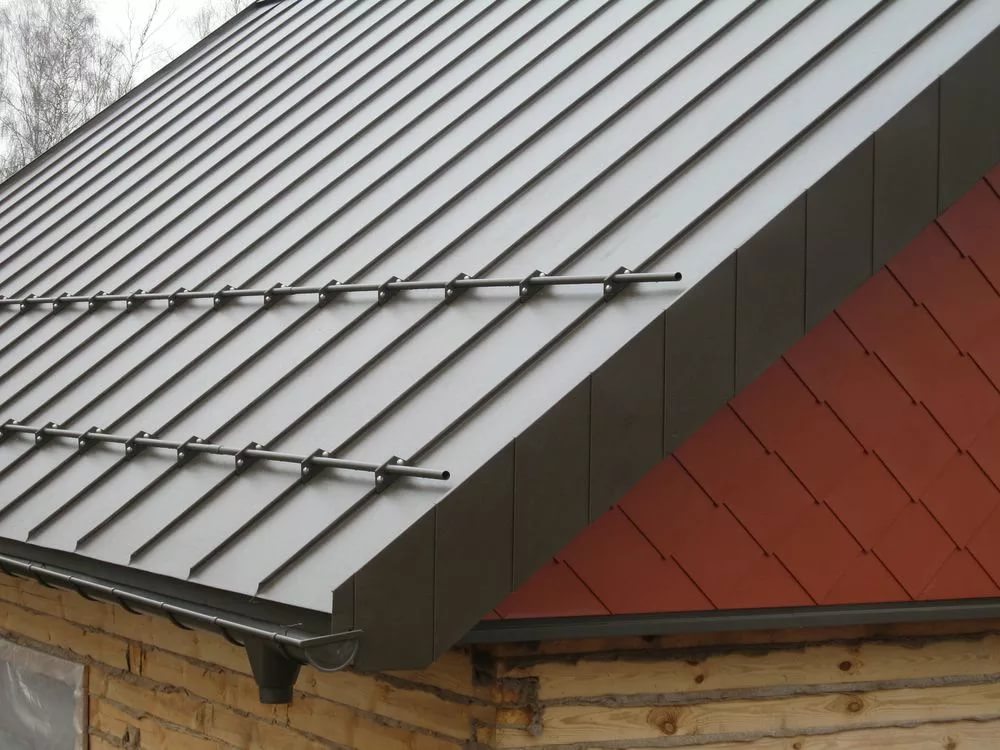
Now there are pictures on the market made of aluminum alloys with zinc, as well as titanium with zinc and copper, but it is too early to talk about them seriously, they have not passed the test of time, and advertising promises are not always true.
A few words about the pros and cons
The advantages here are quite significant:
- Whole sheet. The first and perhaps the main advantage is the solidity of the roof. With a quality connection with a double standing seam, you, in fact, get a solid sheet of metal without breaks and mounting holes;
- Light weight. The maximum thickness of the metal is 1.2 mm, but in most cases sheets with a thickness of 0.5–0.8 mm are used, therefore, such a roof will be the lightest among competitors;
- smooth finish. Snow practically does not linger on a flat and smooth metal surface, but there is a nuance here: due to the danger of uncontrolled snow melting, it is necessary to install snow retainers on the seam roof; in the west, such a house will not be insured without them;
- Durability. Even in economy class models, for example, polymer-coated steel, the warranty starts from 25 years, and copper roofs, according to manufacturers, can stand for 100 years;
- Fire safety. The metal does not burn and does not support combustion.
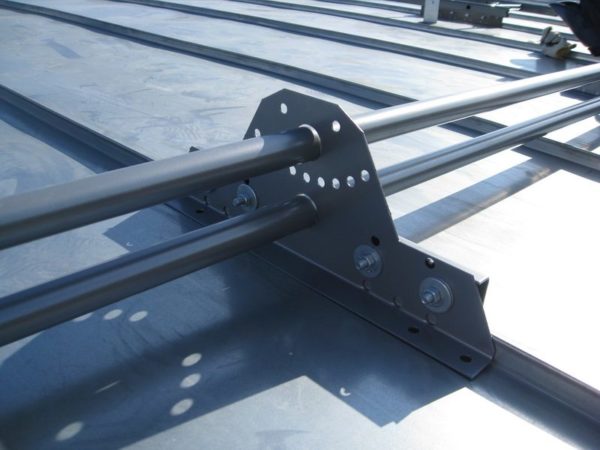
The most notable cons are:
- Noise. Indeed, raindrops will drum on thin metal quite loudly. Now this problem is solved with the help of a soundproofing substrate;
- lightning rod. Any folded roof should be grounded, and ideally, it is desirable to install a lightning rod spire on the ridge, because with such a quadrature, the probability of a lightning strike into metal increases significantly;
- Preparation. To make a folded picture, you need a special rolling machine, plus a highly specialized tool is required to crimp the folds. But with the current level of service, everything is easily solved, paintings can be ordered, and the instrument can be rented, I checked it myself.
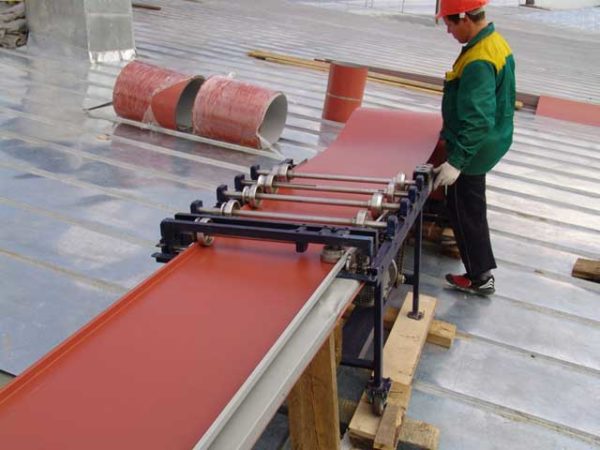
How to cover the roof with iron
The profession of a tinsmith (metal roofing specialist) has always been highly valued, and believe me, for good reason. Laying a folded roof with your own hands is possible, but you should not aim at large areas and complex structures, I personally studied in a small bathhouse, which I will talk about later.
Conclusion
Of course, a metal seam roof will cost you more than, for example, the same slate, but this coating is from the category of those that you did and forgot about the problem for at least 20-30 years. In the video in this article, you will find a lot of subtleties and nuances on the topic of seam roofs. If you have any questions, write in the comments, I can help.
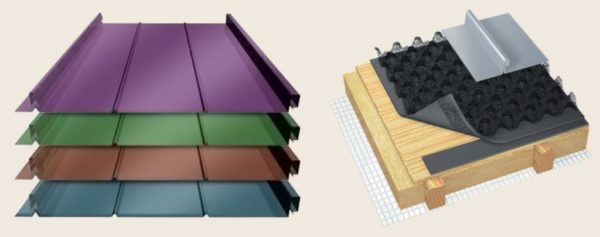
Did the article help you?